Safely Handling PCB Boards with Robotics
- Share
- publisher
- Zoe
- Issue Time
- Jan 11,2025
Summary
DADISICK’s GFL-Z series laser displacement sensors, with their high precision, compact design, and exceptional real-time feedback capabilities, provide a comprehensive solution for safe robotic handling of PCB boards. This technology not only significantly improves production efficiency and product quality but also demonstrates outstanding adaptability in complex and dynamic industrial environments.
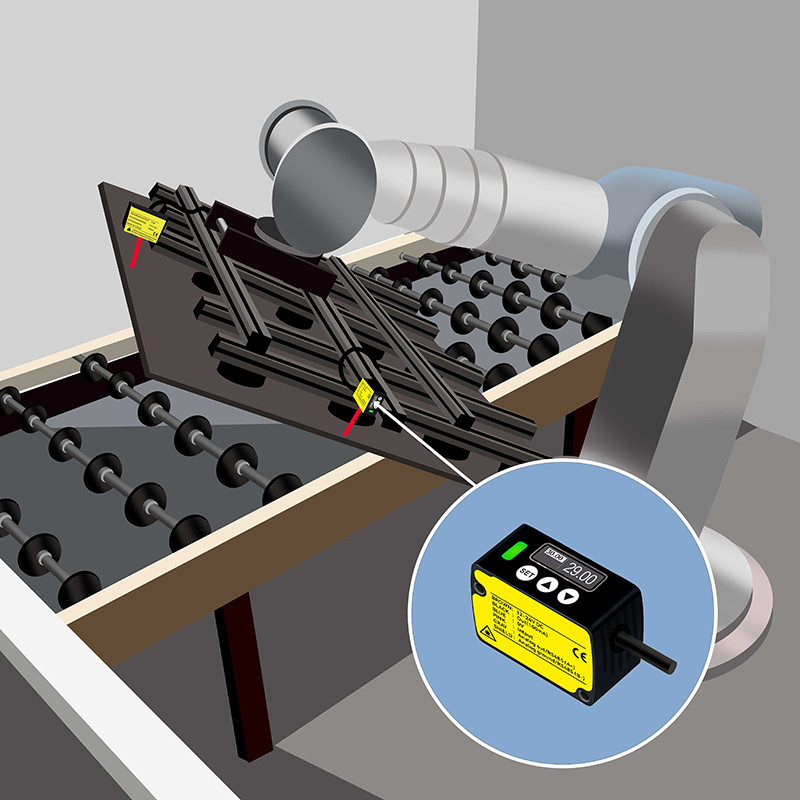
Safely Handling PCB Boards with Robotics
Industrial robots have become indispensable in PCB (printed circuit board) handling, where precision and efficiency are paramount. Leveraging DADISICK's GFL-Z series laser displacement sensors, this solution offers advanced positioning, posture detection, and real-time feedback, setting a new standard in reliable PCB handling processes.
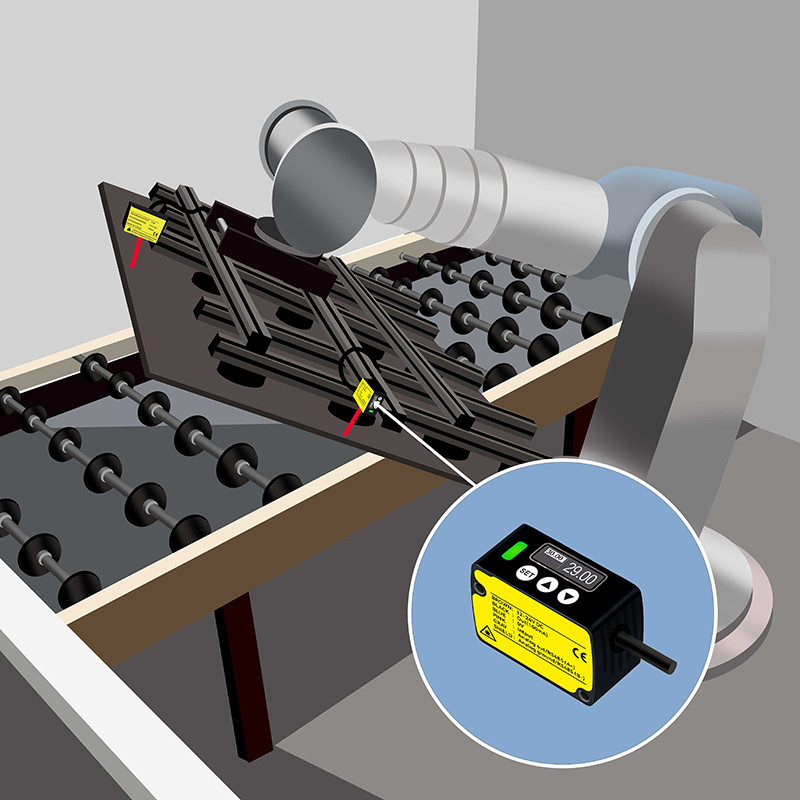
High-Precision Positioning
Initial Positioning
Before the robotic arm picks up the PCB, the GFL-Z series laser displacement sensor accurately measures the PCB’s position on the surface, identifying any deviation relative to the robot’s pre-set pickup location. Based on the triangulation measurement principle, the sensor achieves a repeatability accuracy of 10 µm within a 25 to 35 mm measurement range. By detecting the PCB’s coordinate deviation in the X-Y plane, the sensor provides precise positioning data, ensuring accurate grasping actions and preventing PCB damage caused by incorrect positioning.
