Non-Contact Roll Diameter Measurement: Advantages and Applications of Laser Measurement Sensors
- Share
- publisher
- Zoe
- Issue Time
- Sep 14,2024
Summary
In the processing of roll materials, automatic control of unwinding and rewinding is crucial for improving production efficiency and product quality. Roll diameter measurement is divided into contact and non-contact methods, with laser measurement sensors being particularly suitable for applications involving small cores and high-speed operations due to their small detection spot and fast response time.
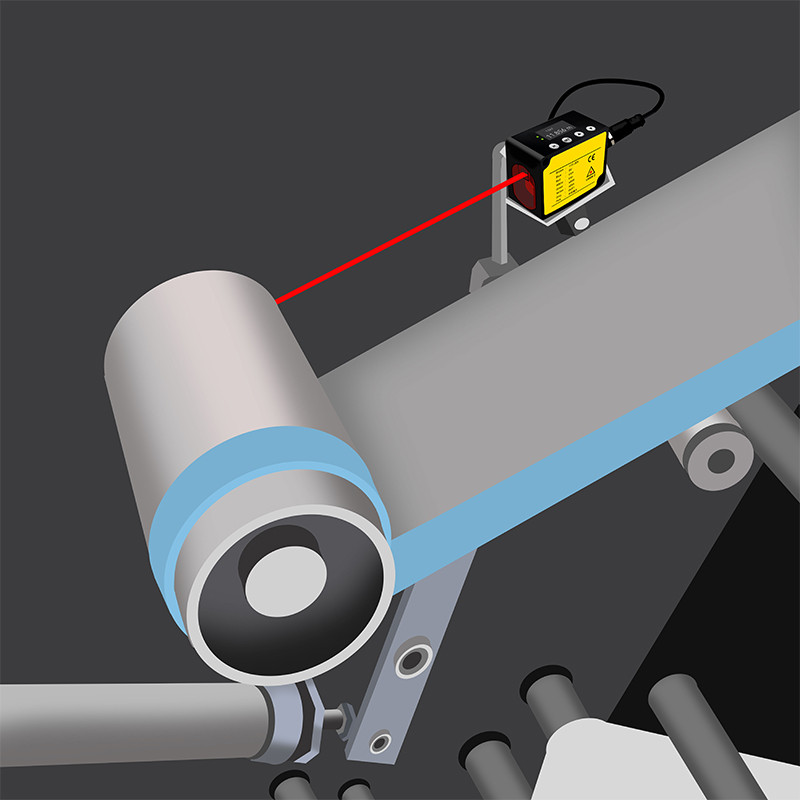
Application Areas of Roll Diameter Measurement
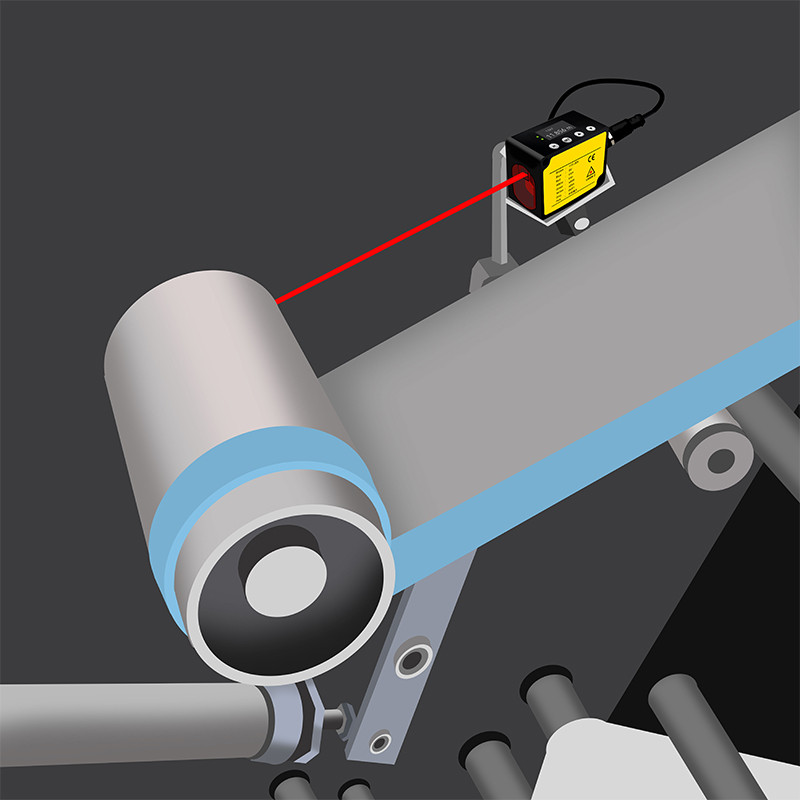
In the processing of roll materials, automatic control of unwinding and rewinding is crucial for improving production efficiency and product quality. Roll diameter measurement sensors, as core components, are widely used in the following areas:
• Film, Paper, and Textile Industries: Assist in controlling the winding and unwinding processes to ensure material tension and quality stability.
