2D LiDAR Sensors: A Key to Customized and Cost-Effective Solutions
- Share
- publisher
- Zoe
- Issue Time
- Sep 28,2024
Summary
LD-05D and LD-20D 2D LiDAR sensors offer a 5-meter and 20-meter scanning range with a 270-degree field of view for precise object detection and environmental perception in industrial automation. These rugged sensors provide consistent measurement quality in demanding environments.
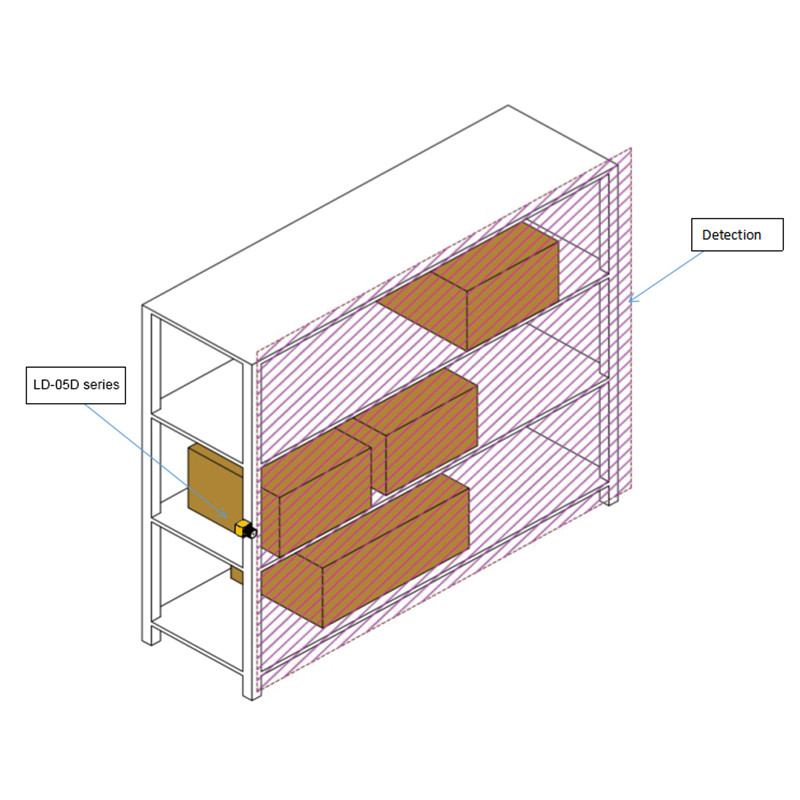
High-Performance Overview of 2D LiDAR Sensors
2D LiDAR sensors provide exceptional on-site evaluation and measurement data output in a compact housing. Whether used in mobile or fixed applications, automation, monitoring, or safety, these sensors offer 5-meter and 20-meter scanning ranges with a 270-degree field of view, allowing for precise detection across vast areas. They maintain consistent performance regardless of surface type or reflectivity, seamlessly covering their entire scanning range with the LD-05D and LD-20D, ensuring consistently high measurement quality. Their robust structure and high-quality connectivity make them suitable for various industries and demanding applications, while also facilitating easy installation and parameter settings.
Applications and Flexibility
As compact data providers for environmental perception and object detection, or as highly flexible tools in industrial environments and building automation, 2D LiDAR sensors are highly capable. They are suitable for autonomous mobile robots (AMRs), service robots, and industrial trucks on mobile platforms. These sensors offer custom and cost-effective solutions for nearly any requirement.
2D LiDAR Technology Principles
LiDAR uses an optical time-of-flight measurement method to scan the surrounding environment. It emits laser pulses through an internal rotating mirror and detects their reflections; the longer the time taken for the laser pulse to return, the further away the detected object is. By combining the signal strength (which depends on the material of the object and affects reflectivity), it is possible to determine the object's position in space with millimeter precision. The LD-05D and LD-20D update their surroundings at a frequency of 15 times per second with an angular resolution of 0.1°, enabling real-time positioning, navigation, and control.
Dual Protection for On-Site Evaluation and Measurement Data Output
The LD-05D and LD-20D can detect whether objects are within predefined areas, with the device presetting 16 groups of areas, each containing 3 sub-areas. This design allows users to quickly adjust settings during operation. To further enhance process reliability, users can customize the geometric shape of individual areas or reference contour areas for static contour monitoring.
2D LiDAR Sensors Typical Use Case: Protrusion Detection
Protrusion detection is used to identify whether goods are encroaching on detection planes, preventing potential falls.
