Application of Measuring Light Curtain in Automatic Counting and Packaging Monitoring of Small Screws
- Share
- publisher
- Vicky
- Issue Time
- Sep 24,2024
Summary
The application of measuring light curtains in counting small objects ensures accurate counting of each small object through precise beam detection and pulse stretcher functions. It not only improves counting accuracy, but also significantly improves production efficiency and packaging quality. With the development of automation technology, measurement light curtains will play a key role in more industrial fields, helping companies achieve efficient and accurate production processes.
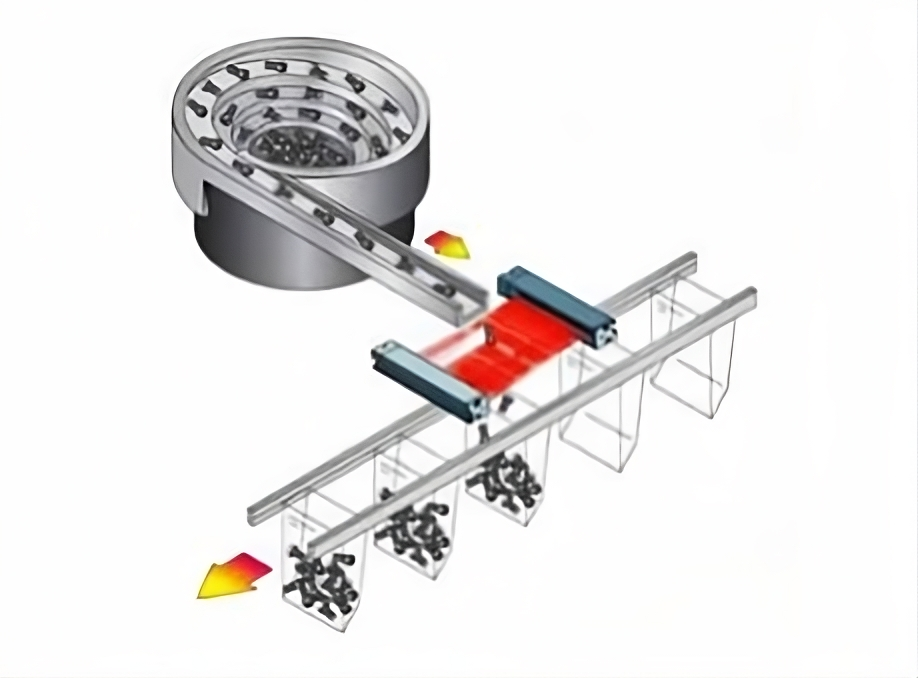
In modern automated production lines, accurate counting and monitoring are key links to ensure product quality and production efficiency. Especially in the production and packaging process of small items such as small screws, traditional manual counting is not only inefficient but also prone to errors. For this reason, the introduction of light curtain counting system has become an efficient and accurate solution. This article will introduce in detail how the measurement light curtain is used to count and monitor small screws from the supply barrel to the plastic bag packaging process, especially the technical details of improving the counting accuracy by integrating a 5 millisecond pulse stretcher.
Measuring Light Curtain Counting System Overview
The light curtain counting system consists of two parts: the transmitter and the receiver, which are installed in parallel on both sides of the path through which the detected object passes. The transmitter emits infrared light or laser beams to form one or more light curtains. When an object passes through the light curtain, it will block part of the beam, causing the light signal received by the receiver to change, thereby triggering the counting signal. The system is non-contact, high-speed, and accurate, and is very suitable for counting small objects.
Application Scenarios of Measuring Light Curtains in Small Screw Counting
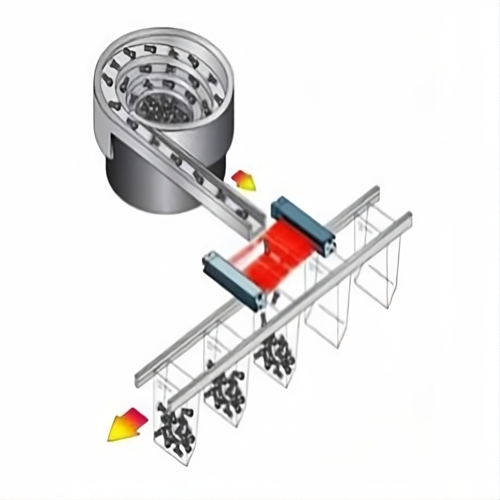
Feeding and conveying
The small screws are transported from the feeding barrel to the top of the packaging area in an orderly manner through a vibrating plate or a pneumatic conveying system.
Light curtain arrangement
At the end of the conveying path, where the small screws are about to fall into the plastic bag, a light curtain system is installed. Adjust the spacing and sensitivity of the light curtain to ensure that each small screw can be accurately detected.
The role of the pulse stretcher
Due to the small size and high speed of small screws, direct counting may cause omissions or miscounts due to too short signals. Therefore, a 5 millisecond pulse stretcher (off delay) is integrated at the output end of the receiver, that is, each screw passing signal detected is extended to 5 milliseconds, which effectively avoids counting errors caused by short-term signal fluctuations or interference, and improves the stability and accuracy of counting.
Advantages of Measuring Light Curtain Counts
Real-time counting
Every time a small screw passes through the light curtain, the signal after pulse broadening processing is received and accumulated by the counter to achieve real-time counting.
Packaging monitoring
The number of small screws required for each bag is preset. When the count reaches the preset value, the system automatically triggers the packaging action (such as closing the plastic bag mouth) and resets the counter to prepare for the next round of counting.
Abnormal alarm
If an abnormal situation occurs during the counting process (such as continuous no count or count far exceeds the preset value), the system will issue an alarm to prompt the operator to check whether the feeding or conveying system is operating normally.
Application effect
On the small screw packaging production line, using a measuring light curtain to count screws can not only effectively improve the accuracy of production, but also significantly reduce human errors and waste in the packaging process. Monitor the packaging quantity in real time to ensure that the number of screws in each bag fully meets the set standards, thereby improving production efficiency.
DADISICK's Hot Selling Safety Light Curtains
Beam spacing: 20mm
Number of optical axes: 40
Protection height: 780mm
Beam spacing: 10mm
Number of optical axes: 102
Protection height: 1010mm
Safety curtain outputs (OSSD): 2 PNP
Beam spacing:40mm
Number of optical axes: 20
Protection height: 760mm
Safety Curtain outputs (OSSD):2 PNP
Beam spacing:40mm
Number of optical axes: 54
Protection height: 2120mm
Safety Curtain outputs (OSSD):2 PNP