Key Applications of Laser Distance Sensors in Robotic Arm Assembly
- Share
- publisher
- Zoe
- Issue Time
- Sep 9,2024
Summary
The application of laser distance sensors in precise robotic arm assembly uses TOF technology to monitor material positions in real-time, ensuring assembly accuracy. The sensors are installed at an angle above the material placement area and use pulsed and phase-shift methods for long and short-distance measurements. Combined with the control system, this optimizes the robotic arm's movement trajectory, enhancing production efficiency and quality.
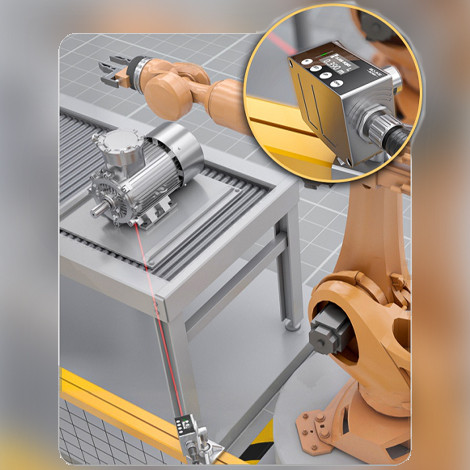
Key Applications of Laser Distance Sensors in Robotic Arm Assembly
With the rapid development of industrial automation technology, robotic arms have become core equipment in modern manufacturing, widely used in automated production lines, robotics technology, vehicle monitoring, and autonomous driving in intelligent transportation systems. In addition, industries such as medical devices, construction, and engineering are also gradually adopting robotic arms to improve efficiency and quality.
The advantage of robotic arms lies in their ability to complete various spatial tasks with precision, becoming an important tool for enhancing production efficiency and quality. Typically, robotic arms consist of a base, multiple joints, drive units, end-effectors, moving components, and guidance systems, working together to perform complex tasks.
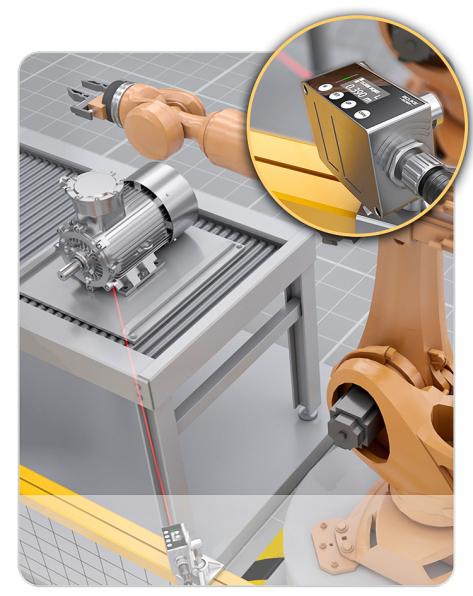
Challenges:
In the precision assembly operations of robotic arms, ensuring the accurate positioning of materials is critical. Even minor deviations may lead to component damage or machine malfunction, thus affecting the efficiency and stability of the entire production line. Therefore, achieving precise identification and tracking of material positions has become a key challenge in the application of robotic arms.
Solution:
Laser distance sensors can effectively solve this problem. Based on DADISICK's Time-of-Flight (ToF) laser distance sensors, the sensors are installed at an angle above the surrounding area of the material placement zone. The sensors project their laser beams at an angle onto the surface of the material. This allows the sensor to accurately detect the position of objects with different colors in real-time without interfering with the operation of the robotic arm, ensuring a smooth assembly process.
Working Principle of Laser Distance Sensors
The working principle of the ToF laser distance sensor is based on the time-of-flight measurement technology. The sensor emits a laser beam and detects the return echo. It uses a high-precision timer to measure the time difference between when the laser is emitted and when it is reflected back from the target object. Given that the speed of light is constant, multiplying the time difference by the speed of light gives the distance to the target object.
ToF laser distance measurement can be further divided into two specific techniques: the pulsed method and the phase-shift method.
Pulsed Method:
The laser emitter sends out a laser pulse, which is reflected back after hitting an object. By measuring the time interval between the emission and reception of the laser pulse and multiplying it by the speed of light, the distance to the target can be calculated. The pulsed method is suitable for long-range and large-area measurements.
Phase-shift Method:
The emitter sends out continuous modulated waves. By calculating the phase difference between the transmitted wave and the received wave, the distance can be measured accurately. The phase-shift method is more suitable for medium to short-range measurements, typically used for distances ranging from several centimeters to several meters.
Benefits of Using the GFL-Y Series Laser Distance Sensor
During the robotic arm assembly process, laser distance sensors work in conjunction with the control system, creating an efficient positioning and tracking system. The sensors collect real-time material position information and transmit the data to the controller. The controller adjusts the movement trajectory and posture of the robotic arm based on pre-programmed algorithms, ensuring that the end-effector can accurately assemble components in the designated positions.
Related Laser Distance Sensor
✅ Measurement Range: 0.1 m to 50 m ✅ Resolution: 1 mm ✅ Supported Interfaces: RS485 / Switch Output / Analog Current and Voltage ✅ Protection Rating: IP67 ✅ Operating Temperature: -10℃~+45℃ ✅ Cable: With 8-core Composite 2 m Cable | ||
NPN+analog+485
|
PNP+analog+485
|
Operating Range
|
GFL-Y01IU-485-N
|
GFL-Y01IU-485-P
|
0.1 - 1 m
|
GFL-Y02IU-485-N
|
GFL-Y02IU-485-P
|
0.1 - 2 m
|
GFL-Y05IU-485-N
|
GFL-Y05IU-485-P
|
0.1 - 5 m
|
GFL-Y10IU-485-N
|
GFL-Y10IU-485-P
|
0.1 - 10 m
|
GFL-Y20IU-485-N | GFL-Y20IU-485-P | 0.1 - 20 m |
GFL-Y50IU-485-N | GFL-Y50IU-485-P | 0.1 - 50 m |