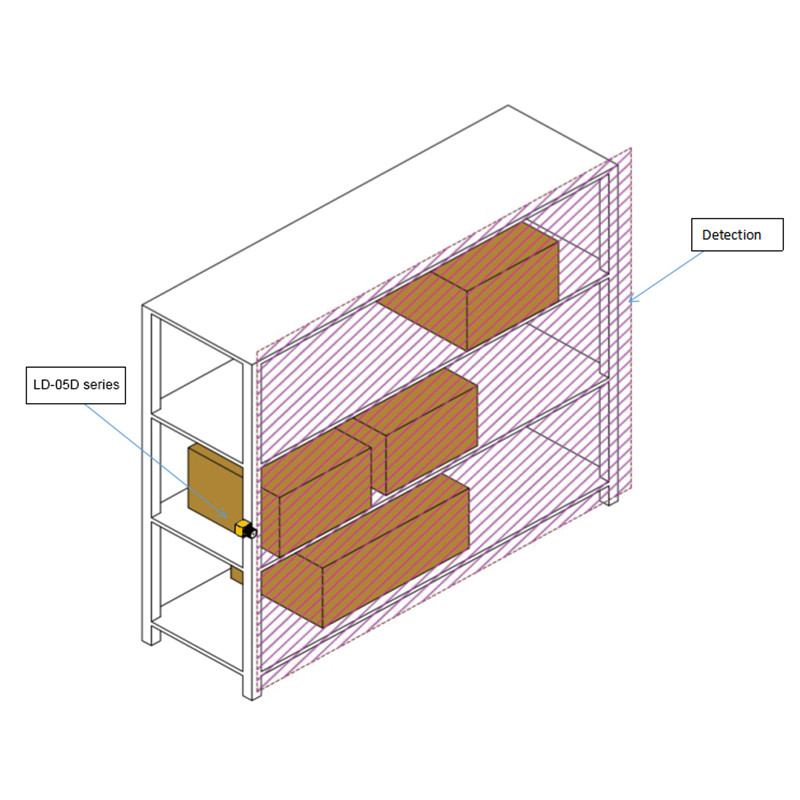
Application Scenarios:
In heavy-duty racks (also known as "pallet racks"), typically over six meters high (approximately three stories), there is a risk of “falling objects.” The scanning plane of the 2D LiDAR should cover the front side of the racks. When the 2D LiDAR scans, if pallets are improperly stacked on the racks and protrude, the integrated monitoring system should promptly alert staff to make adjustments, preventing items from falling and causing personal injuries.
The LD-05D can also be used for protrusion detection on horizontal surfaces, with users able to configure it as needed.
Compact 2D LiDAR sensor: Customized and Cost-Effective Solutions
Technical data
|
||||
Working principle
|
Time-of-flight (TOF) measurement principle |
|||
IO output | NPN or PNP | |||
Work area | 0.05 m ~ 5 m | 0.05 m ~ 20 m | ||
Laser source
|
905 nm (class I) |
|||
Aperture angle
|
270° |
|||
Scanning frequency | 15 Hz / 30 Hz | |||
Angular resolution | 0.1° / 0.3° | |||
Self-learning function | Automatically scan the environment and generate areas | |||
Electrical connections | Db15 Male / Scatter | |||
Supply voltage | DC 9 V ~ 28 V | |||
Power consumption | 2 W | |||
Switch drive | DC 30 V 50 mA max. | |||
Shell color | Yellow | |||
Enclosure rating | IP65 | |||
Weight | 150 g (cable not included) | |||
Dimensions (L × W × H) | 50 × 50 × 76 mm | |||
Detectable object shape | Almost any shape | |||
Measurement error | ±30 mm | |||
Number of field sets | 16 fields, 3 simultaneous protective fields (per field set) | |||
Connection type | Micro-USB | |||
Input | GND/NC × 4 | |||
Switch output | NPN × 3, device working status; PNP × 3, device working status | |||
Delay time | 100 ms ~ 10,000 ms (configurable), typical value 330 ms | |||
Response time | 15 Hz: 67 ms ~ 29,949 ms (configurable), typical value 134 ms; 30 Hz: 33 ms ~ 29,997 ms (configurable), typical value 66 ms | |||
Status Indicator | Status indicator × 1, area group indicator × 3 | |||
Vibration resistance
| 10 - 55 Hz, amplitude 0.75 mm, XYZ three-axis, 2 hours per axis;
50 - 200 Hz, 196 m/s² (20G), scanning speed 2 min/cycle, XYZ three-axis, 2 hours per axis; | |||
Ambient operating temperature | -10 ℃ ~ +55 ℃ | |||
Storage temperature | -30 ℃ ~ +75 ℃ | |||
Ambient light immunity | >15,000 lux |