Application case | The Importance of Installing Safety Light Curtains on Stamping Presses
- Share
- publisher
- Zoe
- Issue Time
- Jul 23,2024
Summary
DADISICK's QCE series safety light curtain offers a variety of beam spacing options, including 10 mm, 20 mm, 30 mm, 40 mm, 80 mm, and 200 mm, with a detection range from 0.3 meters to 6 meters. This light curtain is flexible enough to meet different protection needs, including finger protection, hand protection, and body protection. It has been widely used in mechanical manufacturing, automated production lines, and all hazardous work environments that require a high level of safety protection.
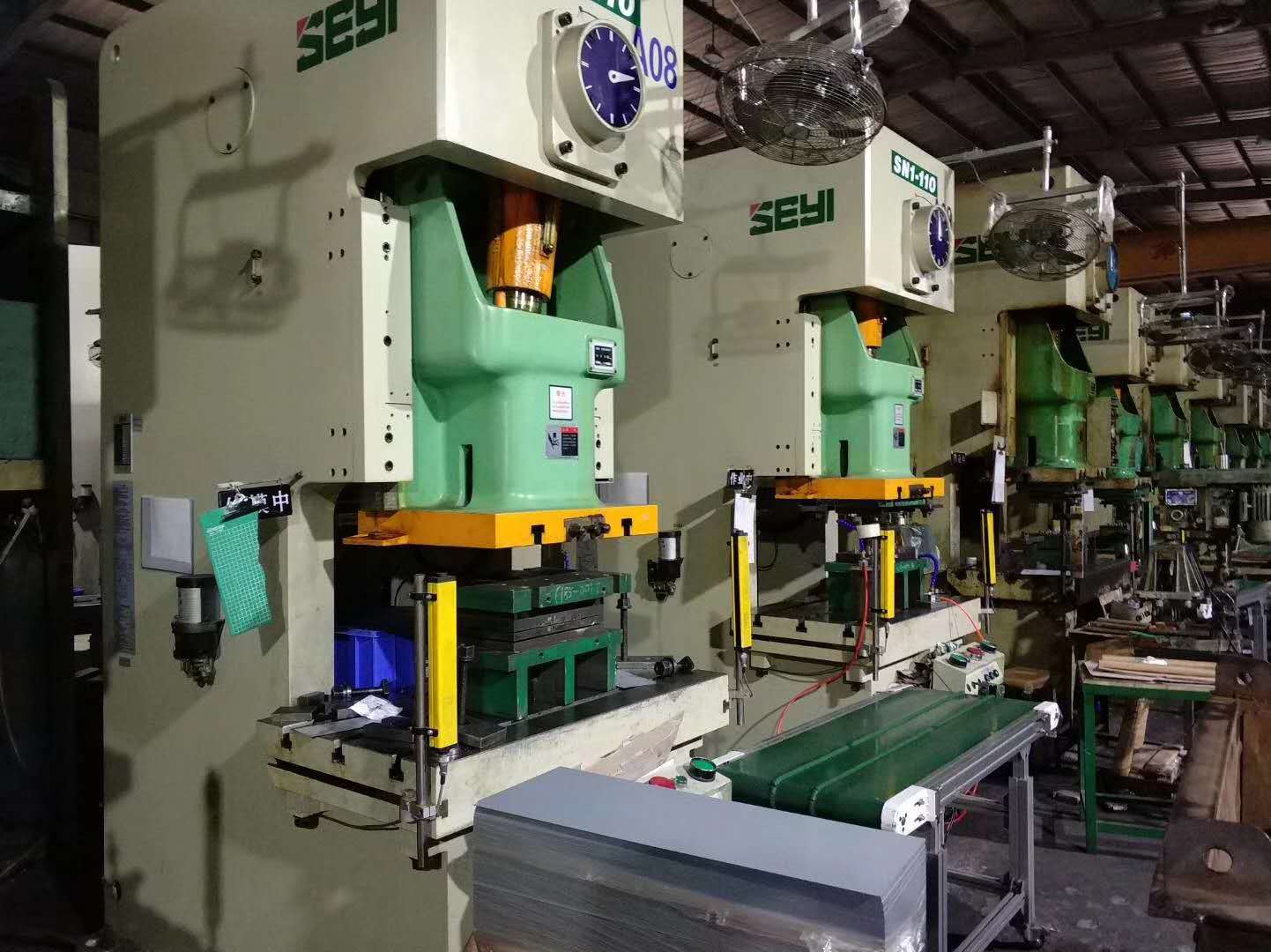
The Importance of Installing Safety Light Curtains on Stamping Presses
A stamping press, also known as a punch press or forging press, is a machine that uses pressure to deform metal and shape it into various structures. Its functions include shearing, forming metal materials, deep drawing, and forging metal. It typically works with molds and is an essential piece of equipment for producing metal mechanical parts.
