Safety Solutions for Intelligent Human-Robot Collaboration in the Industry 4.0 Framework
- Share
- publisher
- Zoe
- Issue Time
- Sep 18,2024
Summary
In the process of automated robot operations, safety protection is crucial. Common safety devices include safety fences, safety door switches, safety light curtains, safety laser scanners, and safety mats. This article will focus on the application of safety light curtains and safety laser scanners in automated robot work areas, as well as safety protection solutions in human-robot collaborative environments under the framework of Industry 4.0.
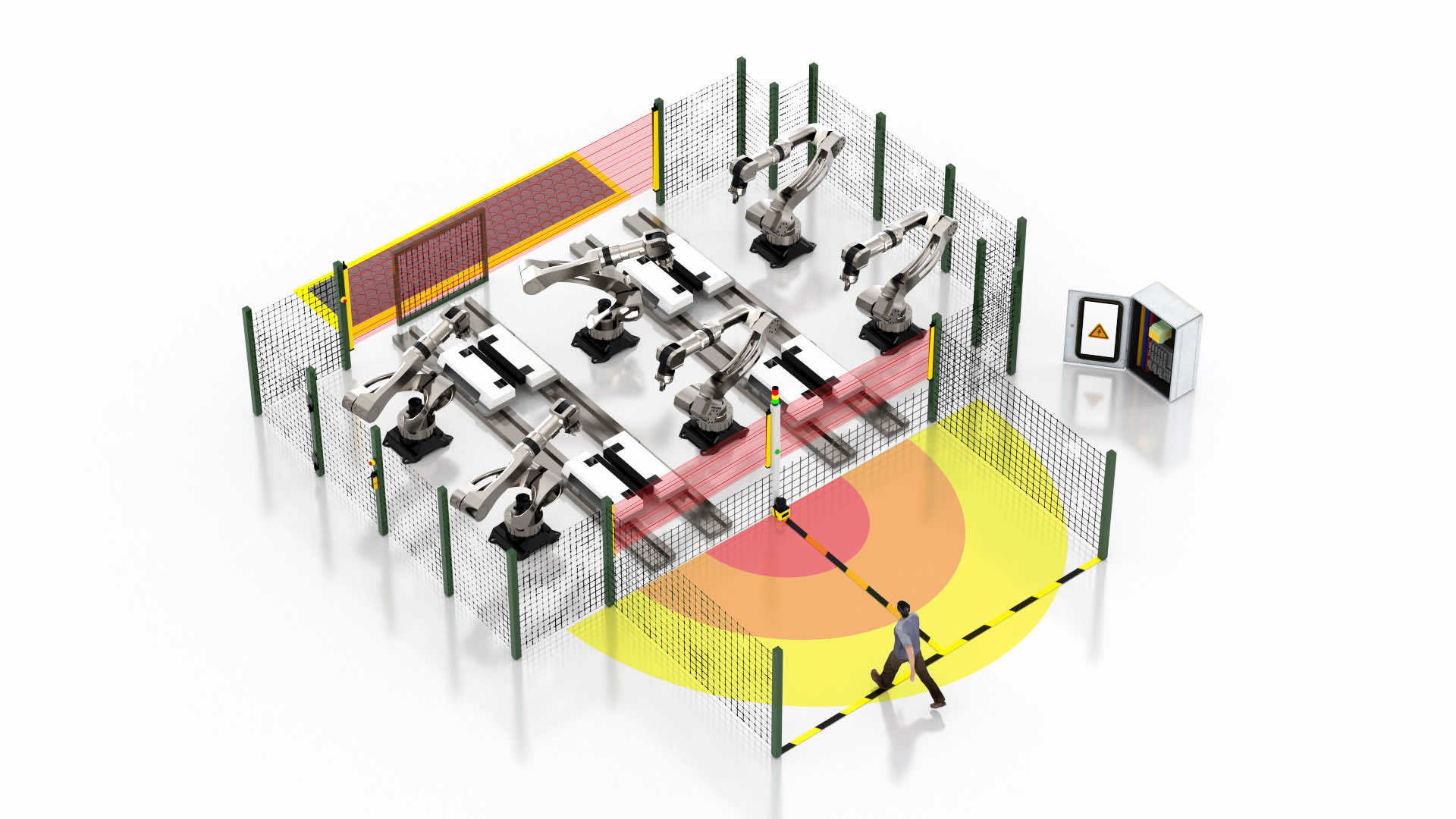
Safety Protection Solutions for Automated Robot Work Areas
In the process of automated robot operations, safety protection is crucial. Common safety devices include safety fences, safety door switches, safety light curtains, safety laser scanners, and safety mats. This article will focus on the application of safety light curtains and safety laser scanners in automated robot work areas, as well as safety protection solutions in human-robot collaborative environments under the framework of Industry 4.0.
