Applications of Laser Displacement Sensors in Precision Position Control and Liquid Level Measurement in 3D Printing
- Share
- publisher
- Zoe
- Issue Time
- Aug 13,2024
Summary
A DADISICK laser displacement sensor is used to detect the height of liquid resin in a 3D printer, providing real-time output of liquid level data. Combined with a control system, it can automatically detect the height difference and perform differential compensation to maintain a constant liquid level in the resin tank.
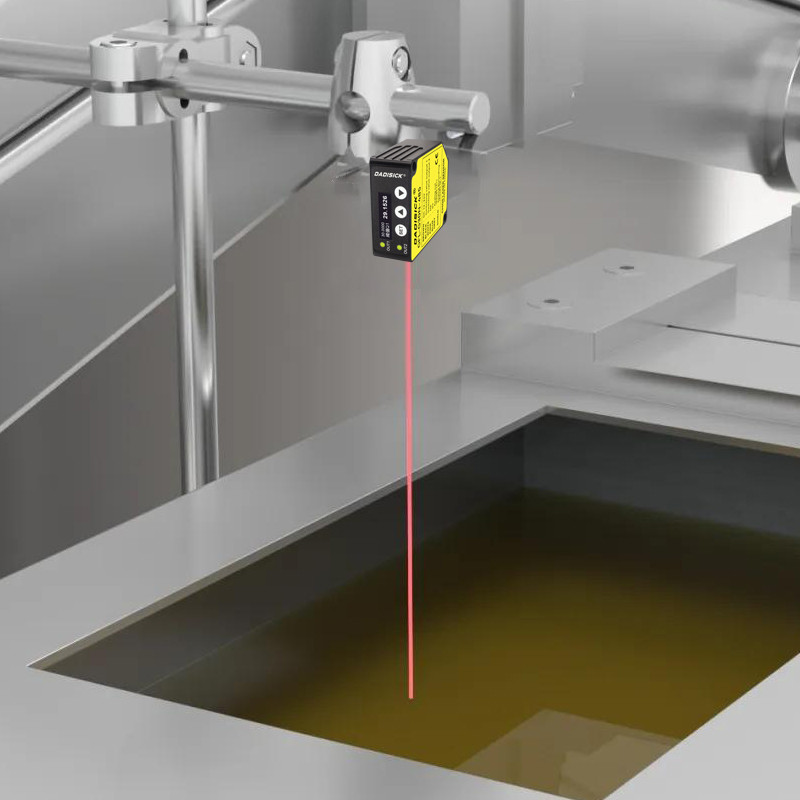
Applications of Laser Displacement Sensors in Precision Position Control and Liquid Level Measurement in 3D Printing
Three-dimensional printing (commonly known as Additive Manufacturing, AM) is a technology that constructs three-dimensional objects by adding material layer by layer. Unlike traditional subtractive manufacturing methods (such as cutting or grinding) or formative manufacturing methods (such as casting or forging), 3D printing can directly produce complex parts from digital models quickly and flexibly, without the need for molds or complex tooling fixtures. This characteristic makes 3D printing particularly advantageous in areas such as personalized customization, complex structure manufacturing, and rapid prototyping.
