Customized Safety Mat Solutions for the Plastic Film and Thermoforming Industry | Tailored Protection from Our Factory
- Share
- publisher
- Zoe
- Issue Time
- Jul 16,2024
Summary
The safety mat is a pressure-sensitive device that detects changes in pressure when a person or object stands on, steps on, or walks over it. This pressure change triggers a safety signal to stop machine operation or issue an alarm. As a safety device, the safety mat protects individuals from harm caused by hazardous machinery or equipment, making it an essential component of industrial safety systems.
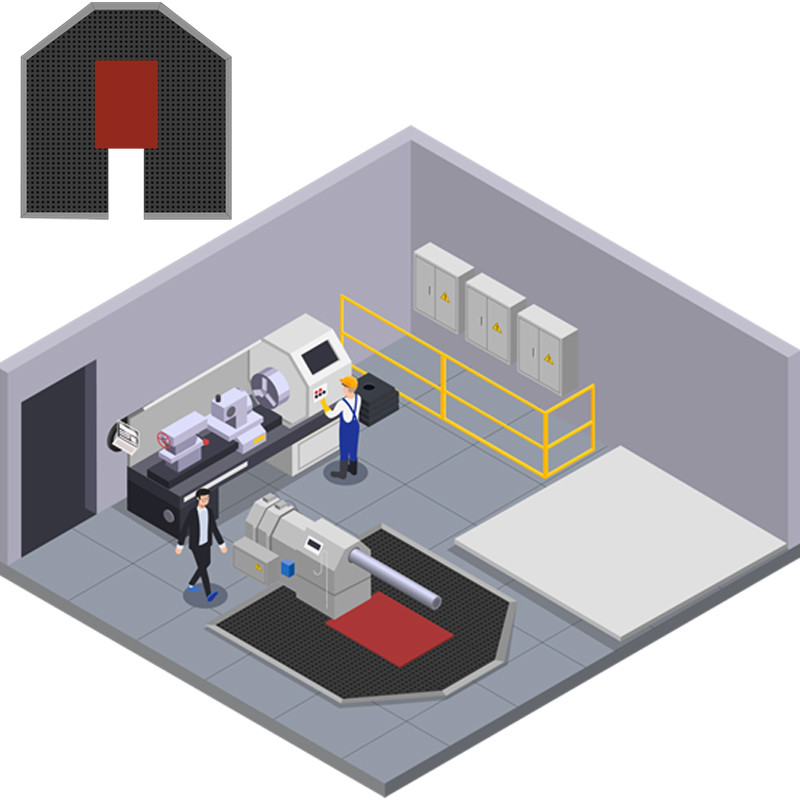
Background of Our Customers
About Company
Oben Group produces polypropylene, polyester, and nylon films for flexible packaging, coatings for the graphic industry, polypropylene thermoformed products, engineering resins, and polyester strapping.
As a leader in developing, manufacturing, and commercializing polypropylene, polyester, and polyamide films, Oben Group also produces polypropylene thermoformed products.
Today, Oben Group operates 14 manufacturing plants, 1 distribution center, and 8 commercial offices across 17 countries in the Americas and Europe.
Oben Group develops, produces, and markets plastic films for flexible packaging and complementary products, with a commitment to quality and efficiency.
About the Production Process of Plastic Films
The production process of flexible plastic films is a complex and meticulous craft involving multiple stages.
1. Selection and Preparation of Raw Materials
Types of Raw Materials: Common raw materials include polyethylene (PE), polypropylene (PP), and polyvinyl chloride (PVC), which are petrochemical products obtained through oil cracking and refining.
Form: Raw materials usually exist in the form of granules or powder, requiring further processing to produce films.
2. Melt Extrusion
Process Description: Raw materials are fed into the hopper of an extruder. The extruder melts the raw materials into a flowing plastic melt through heating and mechanical action. Temperature control during this process is crucial, as it directly affects the flowability of the melt and the quality of the film.
