Applications of Laser Displacement Sensors in In-Vehicle Seat Inspection
- Share
- publisher
- Zoe
- Issue Time
- Nov 9,2024
Summary
In the automotive manufacturing industry, quality control is a critical factor influencing vehicle safety and comfort. As an essential part of a vehicle's interior, the quality and performance of in-vehicle seats directly affect the comfort and safety of both drivers and passengers. In recent years, laser displacement sensors have become widely used in in-vehicle seat inspection due to their technical advantages, such as non-contact measurement and easy integration.
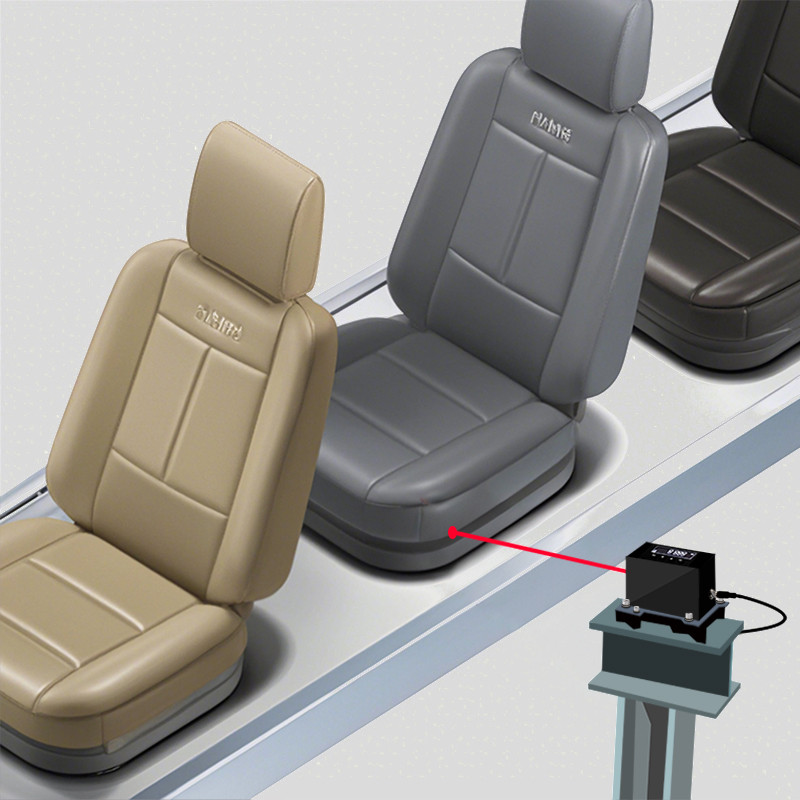
In the automotive manufacturing industry, quality control is a critical factor influencing vehicle safety and comfort. As an essential part of a vehicle's interior, the quality and performance of in-vehicle seats directly affect the comfort and safety of both drivers and passengers. In recent years, laser displacement sensors have become widely used in in-vehicle seat inspection due to their technical advantages, such as non-contact measurement and easy integration.
Working Principle of Laser Displacement Sensors
Laser displacement sensors operate based on the laser triangulation principle. They emit a laser beam onto the surface of the object being measured, then receive the reflected beam. By analyzing the reflection angle and displacement of the laser beam, the sensor precisely calculates the distance between the sensor and the object surface. This measurement method provides high accuracy, fast response, and non-contact advantages, enabling precise measurement of displacement, thickness, and surface contour without physically touching the object.
Applications of Laser Displacement Sensors in In-Vehicle Seat Inspection
Seat Height Measurement
During the production process, seat height is a key parameter. Traditional measurement methods often rely on tools like calipers, which involve contact measurement that is both time-consuming and may damage the seat surface. Laser displacement sensors, however, allow for non-contact measurement, enabling fast and accurate seat height measurements that enhance production efficiency and product quality.
Seat Backrest Angle Measurement
The backrest angle is essential for driver and passenger comfort. Laser displacement sensors measure the angle between the seat backrest and the seat base to verify that the backrest angle meets design specifications. This non-contact measurement method avoids potential damage to the seat and enhances measurement accuracy and reliability.
Seat Adjustment Mechanism Inspection
The seat adjustment mechanism is crucial for ensuring seat comfort and safety. Laser displacement sensors enable high-precision, real-time monitoring of parameters such as travel distance, speed, and applied force, ensuring that the adjustment mechanism meets performance standards. Additionally, the sensor can detect issues such as sticking or abnormal noise, thereby improving seat reliability and safety.