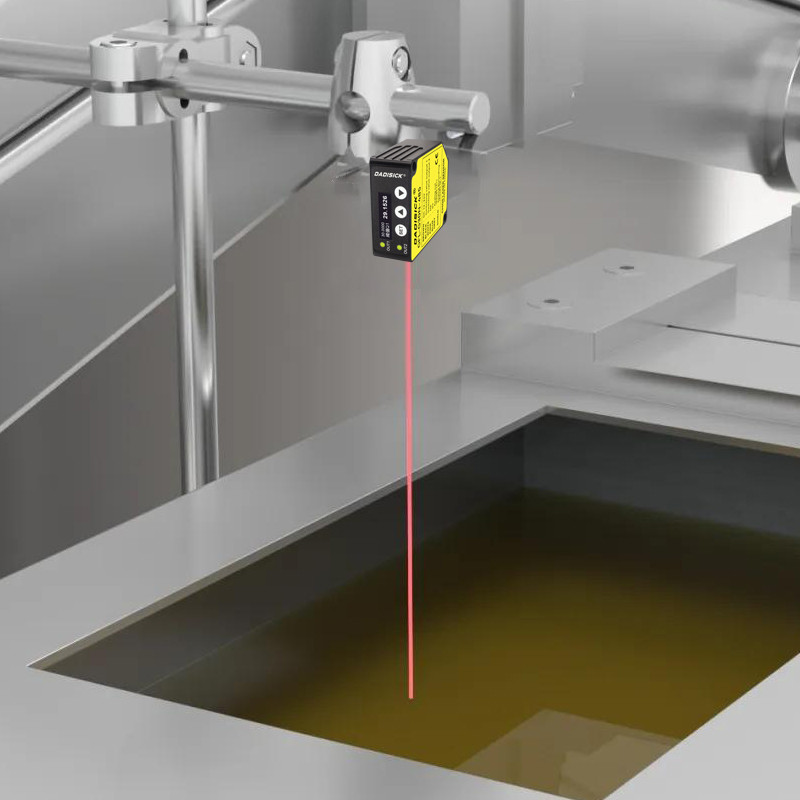
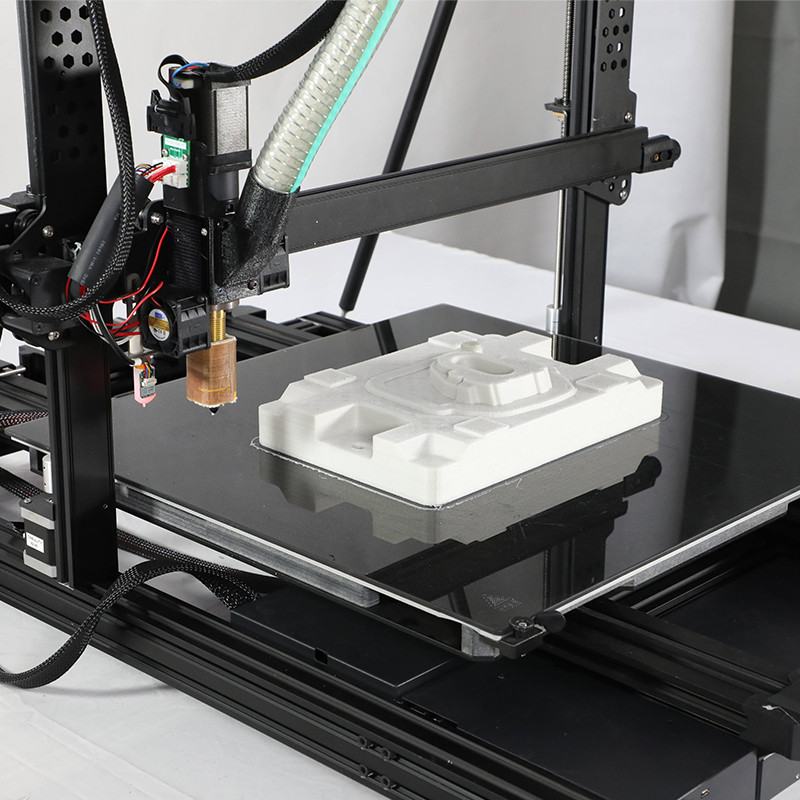
Among 3D printing technologies, photopolymerization is especially important, particularly stereolithography (SLA), digital light processing (DLP), and LCD photopolymerization. These technologies often employ various sensors during the printing process to ensure precision, stability, and safety.
SLA (Stereo Lithography Apparatus): Uses ultraviolet light as a light source, with a galvanometer system controlling the laser beam to scan and cure liquid resin layer by layer.
DLP (Digital Light Processing): Uses digital micromirror technology to project a UV light source onto liquid resin, achieving layer-by-layer curing.
LCD (Liquid Crystal Display): Uses an LCD screen to selectively allow UV light to pass through, achieving exposure, and is also known as Mask SLA technology.
The primary material for these technologies is photosensitive resin, characterized by high forming accuracy and smooth surfaces, making it suitable for applications with high precision requirements.
In practical applications, photopolymerization technology is often combined with high-precision measurement methods to ensure the quality of the final product. Laser displacement sensors, as a type of non-contact measurement equipment, can avoid errors that might arise from traditional contact measurement methods, achieving micron-level or even higher measurement accuracy. This is particularly important for 3D printing processes like SLA (stereolithography) that require precise control of material layer height.
Project Requirements
Precise Position Monitoring:
Aimed at achieving precise positioning monitoring of the print platform or laser head/projector head in SLA/DLP 3D printers, ensuring each resin layer is accurately cured at the preset coordinates to maintain print precision and quality.Resin Level Management:
A system needs to be established for efficient monitoring of resin tank levels, preventing print interruptions due to resin depletion and ensuring continuous and efficient production.Precise Position Control Solution:
1. Deploy high-precision laser displacement sensors beneath the print platform or around the laser head/projector head to form an accurate position monitoring system.