Equipment: The primary equipment used for melt extrusion is the extruder.
3. Film Formation
Formation Method: The molten plastic melt is extruded through the die of the extruder into film form. The design of the die determines the thickness and width of the film.
Process Key Points: To ensure the uniformity and flatness of the film, appropriate stretching and cooling are necessary during the forming process.
4. Cooling and Curing
Cooling Method: The formed film needs to be rapidly cooled using cooling devices to prevent the melt from re-solidifying.
Curing Effect: The cooling process also helps in curing the film, giving it sufficient strength and stability.
5. Surface Treatment
Purpose of Treatment: Depending on the intended use, the film's surface may need treatment to enhance characteristics such as gloss, anti-static properties, and printability.
Methods of Treatment: Common surface treatment methods include corona treatment and plasma treatment.
6. Winding and Packaging
Winding: After the above steps, the produced film is wound into rolls by a winding device.
Packaging: The wound film is appropriately packaged to prevent damage during transport and storage.
7. Quality Inspection
Inspection Content: The produced plastic film undergoes strict quality inspection to ensure that its thickness, width, strength, temperature resistance, and other indicators meet standard requirements.
Importance: Only films that pass inspection can proceed to the next production stage or be sold directly to the market.
8. Special Processes (such as Lamination and Printing)
For flexible plastic films, special processes like lamination and printing may also be required:
Lamination: Different materials are laminated together using adhesives or other methods to create composite films with special properties. For example, a printed film may be laminated with a heat-sealable inner film to create materials with special heat-adhesive functions.
