Auxiliary Equipment for Laser Pipe Cutting Machines in Cutting Spiral Welded Steel Pipes—Laser Displacement Sensors
- Share
- publisher
- Zoe
- Issue Time
- Aug 16,2024
Summary
DADISICK's GFL-Z Series laser displacement sensors utilize angle measurement principles, providing reliable and highly accurate measurements at close distances (up to 600 mm). Regardless of surface color, shape, roughness, or texture, the triangulation sensors deliver stable measurement values. In the process of cutting spiral welded steel pipes with laser pipe cutting machines, these sensors can serve as auxiliary equipment, ensuring efficiency, accuracy, and safety in the cutting process.
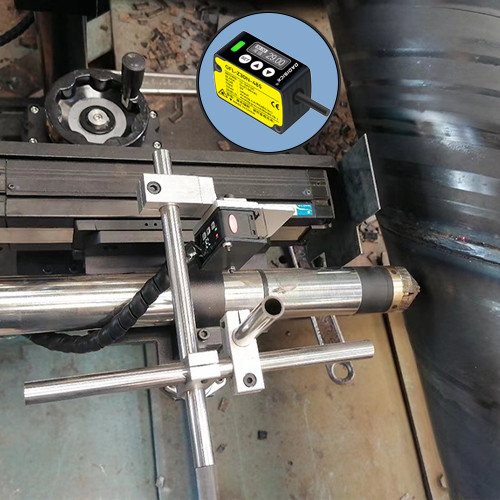
The Main Challenges Faced by Laser Pipe Cutting Machines When Cutting Spiral Welded Steel Pipes
Incomplete Cutting: This issue may arise from mismatches between the laser nozzle and the thickness of the processed pipe, setting the laser cutting speed too fast, contamination of laser lenses, or improper focal adjustment.
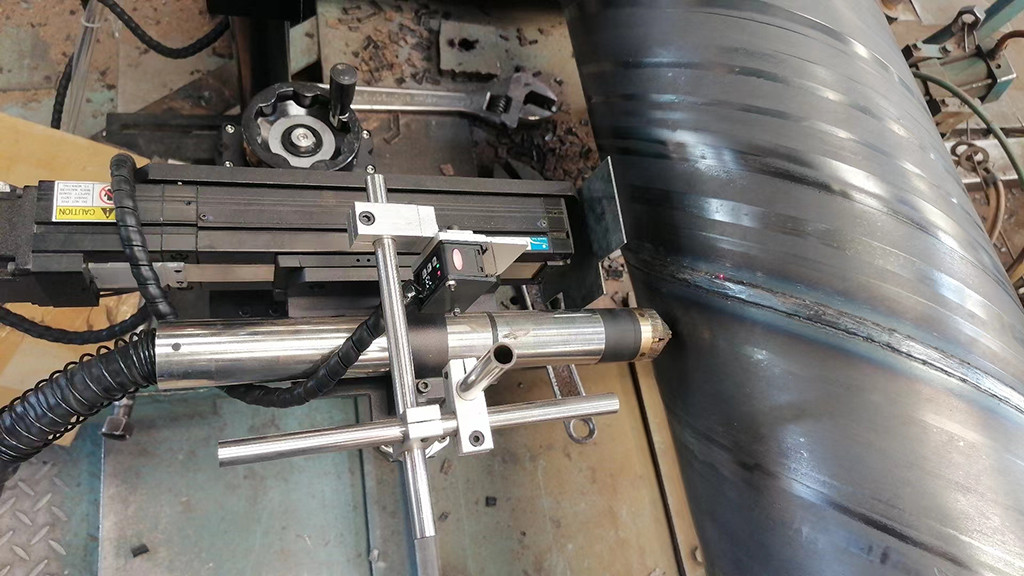
Enhancing Laser Pipe Cutting Efficiency: The Role of Laser Displacement Sensors in Spiral Welded Steel Pipe Processing
As the spiral welded steel pipe rotates and the cutting torch begins its work, the laser displacement sensor fixed on the cross arm plays a crucial role. Its specific functions include:
Accurate Distance Measurement and Dynamic Adjustment: By emitting a laser and receiving the signal reflected back from the surface of the steel pipe, the sensor can accurately calculate the distance between the laser head and the pipe surface. This data is essential for maintaining the optimal working gap between the cutting torch and the pipe, helping to achieve efficient and accurate cutting.
Smart Automatic Adjustment and Instant Feedback: If the pipe shifts position during rotation, the laser displacement sensor quickly detects the change and, through its integrated feedback system, instantly adjusts the cutting torch's position, ensuring continuity and consistency in cutting.
Safety Monitoring Mechanism: In addition to the above functions, the laser displacement sensor also has a safety monitoring function. If it detects an abnormal pipe position or an excessively close distance between the cutting torch and the pipe, the sensor will immediately trigger an alarm or automatically stop the cutting torch, effectively preventing safety accidents.
Increased Efficiency and Automation: Thanks to the precise measurement and quick response capabilities of the laser displacement sensor, the cutting torch can operate continuously and efficiently without frequent manual intervention, significantly improving production efficiency and the level of automation in cutting operations.
Recommended Laser Displacement Sensors
Sensing Distance
|
Repeatability
|
Linearity |
Output
|
30 mm (±5)
|
10 µm
|
±0.1%F.S. |
Analog / RS485
|
50 mm (±15)
|
30 µm
|
NPN / Analog / RS485
|
|
100 mm (±35)
|
70 µm
|
||
200 mm (±80) | 200 µm | ±0.2%F.S. | |
400 mm (±200) | 400 µm / 800 µm | ||
| |||
Laser displacement sensors are versatile measurement tools capable of accurately measuring physical quantities such as length, distance, vibration, speed, and angle. Laser displacement sensors play a crucial role in applications such as small part identification, conveyor belt monitoring, material overlap detection, robotic position control, liquid level monitoring, thickness measurement, vibration analysis, collision testing, and various automotive tests. |
DADISICK Popular Sensors
Response time: up to 1.0ms
Repetitive accuracy: up to 2µm
Output method: NPN/PNP+analog+RS485
Resolution: 1mm
Laser type: red semiconductor laser Class II laser 655+10nm<1m
Reaction time: 50-200ms
Measure distance: 0.1-50m
By converting from the laser into electrical signals. determine various characteristics,distance, displacement, or position.
Sensing range 20m, A technique that uses a laser beam to measure distance and create detailed maps of objects and environments.