Application of CSB18 Ultrasonic Sensors in Roll Diameter Monitoring
- Share
- publisher
- Zoe
- Issue Time
- Sep 13,2024
Summary
In modern automated production lines, real-time monitoring of roll diameter is crucial for ensuring continuous production. This solution utilizes DADISICK’s CSB18 series ultrasonic sensors, which, through advanced performance and intelligent control systems, continuously and accurately monitor the diameter of various materials—including transparent, glossy, colored, black, and metalized materials—while automating the roll replacement process.
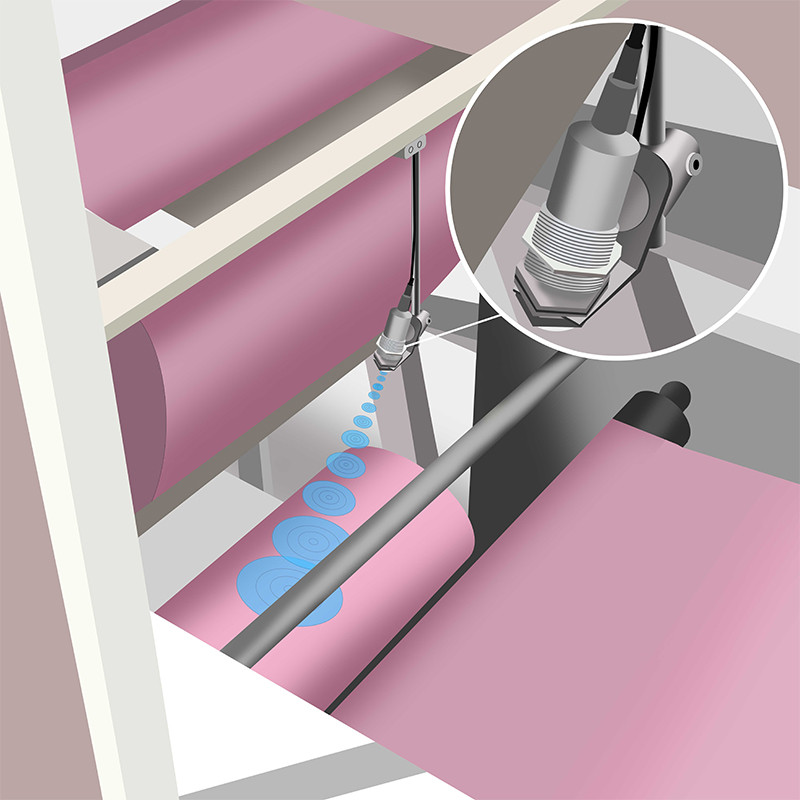
Application of CSB18 Ultrasonic Sensors in Roll Diameter Monitoring
In modern automated production lines, precise monitoring of roll diameters is not only a critical factor for ensuring continuous production but also essential for maintaining high product quality. This solution utilizes DADISICK’s latest CSB18 series ultrasonic sensors, which, through advanced performance and intelligent control systems, can continuously and accurately monitor the diameter of various materials (including transparent, glossy, colored, black, or metalized materials), while automating the roll replacement process. This significantly enhances production efficiency and reduces costs.
In practical applications, as shown in the image below, the CSB18 ultrasonic sensor measures roll diameter in real-time using non-contact technology. The blue wave lines in the illustration represent how the ultrasonic sensor emits sound waves and receives reflected signals to precisely measure the roll diameter. This method avoids issues such as wear or contamination associated with traditional contact measurement, providing a highly reliable roll diameter monitoring solution for automated production lines.