Printing: Color printing is performed on the film to attract consumers' attention and enhance the product's quality. Gravure printing is the primary method used for plastic film printing, known for its speed, rich colors, and clarity.
The Customization Process of Safety Mats
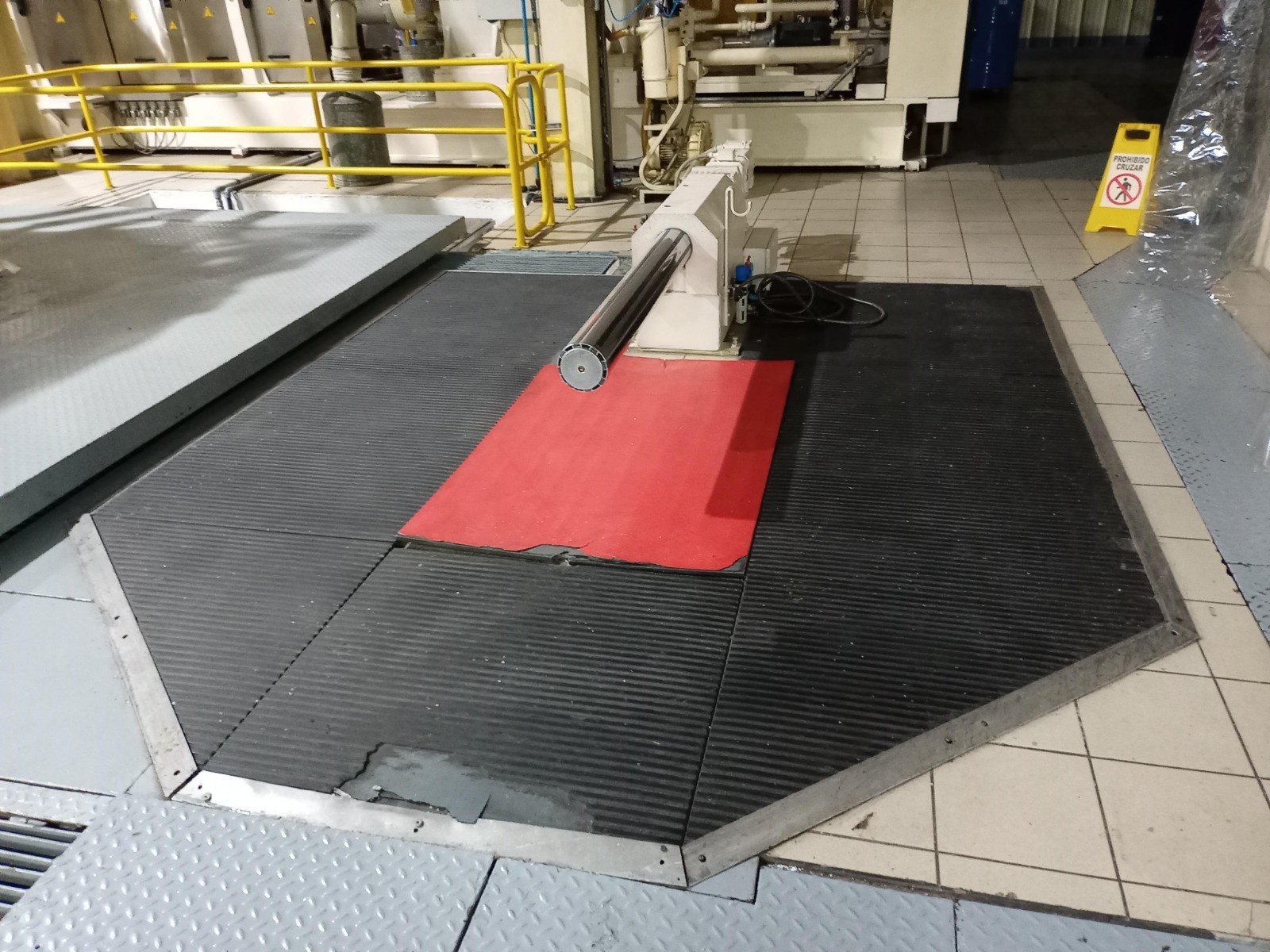
Requirements:
During the production process, the extruder plays a crucial role, but its operation also entails certain hazards, including but not limited to high-temperature risks, high-pressure risks, electrical shock risks, and mechanical injuries.
The image on the right is provided by oben Group, showing their production machinery (specifically the extruder) in conjunction with a safety mat. It is evident that parts of the mat's surface have worn away. Therefore, they sought a more cost-effective safety mat to replace the old one. After comparing different manufacturers, oben Group ultimately chose DADISICK to complete this custom service.
Design and Customization
Based on the detailed dimensions and shape requirements provided by the customer, our design team uses advanced CAD software for precise modeling to ensure that every inch of the safety mat meets customer expectations.
We select high-performance, wear-resistant materials and incorporate advanced anti-slip treatment technologies to create a durable and safe mat product.
To meet the customer's anti-static needs, we specifically use conductive fiber materials to ensure that the mat effectively eliminates static accumulation during use.
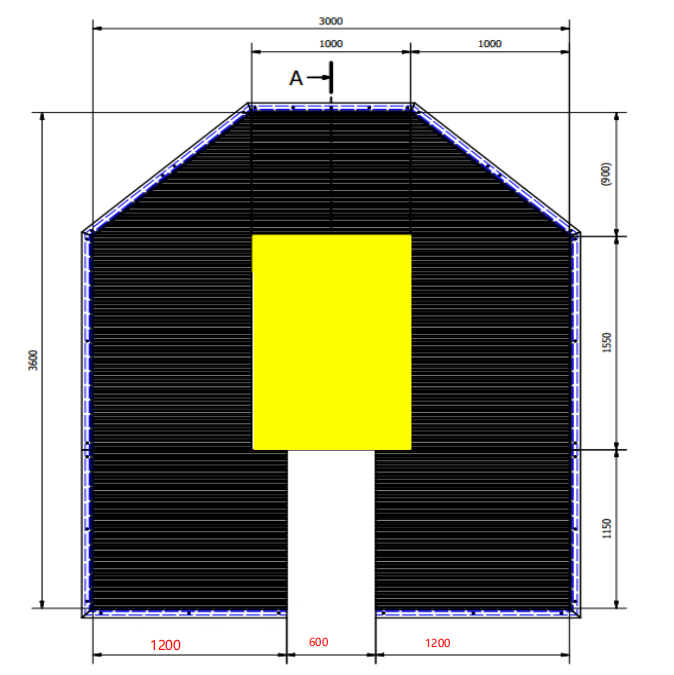
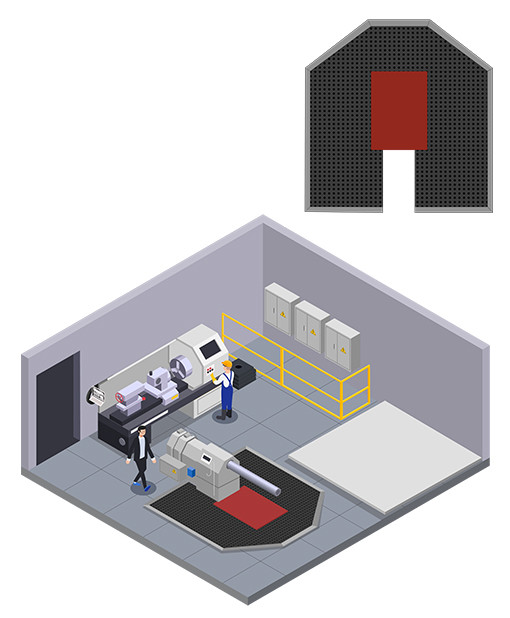
System Integration
We custom develop specialized interface modules to enable the safety mats to easily integrate with the customer’s control system, facilitating quick signal transmission and processing.
Our solution supports multiple communication protocols to ensure compatibility with different brands of equipment, reducing the complexity of system integration.
Customization Function Implementation