Safety Solutions for Intelligent Human-Robot Collaboration in the Industry 4.0 Framework
With the development of Industry 4.0, robots are increasingly being used to replace humans in performing repetitive tasks, thus improving production efficiency. However, since industrial robots move quickly and exert considerable force, serious accidents may occur if personnel accidentally approach their work areas. Therefore, strict safety monitoring of the robots and their working environments is essential, especially real-time monitoring and control of the robot's force, speed, and movement trajectory.
According to the EU Machinery Directive and international standards such as ISO 13849-1, all machinery in operation must be equipped with the necessary safety protection devices. In some countries and regions, the responsibility for safety is borne by the equipment users, requiring companies to provide a safe working environment and ensure that employees are not harmed while operating robots.
Traditional industrial robots are usually installed in fixed positions, are bulky, and difficult to move. However, with the advancement of technology, lightweight, flexible, and easy-to-move new-generation robots are gradually becoming the market mainstream. These collaborative robots can be easily moved to different work areas, creating a demand for more flexible and safe protection solutions.
In the human-robot collaborative environment of Industry 4.0, robots not only need to perform tasks precisely but must also meet stricter safety standards. The robot's force, speed, and movement trajectory must be monitored at all times, and restrictions must be applied based on actual risks. Risk assessments are crucial, as the results dictate the appropriate risk reduction measures—such as the use of safety light curtains or safety laser scanners—to ensure a safe distance between humans and machines, thereby protecting the safety of personnel.