Stamping Press Safety Solutions
Customer Needs Analysis
Worker safety is crucial during the operation of stamping presses. One of the core concerns for our clients is that when a worker's hands or other body parts get close to the press's working area, the machine must be able to stop quickly and reliably to prevent accidents. To achieve this goal, we need to design a safety protection system that is efficient, responsive, and compliant with safety standards.
This solution uses a combination of a safety light curtain and a safety relay to create an effective safety protection system for monitoring and immediately protecting the stamping press's operation area. The system employs non-contact detection technology that automatically triggers a shutdown mechanism when a worker gets too close to the hazardous area, ensuring their safety.
System Components and Working Principle
1. Safety Light Curtain
Selection and Installation: Choose the appropriate model of safety light curtain based on the stamping press's size, working range, and environment. The light curtain should be installed in front of the stamping press's working area to create an invisible protective barrier.
Working Principle: The safety light curtain consists of a transmitter and a receiver. The transmitter emits infrared beams, and the receiver picks up these beams. When an object (like a worker's hand) enters the light curtain area, the beams are blocked, and the receiver immediately detects a change in the signal.
2. Safety Relay
Role: The safety relay acts as a bridge between the safety light curtain and the stamping press control system. It receives safety signals from the light curtain and controls the start and stop of the stamping press based on the signal's status.
Working Principle: When the safety light curtain detects an object entering the hazardous area, it sends a stop signal to the safety relay. Upon receiving the signal, the safety relay immediately cuts off the power or control signal to the stamping press, stopping the machine.
3. Control System Integration
Integrate the safety light curtain and safety relay with the stamping press control system to ensure accurate signal transmission and response speed.
The control system should support self-diagnostic functions, automatically shutting down and alarming in case of a malfunction in the safety light curtain or safety relay, prompting maintenance personnel to check.
System Advantages
1. High Sensitivity and Reliability: The safety light curtain uses high-precision infrared detection technology, allowing it to quickly respond to a worker's approach, ensuring the machine stops in time before any danger occurs.
2. Non-contact Protection: There’s no need for workers to wear any extra gear, which simplifies operations and boosts efficiency.
3. Easy Installation and Maintenance: The system has a simple structure, making installation a breeze and keeping maintenance costs low.
4. Compliance with Safety Standards: It meets international and domestic safety standards, such as ISO 13855 and GB/T 19574, ensuring safety and compliance during production.
Implementation Steps
1. Site Survey and Requirement Confirmation: Understand the model of the stamping press, work environment, and customer needs to determine the specific configuration of the safety light curtain and safety relay.
2. System Design and Equipment Selection: Based on the survey results, design a safety protection system plan and choose the appropriate equipment.
3. Installation and Debugging: Install and debug the safety light curtain and safety relay to ensure the system operates correctly.
4. Training and Maintenance: Provide training for operators on how to use the system and establish a maintenance plan to ensure long-term stable operation.
Recommended Model
DADISICK's QCE series safety light curtain offers a variety of beam spacing options, including 10 mm, 20 mm, 30 mm, 40 mm, 80 mm, and 200 mm, with a detection range from 0.3 meters to 6 meters. This light curtain is flexible enough to meet different protection needs, including finger protection, hand protection, and body protection. It has been widely used in mechanical manufacturing, automated production lines, and all hazardous work environments that require a high level of safety protection.
Related Products
Beam spacing: 20mm
Number of optical axes: 40
Protection height: 780mm
Light barriers outputs (OSSD)2 PNP
The safety light curtain are fixed on support,and then debug according to the specific situation.
Reliable installation for light curtain, quick and easy adjustment, strong design, suitable for harsh industrial environment.