We introduce zoned detection technology, dividing the safety mat into multiple independent areas, each of which can independently set alarm conditions and sensitivity to meet the safety management needs of different zones.
We provide a flexible configuration interface that allows customers to adjust alarm parameters, sensitivity, and other settings according to actual needs, achieving personalized management.
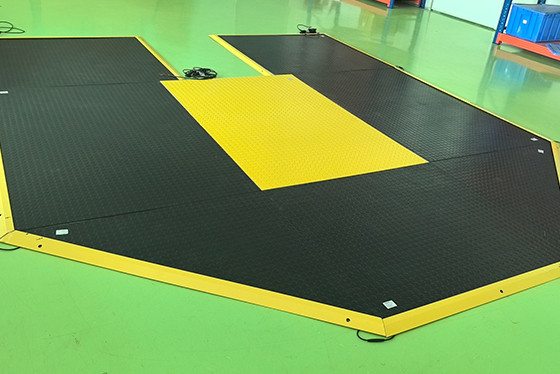
Installation and Commissioning
During the installation process, our staff strictly adhere to safety standards and operating procedures to ensure the mats are securely installed and properly wired.
After installation, comprehensive system testing and commissioning are conducted to ensure the safety mats function correctly.
Training and After-Sales Service
DADISICK provides customers with detailed operation manuals and video tutorials to ensure they can proficiently use the safety mats.
We have established a dedicated after-sales hotline and technical support team to promptly address any questions or issues customers encounter during use.
We offer regular follow-up visits and maintenance services to ensure the long-term stable operation of the safety mat system.
Recommended Safety Mats
Specifications
Surface Material:NBR rubberEdge Material:Aluminum
Height:14 mm
Protection Rating (IEC 60529): IP65
Anti-Slip (DIN 51130): R9
Trigger Force: 30 kg
Maximum Load Capacity (8 hours): 400 N/cm²
Fire Resistance Rating (DIN 4102): B2
Related Pressure-sensitive Devices
Safety carpet is a technology that monitors the pressure distribution on the carpet through pressure sensing.
Safety carpet is a technology that monitors the pressure distribution on the carpet through pressure sensing.
Safety carpet is a technology that monitors the pressure distribution on the carpet through pressure sensing.
Safety Edges is a technology that monitors the pressure distribution on the carpet through pressure sensing.