Measuring the Thickness of Lithium Battery Electrodes Using High-Precision Laser Displacement Sensors
- Share
- publisher
- Zoe
- Issue Time
- Jul 19,2024
Summary
The GFL-G Series and GFL-Z Series high-precision laser distance displacement sensors introduced by DADISICK have a resolution that can reach up to the micron level, with the highest resolution being 2 μm. They are suitable for measuring displacement, flatness, height, and thickness.
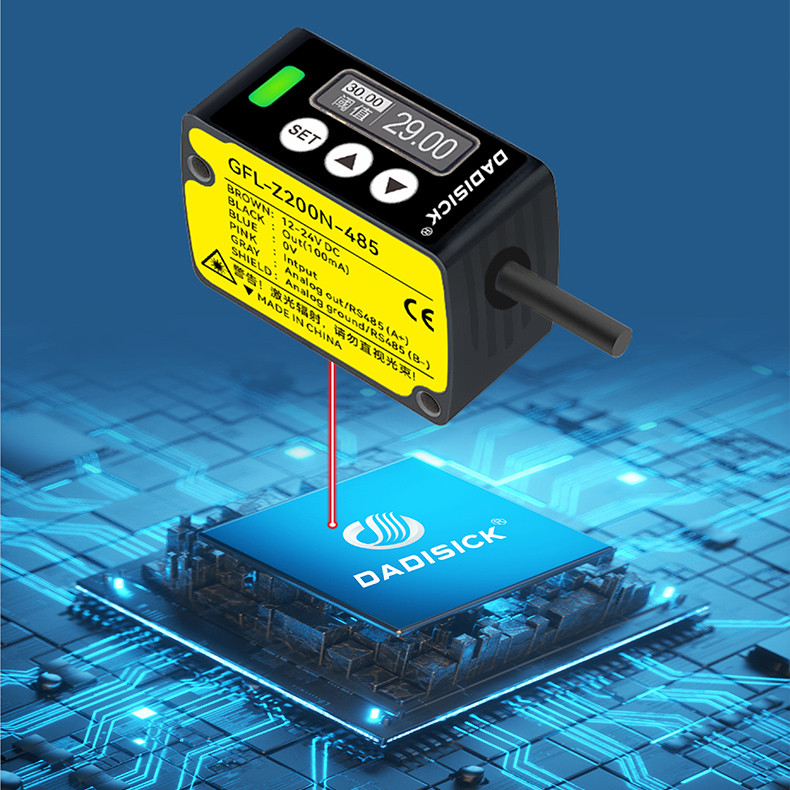
High-Precision Laser Displacement Sensors for Accurate Thickness Measurement of Lithium Battery Electrodes
As the electric vehicle market continues to expand, the demand for lithium batteries is increasing. In the production process of lithium batteries, the thickness of the electrodes is a crucial factor affecting battery performance and safety. Therefore, precise thickness measurement of lithium battery electrodes is a key aspect of the production process. In recent years, laser displacement sensors, as high-precision measuring devices, have been widely used in the thickness measurement of lithium battery electrodes. This paper will introduce the working principle, application scenarios, measurement methods, experimental results, and application prospects of laser displacement sensors in the thickness measurement of lithium battery electrodes.
