High-Speed, Interference-Free, Precise Synchronization — ST100 Optical Transmission Module Empowers the Automated Crane Industry
- Share
- publisher
- Zoe
- Issue Time
- Feb 26,2025
Summary
The ST100 series optical data transmission module, with its high speed, low latency, and strong anti-interference capabilities, offers a novel solution for achieving synchronization control and collision prevention in bridge crane operations. Through proper system integration, parameter configuration, and on-site testing, the module can significantly enhance the intelligence and safety of crane operations, providing robust support for modern industrial automation and logistics.
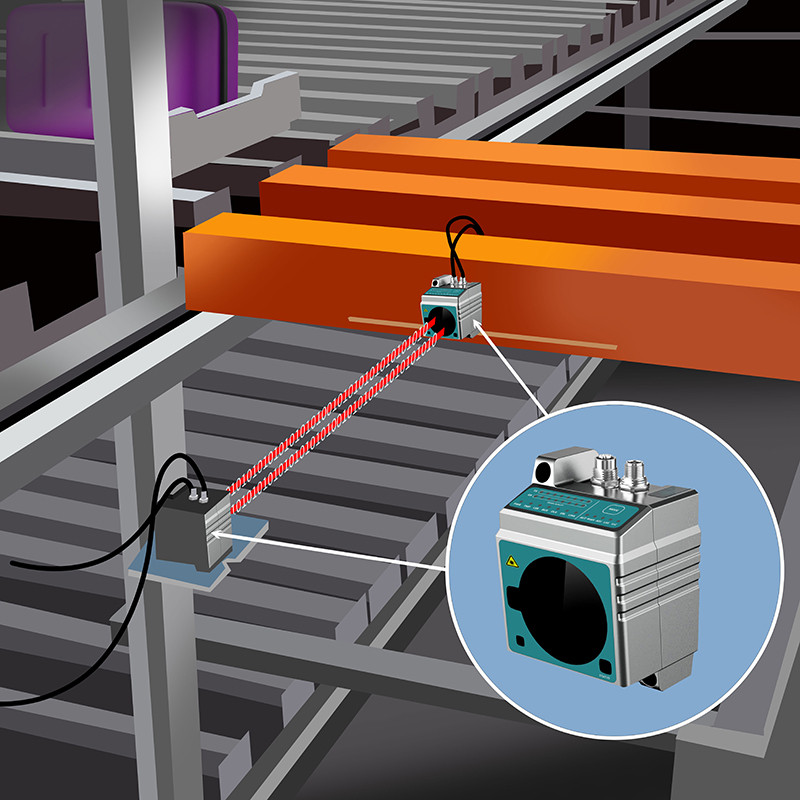
Solution for Applying the ST100 Series Optical Data Transmission Module in Bridge Cranes
Bridge cranes play a crucial role in industrial production and warehousing, where precise synchronization and safety protection are essential during the lifting and transportation of heavy loads. In complex environments where traditional wired data transmission is limited by installation challenges, a high-speed, low-latency, and interference-free data transmission method is needed. The ST100 series optical data transmission module is specifically designed for such scenarios. It employs infrared lasers to achieve full-duplex 100 Mbps communication over selectable distances (80m, 120m, or 200m), meeting the demands for real-time data exchange, synchronization control, and anti-collision management in crane operations.
