FAQ About Laser Distance Sensors and Laser Displacement Sensors
- Share
- publisher
- Zoe
- Issue Time
- Sep 5,2024
Summary
This article compiles frequently asked questions about laser displacement sensors and laser distance sensors.
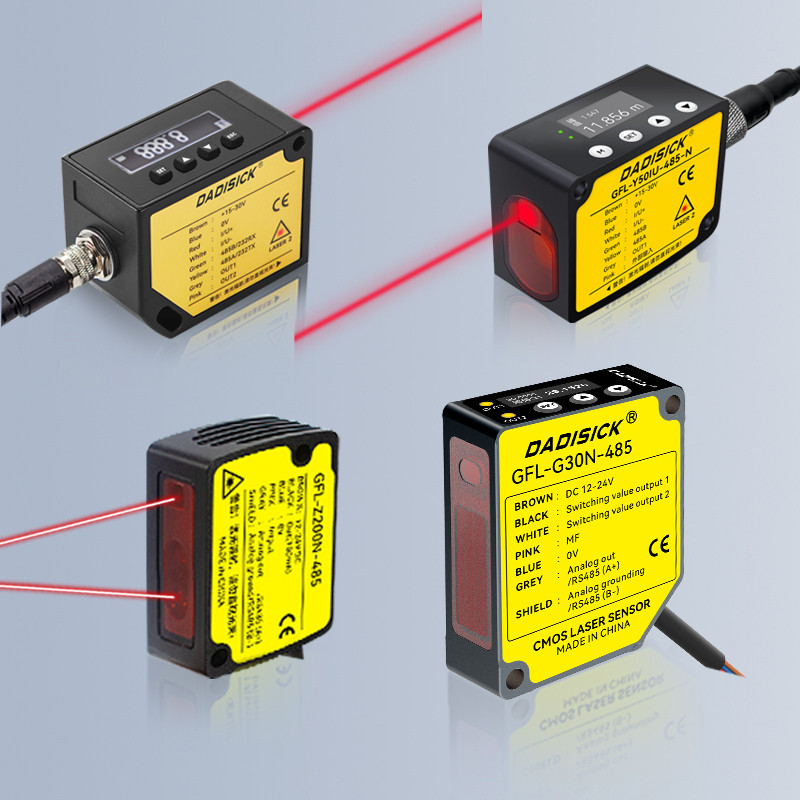
FAQ on Laser Displacement and Laser Distance Sensors in Industrial Automation
What Is A Laser?
A laser (Light Amplification by Stimulated Emission of Radiation) is a beam of light generated through stimulated emission, which has a specific wavelength. This characteristic allows the light beam to be highly concentrated, resulting in a single-wavelength (monochromatic) light.
What Are The Laser Classifications And Their Protective Measures?
Class 1: Does not cause harm to the eyes, and no protective measures are required.
Class 2: Due to the blink reflex, it is safe for short-term eye exposure, but warning signs are required.
Class 2M: Safe for short-term exposure due to the blink reflex, but it cannot be observed through optical instruments (e.g., magnifying glasses).
Class 3R: Direct viewing of the laser may be dangerous, so appropriate protective measures are necessary, and wearing protective eyewear is recommended.
Class 3B: Direct exposure to Class 3B lasers can cause harm to the eyes. Protective eyewear is usually required, and Class 3B lasers must be equipped with a key switch and safety interlock system.
Class 4: Class 4 lasers are the highest and most dangerous, including all lasers exceeding the AEL (Accessible Emission Limit) of Class 3B. Class 4 lasers can burn the skin or cause severe and permanent eye damage from direct, diffuse, or indirect exposure to the beam. Therefore, great care must be taken to control the beam path. Class 4 lasers must be equipped with a key switch and safety interlock system. Most industrial, scientific, military, and medical lasers fall into this category.
How Does A Laser Displacement Sensor Work?
A laser displacement sensor operates based on the triangulation principle, making it suitable for high-precision measurements at very short distances. The measurement range is typically within 1000 millimeters, with an accuracy that can reach the micron level, and it offers extremely fast measurement speeds. It is widely used in precision manufacturing, automation equipment, and the microelectronics field.
How Does A Laser Distance Sensor Work?
A laser distance sensor operates based on either the phase-shift method or the time-of-flight (ToF) method.