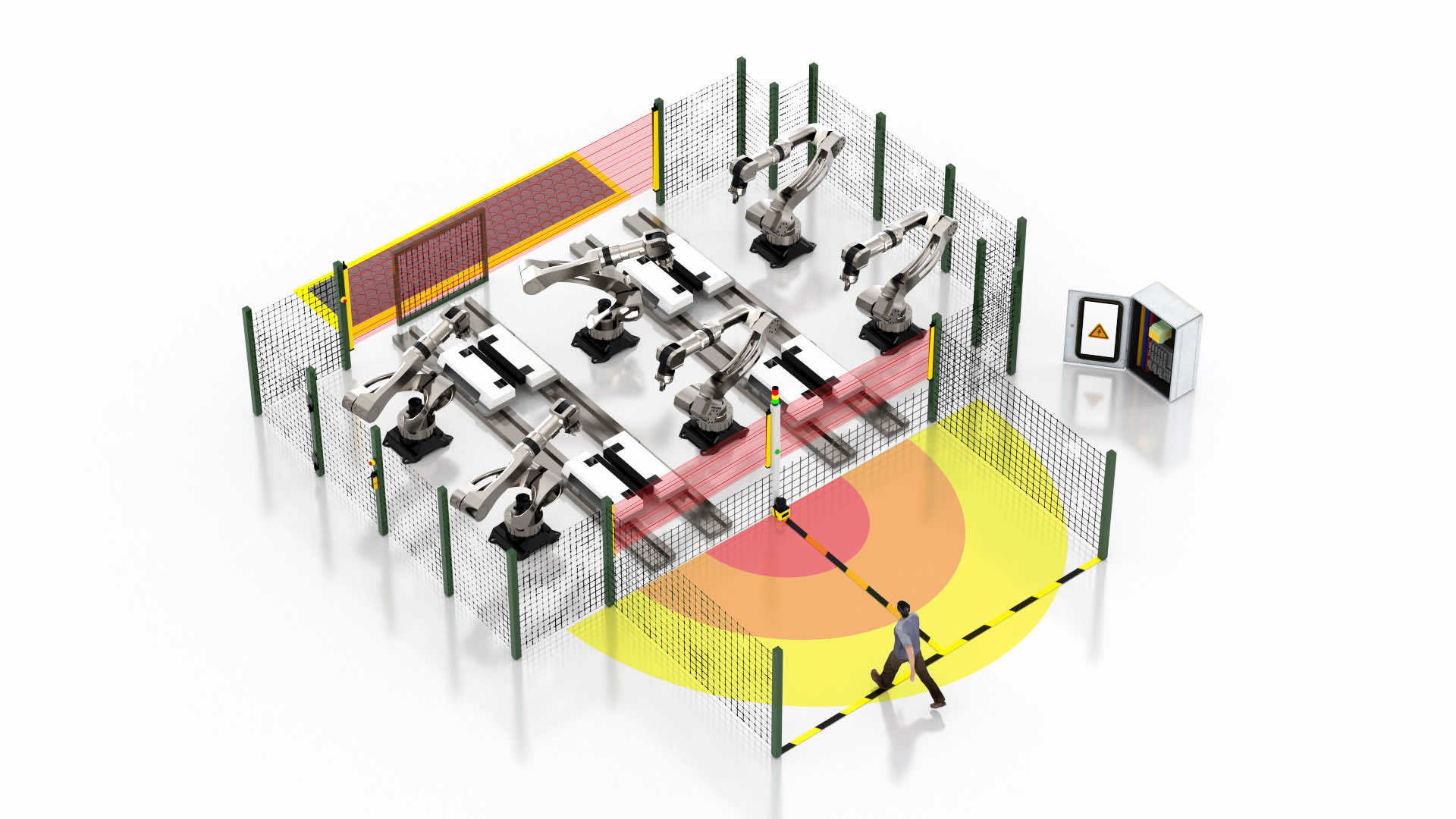
Working Principle of Safety Light Curtains
A safety light curtain provides protection by emitting a row of parallel light beams across the protected area. When a person or object interrupts the beams, the receiver unit immediately sends a signal to the machine's control system, causing the equipment to stop operating. The advantage of safety light curtains lies in their simple structure and quick response, making them ideal for emergency stop scenarios during mechanical motion.
Working Principle of Safety Laser Scanners
In contrast to safety light curtains, safety laser scanners achieve protection through distance settings. The safety laser scanner works on the time-of-flight (TOF) measurement principle, emitting infrared laser pulses to create a detection zone. When an object is detected, the laser pulse is reflected from the object's surface back to the scanner, which calculates the object's distance based on the time difference between emission and reception.
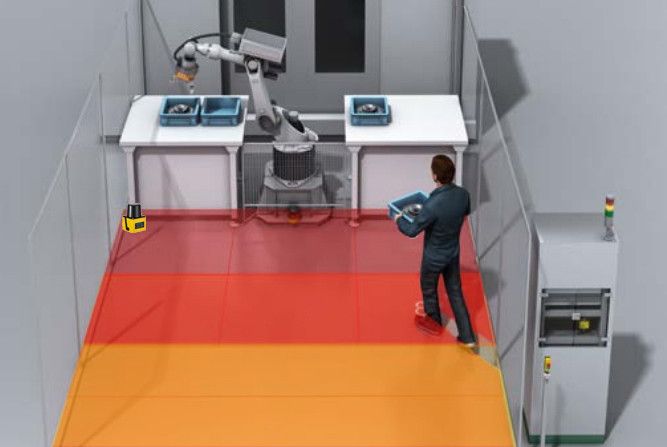
Specific Operational Process
Using DADISICK's safety laser scanner as an example, users can customize detection zones, including collaboration zones and warning zones. In automated operations, if personnel need to enter the robot’s work area to place objects (i.e., the collaboration zone), the system will indicate the current zone status via the color of the signal lights. A yellow light indicates that the operator has entered the collaboration zone, and the robot will slow down; if the operator enters the warning zone, a red light will turn on, accompanied by sound and visual alarms, indicating that the operator has entered a dangerous area, and the robot will stop completely. Once the operator leaves the protected zone, the system and robot will automatically resume operation without manual intervention, ensuring convenience and safety in the operational process.