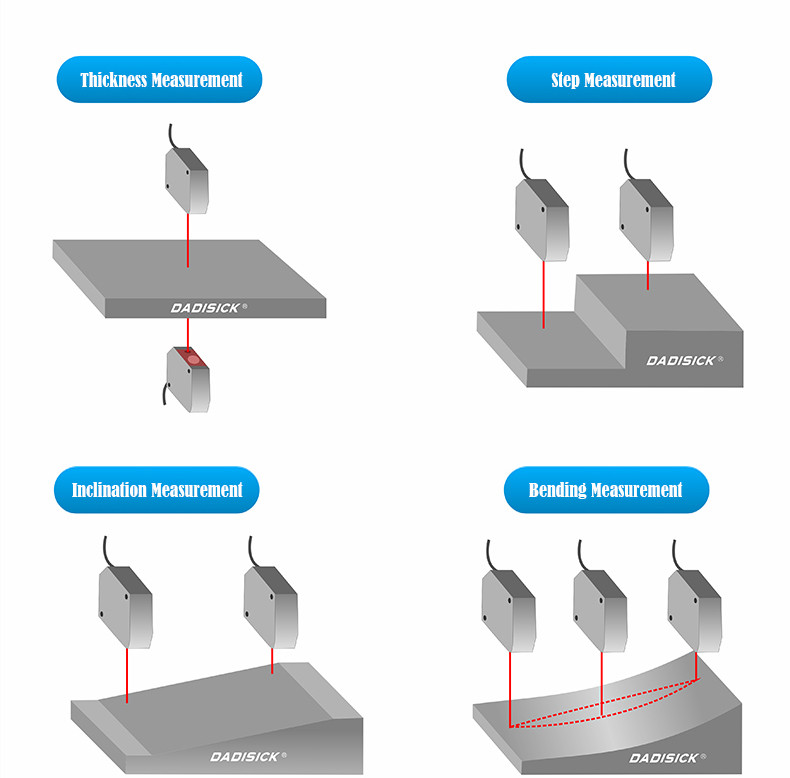
Principle of Operation for Laser Displacement Sensor
1. Laser Emission: The laser displacement sensor emits a laser beam directed at the object being measured.
2. Beam Reflection: The beam reflects off the surface of the object.
3. Beam Reception: The sensor's light-sensitive receiver captures the reflected beam, usually at a fixed angle.
4. Triangulation Method: The method is based on the principle of geometric triangulation. A laser beam is emitted by a laser source and directed towards the surface of the object being measured through a lens. The laser light reflected off the object's surface is captured by a receiver through another lens. The position of the reflected light spot on the receiver changes according to the displacement of the object. By analyzing these changes in position, the sensor calculates the displacement using geometric triangulation.
This method is well-suited for high-precision, short-distance measurements, as it can detect even minute changes in the position of the reflected light spot, enabling measurements with micrometer-level accuracy. (To learn about the differences between laser distance sensors and laser displacement sensors, please click here.)
In the thickness measurement of lithium battery electrodes, laser displacement sensors can achieve high-precision thickness measurement and also detect the surface profile of the electrodes, providing strong support for quality control in the production process.
Method of Measurement for Laser Displacement Sensors
In the thickness measurement of lithium battery electrodes, the specific measurement method of the laser displacement sensor is as follows:
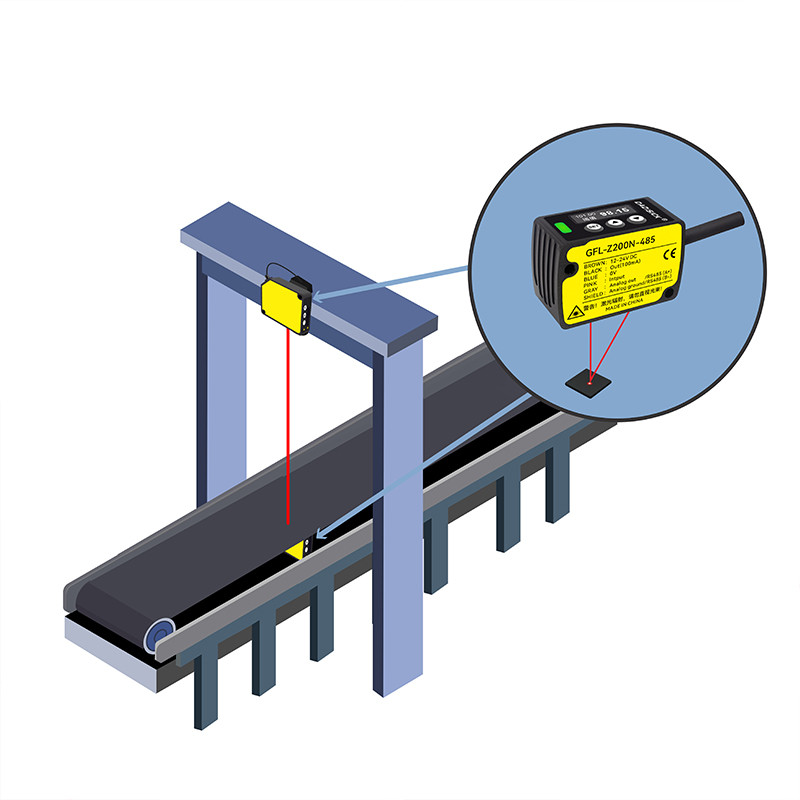
Thickness Measurement:
First, fix the laser displacement sensor on the test bench and adjust the distance between the sensor and the measured electrode to ensure that the laser beam can correctly hit the surface of the electrode. Then, operate the control system to scan the electrode with the laser displacement sensor and record the displacement data of each point. By processing and analyzing the displacement data, the thickness distribution of the electrode can be determined.Accuracy Calibration:
To ensure measurement accuracy, the laser displacement sensor needs to be periodically calibrated. Generally, standard reference blocks can be used for calibration. Place the standard reference block on the test bench and adjust the position relationship between the laser displacement sensor and the reference block so that the laser beam can vertically hit the surface of the reference block. Then, operate the control system to scan the reference block with the laser displacement sensor and record the displacement data. By analyzing and processing these data, the accuracy error of the sensor can be determined and corresponding adjustments and compensations can be made.Stability Check:
To ensure the reliability of measurement results, the stability of the laser displacement sensor needs to be periodically checked. Generally, long-term monitoring can be used for stability checks. Place the laser displacement sensor on the test bench to scan a fixed measured object and record the measurement data over a period. By analyzing and processing these data, the stability error of the sensor can be determined and corresponding adjustments and compensations can be made.Advantages of Using Laser Displacement Sensors for Measurement
Through experimental results and analysis, we found that laser displacement sensors have the following advantages in the thickness measurement of lithium battery electrodes:
High Precision: The accuracy of laser displacement sensors can reach the micron level or even higher, enabling high-precision thickness measurement of lithium battery electrodes.
Non-Contact: Laser displacement sensors use non-contact measurement methods, avoiding scratches and deformation caused by contact and effectively preventing measurement errors due to contact.
Fast Measurement: Laser displacement sensors have a very fast measurement speed, allowing for the measurement of a large number of samples in a short time, greatly improving production efficiency.
High Degree of Automation: Laser displacement sensors can be used with automated production lines to achieve automated measurement and data acquisition, reducing labor costs and error rates.
Recommended Laser Displacement Sensors
Sensing Distance
|
Repeatability
|
Linearity |
Output
|
30 mm (±5)
|
10 µm
|
±0.1%F.S. |
Analog / RS485
|
50 mm (±15)
|
30 µm
|
NPN / Analog / RS485
|
|
100 mm (±35)
|
70 µm
|
||
200 mm (±80) | 200 µm | ±0.2%F.S. | |
400 mm (±200) | 400 µm / 800 µm | ||
Applications of Laser Displacement Sensors | |||
Laser displacement sensors are versatile measurement tools capable of accurately measuring physical quantities such as length, distance, vibration, speed, and angle. Laser displacement sensors play a crucial role in applications such as small part identification, conveyor belt monitoring, material overlap detection, robotic position control, liquid level monitoring, thickness measurement, vibration analysis, collision testing, and various automotive tests. |
Related Laser Displacement Sensors
By converting from the laser into electrical signals. determine various characteristics,distance, displacement, or position.
By converting from the laser into electrical signals. determine various characteristics,distance, displacement, or position.
Output method: NPN/PNP+analog+RS485
Resolution: 1mm
Laser type: red semiconductor laser Class II laser 655+10nm<1m
Reaction time: 50-200ms
Measure distance: 0.1-50m
By converting from the laser into electrical signals. determine various characteristics,distance, displacement, or position.