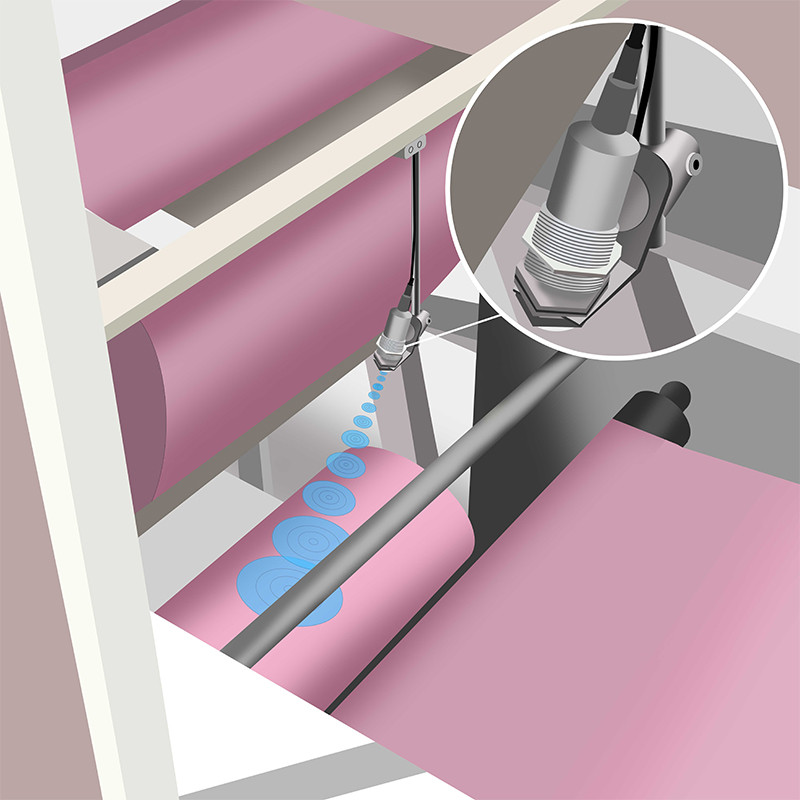
Core Components and Technical Features
Non-contact Measurement: Utilizing ultrasonic technology, the sensor measures without direct contact with the roll surface, preventing measurement errors caused by wear or contamination.
Broad Adaptability: The CSB18 series sensor can penetrate transparent, colored, and metalized materials, and it continues to operate stably even in extreme environments, making it suitable for industries such as packaging, printing, and more.
Continuous Analog Output: It provides precise current or voltage signals that reflect changes in roll diameter in real-time, allowing machine controllers to maintain accurate control.
High Reliability: Advanced signal processing algorithms effectively suppress environmental interference, ensuring the accuracy and stability of the measurement data.
Models
|
CSB18-300 |
CSB18-500
|
CSB18-1000
|
Detection range | 30-300 mm | 50-500 mm | 60-1000 mm |
Blind zone
|
0-30 mm |
0-50 mm
|
0-60 mm
|
Resolution
|
0.1 mm |
0.15 mm
|
0.17 mm
|
Response time | 22 ms | 32 ms | 52 ms |
Switching hysteresis | 2 mm | 2 mm | 2 mm |
Switching frequency | 45 Hz | 31 Hz | 19 Hz |
Repeatability: ±0.15% of full-scale value | |||
Absolute accuracy: ±1 % (built-in temperature drift compensation) | |||
Input type: With synchronization and learning function | |||
Output type: Switch output; IO-Link output; Analog output; Digital output RS485 | |||
Material: Copper nickel plating , plastic fittings , glass filled epoxy resin | |||
Connection type: 5-pin M12 connector | |||
Protection Class: IP67 | |||
Ambient temperature: -25°C~+70°C (248~343K) |
Intelligent Control System
Data Acquisition and Processing: The system integrates an efficient data acquisition module that processes sensor signals in real-time, displaying reel diameter data in a simplified numerical format for easy monitoring.
Warning and Alarm Mechanisms: The system is programmed with upper and lower diameter thresholds. When the reel diameter falls below the preset value, it triggers a warning signal. If it continues to decrease to a critical level, the system issues an emergency alarm and initiates the reel replacement process.
Automated Management: By linking with robotic arms or automatic feeding systems, the system enables automatic reel replacement, minimizing manual intervention and boosting production efficiency.
Remote Monitoring and Diagnostics: Equipped with remote access capabilities, the system allows management to view production status in real-time, perform diagnostics, and make adjustments remotely.