ST100 Series Optical Data Transmission Module
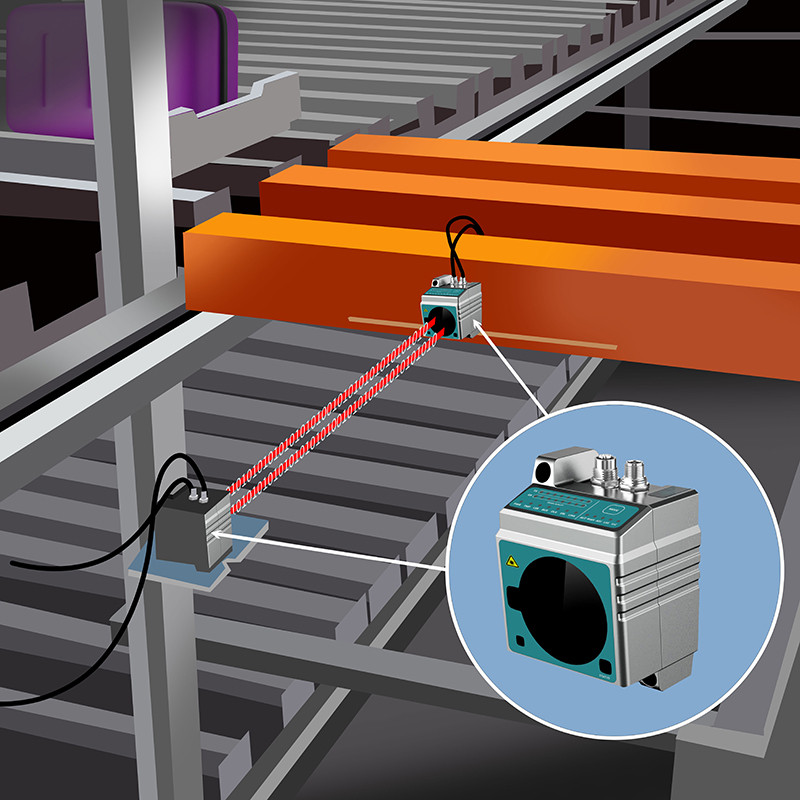
Product Advantages and Key Features
▪️High-Speed Full-Duplex Transmission:
Achieves 100 Mbps data transmission and supports selectable distances up to 200 meters, ensuring real-time data exchange.
▪️Laser Communication Advantages:
Utilizes infrared lasers at wavelengths of 785nm and 850nm for data transmission. With a primary beam spot of approximately 5mm and a divergence angle of 1°, paired with a receiver field-of-view of 1.5°, it offers minimal channel interference and extremely low transmission delay.
▪️Flexible System Design:
The module integrates optical, mechanical, electronic, and software components, supporting space laser communication for any protocol within 200 meters. It also features extensive interaction and indicator functions for quick installation, making it ideal for scenarios where cable laying is impractical or high real-time performance is required.
Overview of Working Principles
▪️Data Conversion and Transmission:
The data stream from the host computer is converted into laser pulse signals by the module's circuitry and then transmitted as a series of laser pulses through free space to the receiver.
▪️Optoelectronic Conversion:
At the receiving end, the sensor detects the incoming laser pulses and converts the optical signals back into electrical data streams, which are then sent to the host computer to complete the two-way data transmission.
▪️Optimized Link Parameters:
By precisely matching the optical beam characteristics (spot size, divergence angle, and field-of-view), the module ensures stable and reliable data transmission even in high-interference or complex environments typical of bridge crane operations.
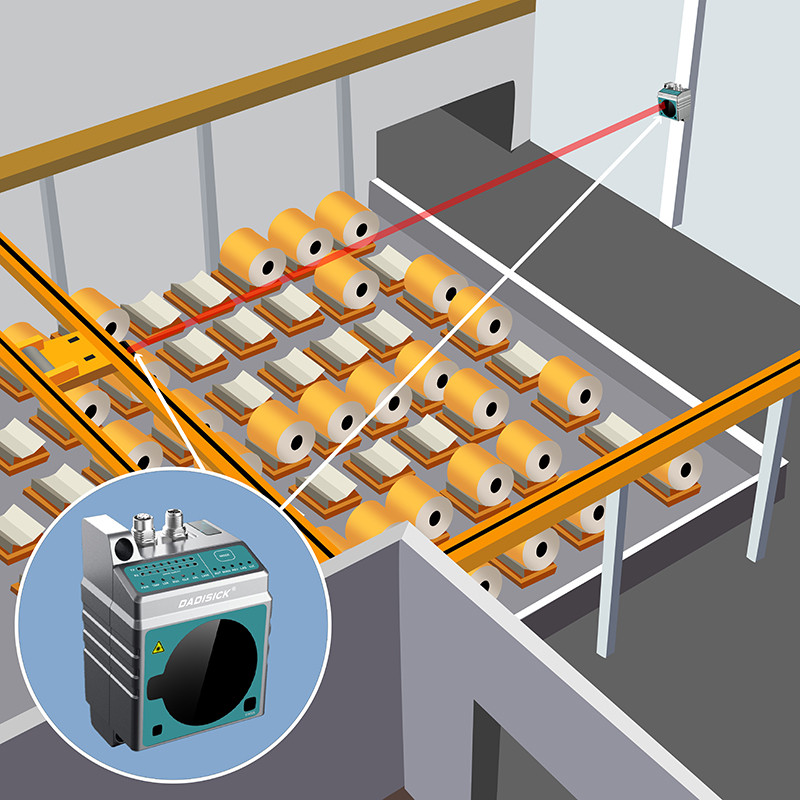
Bridge Crane Application Design
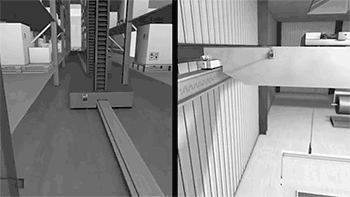
Synchronization Control
Application Scenario:
In operations where multiple cranes or multi-girder systems need to move synchronously, accurate relative positioning is critical to prevent load imbalance and potential collisions. Any deviation in the movement of a single unit can disrupt the overall balance and lead to unsafe conditions.