2. During the printing process, the sensors continuously collect real-time position data of the platform and light source, providing instant feedback to the central control system.
3. The control system dynamically adjusts printing strategies and coordinates based on the feedback data, ensuring each resin layer is precisely positioned at the designated location, thereby enhancing print accuracy and stability.
Sensing Distance
|
Resolution
|
Linearity |
Output
|
30 mm (±4)
|
2 µm
|
±0.1%f.s. (f.s.=8mm) |
NPN / PNP
Analog RS485 |
50 mm (±10)
|
5 µm
|
±0.1%f.5. (f.s.=20mm) |
|
85 mm (±20)
|
10 µm
|
±0.1%f.8.(f.s.=40mm) | |
120 mm (±60) | 30 µm | ±0.1%f.s.(f.s.=120mm) | |
250 mm (±150) | 75 µm | ±0.3%f.s.(f.s.=300nm) |
Advantages of Using GFL-G Series High-precision Laser Displacement Sensors
✅ Real-time Distance Monitoring: Laser displacement sensors can monitor the distance between the laser head/projector head and the resin surface in real time, ensuring that the light is accurately focused on the resin layer, thereby avoiding issues like curing position shifts or light leakage.
✅ Enhanced Printing Precision: By providing precise position monitoring and control, laser displacement sensors can significantly improve printing accuracy. This helps reduce errors and defects during the printing process, thereby improving the dimensional accuracy and surface quality of the final product.
✅ Automated Adjustment Functionality: Laser displacement sensors can be integrated with the control system to enable automated adjustments. When a position deviation is detected, the control system can automatically adjust the position of the print platform or laser head/projector head to correct the deviation and continue printing, ensuring the continuity and accuracy of the printing process.
Intelligent Resin Level Monitoring Solution:
1. Utilize non-contact laser displacement sensors installed at the top or side of the resin tank, using laser ranging principles to monitor the resin surface position.
2. The sensors capture the displacement of reflected light caused by changes in resin levels in real time and use precise algorithms to calculate the current level, continuously updating the level data.
3. Seamlessly integrate the sensors into the 3D printer control system to enable instant transmission and processing of level data. When the level drops below the preset safety threshold, the system automatically triggers an alarm or pauses printing operations to ensure production safety and continuity.
Sensing Distance
|
Repeatability
|
Linearity |
Output
|
30 mm (±5)
|
10 µm
|
±0.1%F.S. |
Analog / RS485
|
50 mm (±15)
|
30 µm
|
NPN / Analog / RS485
|
|
100 mm (±35)
|
70 µm
|
||
200 mm (±80) | 200 µm | ±0.2%F.S. | |
400 mm (±200) | 400 µm / 800 µm |
Advantages of Using GFL-Z Series Laser Displacement Sensors
✅ Non-contact Measurement: Avoids direct contact with resin, reducing the risk of corrosion and contamination, lowering maintenance costs, and increasing system durability.
✅ Real-time Precision Monitoring: Provides continuous, high-precision data on levels and positions, ensuring real-time monitoring and precise control during the printing process.
✅ Intelligent Management: Seamlessly integrates with the control system, enabling automated warning and response mechanisms, optimizing the printing process, and improving production efficiency and safety.
Applications of Laser Displacement Sensors
Laser displacement sensors are versatile measurement tools capable of accurately measuring physical quantities such as length, distance, vibration, speed, and angle. Laser displacement sensors play a crucial role in applications such as small part identification, conveyor belt monitoring, material overlap detection, robotic position control, liquid level monitoring, thickness measurement, vibration analysis, collision testing, and various automotive tests.
DADISICK Popular Sensors
Output method: NPN/PNP+analog+RS485
Resolution: 1mm
Laser type: red semiconductor laser Class II laser 655+10nm<1m
Reaction time: 50-200ms
Measure distance: 0.1-50m
By converting from the laser into electrical signals. determine various characteristics,distance, displacement, or position.
Detection range: 100-2000 mm, 200-4000 mm, 350-6000 mm
Material: copper nickel plating, plastic fittings
Connection type: 5-pin M12 connector
Detection range: 150-3000 mm
Material: plastic accessories, filled with epoxy resin
Connection type: 5-pin M12 connector
Output method: analog voltage 0-10V+PNP