Laser Scanning Radar Sensor Technology: Unlocking New Possibilities for AGVs, Factory Safety, and Robotics
- Share
- Issue Time
- Apr 23,2024
Summary
This article introduces Laser Scanning Radar Sensor's principles, technical features, and its AGV applications like precise positioning, path planning, and obstacle avoidance. This article highlights lidar's role in enhancing safety in factory operations and reducing accidents. It also discusses lidar's application in robotics for autonomous navigation and environmental perception.
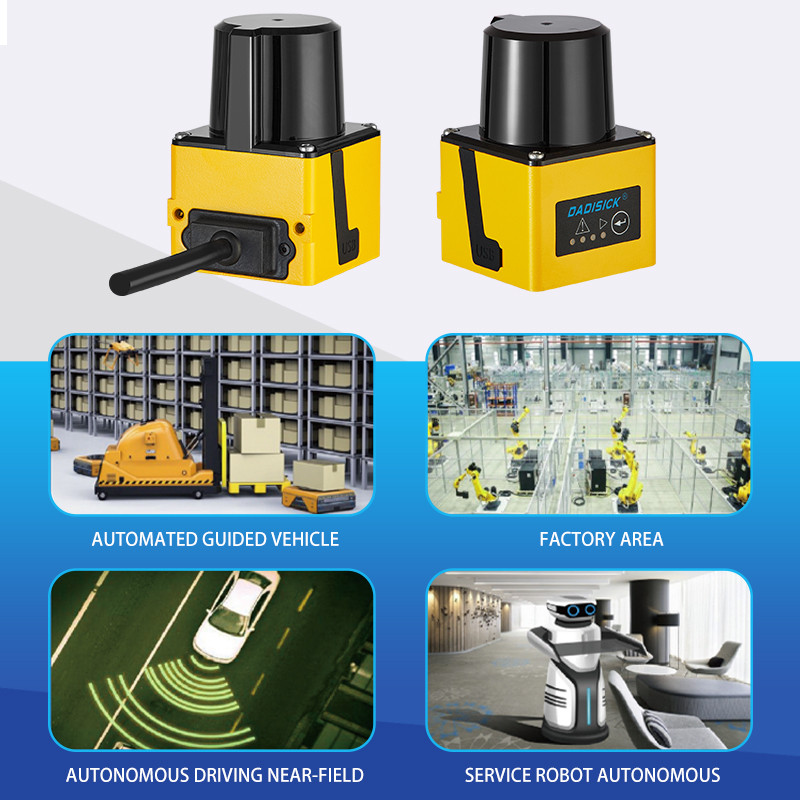
Principle of Laser Scanning Radar Sensor (LiDAR) Operation
Technical Characteristics of Laser Scanning Radar Sensor (LiDAR)
Application of Laser Scanning Radar Sensor (LiDAR) in AGVs, Factory Area Operational Safety Protection, and the Robotics Industry
1. Safety laser scanners have advantages in terms of installation location compared to light curtains. Aligning the optical axis during installation is also very easy. Even complex protection zones can be easily configured using intuitive software.
2. Compared to safety mats, safety laser scanners do not pose the risk of damage due to falling workpieces. Protection zones with safety laser scanners can be freely configured, making layout changes easy to implement. When changing layouts, there is no need to stock different sizes and shapes of safety mats to create different protection zone shapes.
3.Compared to other safety devices, safety laser scanners have fewer restrictions on installation location and protection areas. They are easy to install, with minimal risk of failure, making them effective safety devices for providing protection.
Advantages of 2D Radar Compared to 3D Radar
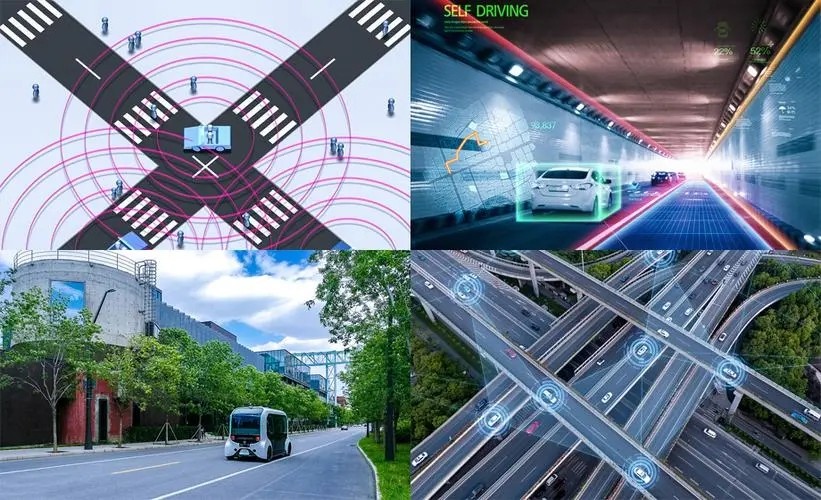