Solution Approach:
▪️Real-Time Data Exchange:
The installation of the ST100 module enables high-speed data transmission between cranes, allowing each unit to obtain real-time information on position, movement status, and speed.
▪️Coordinated Movement Control:
The real-time data is processed by the host computer, which executes precise synchronization algorithms to ensure that all cranes or bridge girders move in perfect harmony along the same track, thereby mitigating safety risks caused by individual unit discrepancies.
Anti-Collision Functionality
Application Scenario:
Bridge cranes may encounter other cranes, obstacles, or walls within their operating area. It is essential to ensure that as a crane approaches an obstacle, it can automatically decelerate or stop to prevent a collision.
Solution Approach:
▪️Continuous Distance Measurement:
The ST100 module continuously transmits and receives laser signals, calculating the distance between the crane and nearby obstacles in real time.
▪️Adaptive Speed Control:
Based on the measured distance, the system maintains normal operating speed when the obstacle is far away. As the crane enters a critical range (e.g., the last 10 meters at normal speed, followed by a gradual reduction in the final 5 meters to half speed), the speed is adjusted smoothly until the crane comes to a complete stop, ensuring safe deceleration and smooth stopping.
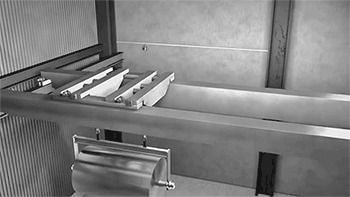
System Integration and Installation
▪️Optimal Installation Position:
The module should be installed in a location with an unobstructed line of sight to ensure that the optical beam can directly reach the target. Installation positions must be carefully planned according to the crane’s structural design to maintain stable data transmission.
▪️Parameter Configuration and Testing:
Parameters such as transmission speed, beam angle, and anti-collision distance thresholds can be configured via the host computer. On-site testing is necessary to verify data transmission accuracy and responsiveness, followed by fine-tuning as needed.
▪️Environmental Adaptability:
Given the harsh operating conditions (high temperature, vibration, dust) in crane environments, the module should include protective measures (such as shields and vibration damping devices) to ensure long-term stable operation.
Expected Outcomes and Overall Advantages
✅Real-time, reliable data exchange supports synchronized crane operations with accurate and up-to-date information.
✅With real-time positioning and adaptive speed control, the risk of collisions is minimized, ensuring both equipment and personnel safety while improving overall operational efficiency.
✅The module’s plug-and-play design facilitates rapid installation and integration, reducing setup time and maintenance costs.
Related Sensors
Eective transmission distance: 80 m
Communication rate: 100 Mbit/s
Communication light divergence angle: 1°
Communication light receiving angle: 1.5°
Eective transmission distance: 120 m
Communication rate: 100 Mbit/s
Communication light divergence angle: 1°
Communication light receiving angle: 1.5°
Eective transmission distance: 200 m
Communication rate: 100 Mbit/s
Communication light divergence angle: 1°
Communication light receiving angle: 1.5°
Measuring frequency: 1000Hz
Data transmission interface: SSl, Ethernet 100 BASE-TX
Measuring distance: 200m
Measurement accuracy: ±2 mm