Seat Surface Contour Inspection
Laser displacement sensors can perform 3D scanning of the seat surface, capturing its shape and dimensions, which aids in seat design and manufacturing to improve comfort and fit. The sensor also detects surface defects, such as scratches or dents, which enhances product quality and appearance.
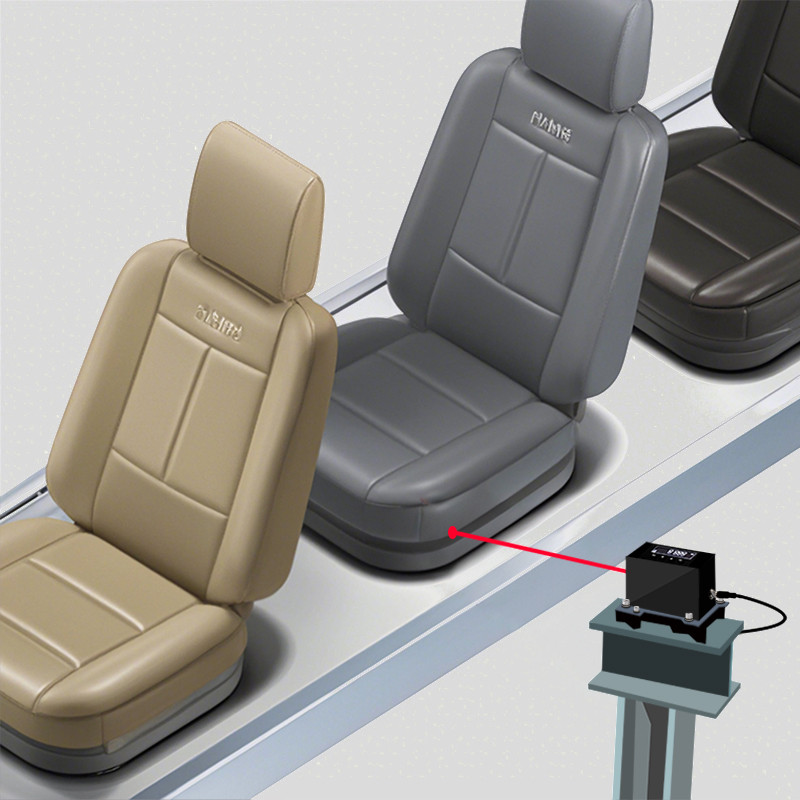
Technical Advantages of Laser Displacement Sensors
Non-Contact Measurement
Laser displacement sensors use a non-contact measurement approach, which effectively protects the surface of the measured object and is suitable for measuring objects of various materials and shapes. Non-contact measurement also eliminates issues like wear and deformation associated with traditional contact methods, improving measurement accuracy and reliability.
High-Precision Measurement
Laser displacement sensors offer high-precision measurement capabilities, allowing for the accurate detection of slight displacement changes. In in-vehicle seat inspection, these sensors can measure subtle changes in parameters like seat height, angle, and adjustment travel, ensuring that seat performance aligns with design standards.
High-Speed Measurement
Laser displacement sensors deliver fast measurement speeds, allowing quick measurements of the target object. In production lines, laser displacement sensors facilitate real-time monitoring, thereby increasing production efficiency and product quality.
Ease of Integration
Due to their compact size and lightweight, laser displacement sensors are highly adaptable for integration into various automated inspection systems. In in-vehicle seat inspection, they can be seamlessly integrated with robots and automated production lines, enabling automated inspection that significantly enhances inspection efficiency and precision.
Recommended Laser Displacement Sensors
Sensing Distance
|
Repeatability
|
Linearity |
Output
|
30 mm (±5)
|
10 µm
|
±0.1%F.S. |
Analog / RS485
|
50 mm (±15)
|
30 µm
|
NPN / Analog / RS485
|
|
100 mm (±35)
|
70 µm
|
||
200 mm (±80) | 200 µm | ±0.2%F.S. | |
400 mm (±200) | 400 µm / 800 µm |
Related Distance Sensors
Response time: up to 1.0ms
Repetitive accuracy: up to 2µm
Detection distance: 30mm
Detection range (f. s.): ±4mm
Output method: NPN/PNP+analog+RS485
Resolution: 1mm
Laser type: red semiconductor laser Class II laser 655+10nm<1m
Reaction time: 50-200ms
Measure distance: 0.1-50m
By converting from the laser into electrical signals. determine various characteristics,distance, displacement, or position.
Detection range: 100-2000 mm, 200-4000 mm, 350-6000 mm
Material: copper nickel plating, plastic fittings
Connection type: 5-pin M12 connector