Key Components of Safety Devices and Machine Control Systems
The Output Signal Switching Device (OSSD) is a key component widely used in the field of industrial automation safety, primarily designed to establish effective connections and signal transmission between safety devices and machine control systems.
Working Principle
OSSD is typically used in conjunction with sensors (such as light curtain sensors or laser scanners) to monitor the sensor status and determine if any objects or personnel have entered a hazardous area.
When the sensor detects an intrusion, it sends a signal to the OSSD, which then converts this signal into a format recognizable by the machine control system and transmits it to the control system.
Once the control system receives the OSSD signal, it will execute the appropriate safety measures according to the preset safety logic, such as emergency shutdown or speed reduction.
Application Scenarios
OSSD is widely applied in various industrial automation equipment and production lines, especially in scenarios that require personnel safety protection, such as robotic work areas, stamping machine production lines, and automated assembly lines.
In these scenarios, the OSSD works in coordination with safety devices like safety light curtains, safety door switches, and safety mats, forming a complete safety protection system that effectively reduces the risk of accidents.
2D TOF Obstacle Avoidance Safety Laser Scanners
Technical data
|
||||
Working principle
|
Time-of-flight (TOF) measurement principle |
|||
IO output | NPN or PNP | |||
Work area | 0.05 m ~ 5 m | 0.05 m ~ 20 m | ||
Laser source
|
905 nm (class I) |
|||
Aperture angle
|
270° |
|||
Scanning frequency | 15 Hz / 30 Hz | |||
Angular resolution | 0.1° / 0.3° | |||
Self-learning function | Automatically scan the environment and generate areas | |||
Electrical connections | Db15 Male / Scatter | |||
Supply voltage | DC 9 V ~ 28 V | |||
Power consumption | 2 W | |||
Switch drive | DC 30 V 50 mA max. | |||
Shell color | Yellow | |||
Enclosure rating | IP65 | |||
Weight | 150 g (cable not included) | |||
Dimensions (L × W × H) | 50 × 50 × 76 mm | |||
Detectable object shape | Almost any shape | |||
Measurement error | ±30 mm | |||
Number of field sets | 16 fields, 3 simultaneous protective fields (per field set) | |||
Connection type | Micro-USB | |||
Input | GND/NC × 4 | |||
Switch output | NPN × 3, device working status; PNP × 3, device working status | |||
Delay time | 100 ms ~ 10,000 ms (configurable), typical value 330 ms | |||
Response time | 15 Hz: 67 ms ~ 29,949 ms (configurable), typical value 134 ms; 30 Hz: 33 ms ~ 29,997 ms (configurable), typical value 66 ms | |||
Status Indicator | Status indicator × 1, area group indicator × 3 | |||
Vibration resistance
| 10 - 55 Hz, amplitude 0.75 mm, XYZ three-axis, 2 hours per axis;
50 - 200 Hz, 196 m/s² (20G), scanning speed 2 min/cycle, XYZ three-axis, 2 hours per axis; | |||
Ambient operating temperature | -10 ℃ ~ +55 ℃ | |||
Storage temperature | -30 ℃ ~ +75 ℃ | |||
Ambient light immunity | >15,000 lux |