Placement Positioning
When the robotic arm transports the PCB to the target location, the laser displacement sensor plays a critical role again, detecting the precise coordinates of the target location. This ensures the PCB is placed at the predefined position with micron-level precision. Such accuracy is essential for subsequent processing steps (e.g., component insertion, soldering), enhancing production efficiency and significantly reducing defects caused by positional errors.
Posture and Deformation Detection of PCBs
Posture Detection
During transportation, the PCB may experience tilting or rotational changes. The laser displacement sensor detects posture changes by measuring height differences at various points on the PCB. For instance, if the sensor identifies that one corner is significantly lower than the others, it can infer that the PCB is tilted. The robotic arm can then adjust its grasping and placement actions accordingly, ensuring proper posture during handling.
Deformation Detection
Due to material properties or external factors (e.g., temperature, pressure), the PCB may deform. The GFL-Z series laser displacement sensor scans the PCB surface and compares the data with standard models to quickly detect deformations. If deformation is detected, the system can take actions such as halting transportation, issuing alerts, or adjusting handling strategies to prevent faults in subsequent processes caused by deformation.
Real-Time Feedback and Path Planning Adjustment
Real-Time Feedback
During the handling process, the laser displacement sensor continuously monitors the relative position of the PCB and its surrounding environment. For example, if the sensor detects a few millimeters of displacement along the Z-axis, the control system can immediately adjust the robotic arm’s movement parameters to maintain positional accuracy throughout transportation.
Path Planning Adjustment
Based on real-time data from the sensor, the robotic arm’s path planning system dynamically adjusts the transportation route. If obstacles are detected along the predefined path or the PCB’s position deviates, the system recalculates a safe and efficient route. This enhances the robotic arm’s flexibility and adaptability in complex production environments.
Recommended Laser Displacement Sensor
The GFL-Z Series displacement sensor is a specialized solution for high-precision measurement tasks, offering versatile applications across various industries. With a measurement range of 25 mm to 35 mm, the GFL-Z Series provides a precision of up to 10 µm. The sensor supports simultaneous reading from up to 12 units, enabling advanced data processing and analysis. It offers features such as:
▪️Statistical Analysis: Max, Min, and Average values for a single data acquisition session.
▪️Waveform Display: Real-time visual display of measurement data, with the option to export to Excel for further analysis.
▪️Differential Calculation: Supports the calculation of differences between two sensors for enhanced accuracy.
▪️User-Defined Limits: Customizable upper and lower limits, with the option to reset the display.
Output Options:
▪️RS485 (MODBUS Protocol)
▪️Analog Output: 0-5V / 4-20mA
▪️Discrete Output (NPN): Customizable to PNP if required.
Possible Solutions
Response time: up to 1.5ms
Repetitive accuracy: up to 10µm
Response time: up to 1.0ms
Repetitive accuracy: up to 2µm
Detection range: 20-120mm
Material: copper nickel plating
Connection type: 4-pin M12 connector
Output method: 1 NPN switch output, NO/NC
Detection distance: 30-150mm, 2M, 10M
Power supply voltage: DC12-24V
No-load current:9mA , 9mA, Reflection 11mA, reception 9mA
Connection method:Wire lead type (standard wire length 2m)