Phase-shift method: Suitable for mid to short-range measurements, with a typical measurement range from several centimeters to several meters and accuracy reaching the millimeter level.
Time-of-flight (ToF) method: Ideal for long-range and large-scale measurements, with a measurement distance ranging from several hundred meters to several kilometers, and accuracy typically between centimeters and decimeters.
Do Laser Displacement Sensors And Laser Distance Sensors Have Blind Spots?
Laser displacement sensors that use the triangulation principle do have blind spots. Therefore, a switch point should be set at the start of the working range to ensure reliable object detection. However, laser distance sensors based on the phase-shift or time-of-flight (ToF) method do not have blind spots.
How Accurate Are Laser Displacement Sensors?
The measurement accuracy typically depends on the measurement principle employed. If the measured values have high accuracy and precision, extremely high measurement accuracy can be achieved. For example, sensors using the triangulation principle can achieve a linear deviation of less than 1 millimeter.
What Is Linearity? How Is It Related To Measurement Accuracy?
Measurement accuracy consists of both accuracy and precision. To improve measurement accuracy, it's essential to focus on parameters such as linear deviation, temperature drift, switch-on deviation, and switching distance deviation.
What Is The Difference Between Repeatability And Linearity?
Maximum repeatability, or maximum repeat precision, refers to the largest potential deviation in the switching point or measurement value across the entire working range when measuring under the same conditions. Linearity, on the other hand, describes the maximum possible deviation between the actual measured value and the ideal measured value.
What Is Laser Triangulation?
Laser triangulation is a geometric measurement method. The sensor accurately determines the distance between the object and the sensor using the geometric relationship of a triangle.
What Is A CMOS Line?
A CMOS line is a type of photosensitive element. When light reflected from an object hits the CMOS line, the position of the light spot changes with the distance to the object. A CMOS line enables precise measurement of objects at short distances.
How Fast Is The Measurement Data Transmitted From The Sensor To The Control System? What Is The Sensor's Response Speed?
The sensor's speed depends on the data output method.
With digital switching output: the switching frequency determines the maximum number of switching cycles per second.
Analog output: the measurement speed determines the number of measurements output per second.
Using the IO-Link interface: the minimum cycle time dictates how fast new measurement values are transmitted through the interface.
What Is The Measurement Range Of Laser Displacement And Laser Distance Sensors?
Laser triangulation sensors can provide precise measurements at short distances, typically within 1 meter. Laser rangefinders using the time-of-flight method with a reflector can measure distances up to 100 meters.
Can Laser Displacement Sensors Measure Shiny Or Colored Surfaces? Do Different Surfaces Affect The Measurement Results?
Yes, laser distance sensors can reliably measure surfaces that are dark, colored, light, or have low reflectivity. The measurement results remain consistent across different surfaces.
What Is The Protection Rating Of Laser Displacement And Laser Distance Sensors?
Laser displacement and distance sensors typically have an IP67/68 protection rating, making them waterproof and suitable for industrial environments. Some laser distance sensors have an IP69K rating, which allows them to withstand high-pressure cleaning and corrosion, making them ideal for harsh cleaning applications and heavy-duty use.
How Can The Optical Components Of Laser Displacement Sensors Be Protected?
Laser displacement sensors from DADISICK are equipped with an aluminum alloy or metal die-cast housing, which effectively protects the optical components.
Related Laser Sensors for Distance Measurement
Displacement Sensor Based on the Triangulation Principle
Measurement Range: 24 mm to 400 mm
Accuracy: Minimum 0.002 mm, Maximum 0.075 mm
Protection Rating: IP64
Supported Interfaces: RS485 / Switch Output / Analog Current and Voltage
Measurement Range: 25 mm to 600 mm
Accuracy: Minimum 0.01 mm, Maximum 0.8 mm
Protection Rating: IP60
Supported Interfaces: RS485 / Switch Output / Analog Current and Voltage
Distance Sensor Based on the Phase Measurement Principle
Measurement Range: 0.1 m to 50 m
Resolution: 1 mm
Protection Rating: IP67
Supported Interfaces: RS485 / Switch Output / Analog Current and Voltage
Measurement Range: 0.2 m to 100 m
Resolution: 1 mm
Protection Rating: IP67
Supported Interfaces: RS232 / RS485 / Switch Output / Analog Current and Voltage