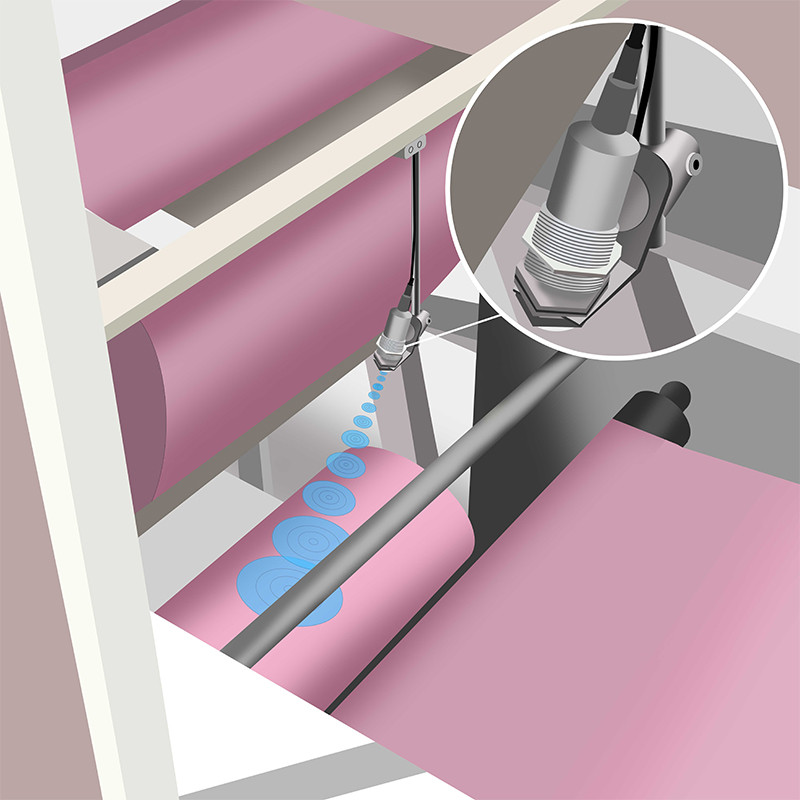
Implementation Steps:
1️⃣ Requirement Analysis: Define the specific requirements of the production line, including reel type, diameter range, and replacement frequency.
2️⃣ System Design and Selection: Choose appropriate sensors and control systems based on the requirements and design the system architecture.
3️⃣ Installation and Commissioning: Install and commission the sensors on the production line, ensuring measurement accuracy and system stability.
4️⃣ System Integration and Testing: Seamlessly integrate the sensor monitoring module with the production line control system and conduct comprehensive tests to ensure that all functional modules work together effectively.
5️⃣ Training and Maintenance: Train operators on system operation and maintenance, and establish a regular maintenance plan to ensure long-term system stability.
System Advantages
✅ Increased Production Efficiency: The automated monitoring and reel replacement mechanism reduces downtime, ensuring continuous production.
✅ Cost Reduction: By minimizing reel overuse or premature replacement, the system helps reduce waste and lowers labor maintenance costs.
✅ Improved Product Quality: The system ensures that reels are used under optimal conditions, preventing production defects caused by insufficient diameter.
✅ Enhanced Flexibility: Compatible with various reel materials and sizes, it meets diverse production requirements.
✅ Easy Integration and Maintenance: With a modular design, the system can be easily integrated into existing production lines. Additionally, it offers convenient maintenance interfaces and detailed operation manuals to reduce maintenance difficulty.
Related Ultrasonic Sensors
Detection range: 20-120 mm
Detection range: 20-200 mm
Material: copper nickel plating
Connection type: 4-pin M12 connector
Detection range: 30-300 mm, 50-500 mm, 60-1000 mm
Material: copper nickel plating, plastic fittings
Connection type: 5-pin M12 connector
Detection range: 100-2000 mm, 200-4000 mm, 350-6000 mm
Material: copper nickel plating, plastic fittings
Connection type: 5-pin M12 connector
Emitter - receiver spacing: 20-40 mm, 20-60 mm, 20-100 mm
Material: nickel plated copper, plastic fittings
Connection type: 2 m, PVP cable, 0.14 mm²