Metal Foil and Sheet Industries: Accurate roll diameter measurement helps adjust operating speed, preventing the material from being too tight or too loose.
• Textile Industry: Ensures uniformity and efficiency during the winding of fabric rolls.
• Rubber and Plastic Industries: Monitors the roll diameter of rubber belts, plastic films, etc., in real-time to avoid equipment malfunctions or material waste.
• Cable and Wire Production: Optimizes winding speed, ensuring product quality and length precision.
• Printing and Packaging Industries: Monitor the diameter of paper rolls or packaging materials, optimize equipment speed, and prevent material breakage or waste, especially on high-speed production lines.
Types of Roll Diameter Measurement Sensors
There are two types of roll diameter measurement methods: contact and non-contact.
• Contact methods use mechanical structures, such as wheels or shafts that touch the roll’s outer surface to measure changes in diameter. Common sensors include potentiometers, rotary encoders, limit switches, proximity sensors, etc.
• Non-contact methods measure the distance between the roll and the sensor directly, avoiding errors caused by friction and wear in contact systems. Ultrasonic distance sensors and laser measurement sensors are the most commonly used non-contact sensors, with laser measurement sensors increasingly becoming the preferred choice due to their high precision and fast response.
Working Principles of Different Roll Diameter Sensors
Ultrasonic Distance Sensors
The ultrasonic distance sensor emits ultrasonic waves towards the roll and receives the reflected signal from the roll’s outer surface. By measuring the time difference between emission and reception, it calculates the distance between the sensor and the roll. Although ultrasonic sensors perform well in low-speed, large-diameter applications, their slower response time and lower precision compared to laser measurement sensors limit their use in high-speed and high-precision scenarios. However, due to their excellent cost-effectiveness, ultrasonic sensors remain popular in the market. (More Roll Diameter Measurement Applications)
Laser Measurement Sensors
Laser measurement sensors, Based on the fundamental principles of laser measurement, the methods can be divided into the Time of Flight (ToF) method and the triangulation method. Among them, the Time of Flight method can be further categorized into the Pulse Method (ToF) and the Phase-Shift Method. (See Details of Laser Measurement Sensors Working Principles)
• Phase-Shift Method: Measures the time difference by comparing the phase difference between the emitted and received light signals, providing high accuracy.
• Pulse Method (ToF) Method: Measures the time difference between emitted and reflected light pulses, offering very high precision and fast response, particularly suitable for high-speed roll diameter measurement.
• Triangulation is a geometric measurement method based on triangular relationships. In this method, a laser spot is projected onto the object to be measured, and the reflected light from the object is directed at a certain angle towards the CMOS sensor element. The position of the light spot on the CMOS line changes according to the distance of the object. In this way, even at very small distances, the distance to the object can be precisely determined.
Laser measurement sensors, with their small detection spot and fast response time, are ideal for measuring the diameter of small cores at high speeds. Their non-contact nature avoids mechanical wear and maintains high accuracy and reliability even in extreme conditions.
Advantages and Future Prospects of Laser Measurement Sensors
Roll diameter measurement directly impacts the speed of unwinding and rewinding, as well as tension control. Non-contact methods, especially laser measurement sensors, provide high-precision measurements without touching the material, significantly improving automation accuracy and production efficiency.
Compared to contact methods, laser measurement sensors offer longer service life, lower maintenance costs, and higher precision, helping to reduce material waste and improve product quality. In the future, laser measurement sensors will see broader applications in roll material processing, printing, packaging, and other industries, becoming the preferred technology for roll diameter measurement.
Recommended Distance Measurement Sensors
Output method: NPN/PNP+analog+RS485
Resolution: 1mm
Laser type: red semiconductor laser Class II laser 655+10nm<1m
Reaction time: 50-200ms
Measure distance: 0.1-50m
Measuring frequency: 1Hz-40Hz
Communication interface: RS232/RS485 (switchable)
Measuring distance: 0.2-100m
Measurement resolution: 1mm
Response time: up to 1.5ms
Output type: RS485
Measuring center distance: 200mm
Measuring range: ±80mm
Response time: up to 1.0ms
Repetitive accuracy: up to 2µm
Detection distance: 250mm
Detection range (f. s.): ±150mm