The Proper Installation and Usage Guide for Ultrasonic Sensors
- Share
- publisher
- Zoe
- Issue Time
- Sep 3,2024
Summary
This article mainly introduces how to correctly install ultrasonic sensors. Installation requirements include ensuring the correct installation angle, maintaining sufficient sensor spacing to avoid interference, considering environmental factors such as temperature and wind speed, and achieving effective detection in confined spaces by adjusting angles or using accessories. Additionally, using synchronous or asynchronous functions can ensure the measurement accuracy of multiple sensors.
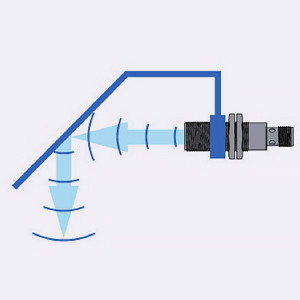
Installation and Operation Instructions for Ultrasonic Sensors
Ultrasonic sensors can be used in harsh environments, but water droplets and excessive dust accumulation may affect the normal output of the ultrasonic waves. Fine dust and non-accumulating stains, however, will not affect normal operation.
When detecting targets with smooth and highly flat surfaces, the sensor should be installed at an angle of 90°±3° to the front of the detected object. Avoid excessive installation angles to ensure the sensor can receive the reflected sound waves.
For targets with rough surfaces, the sensor's installation angle can be greater than 3°. Due to the inherent characteristics of sound waves, when detecting materials with strong sound absorption, such as cotton, sponge, and special fabrics, the sensor’s effective detection range may be shortened. The specific installation conditions should be determined based on on-site adjustments.
During model selection, testing should be conducted according to the different materials to ensure accuracy.
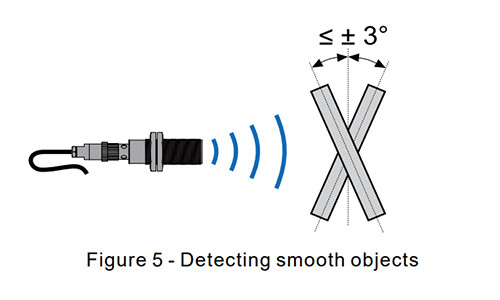
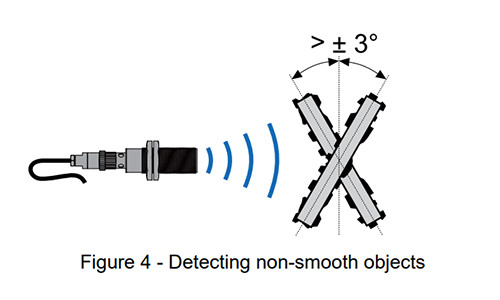
Ultrasonic Sensor Installation Spacing
When using two or more sensors of the same model, if the installation distance is too close, it may cause frequency interference between the sensors, leading to abnormal outputs. To avoid this, ensure sufficient distance between multiple sensors of the same model during installation.
The recommended installation distances are as follows:
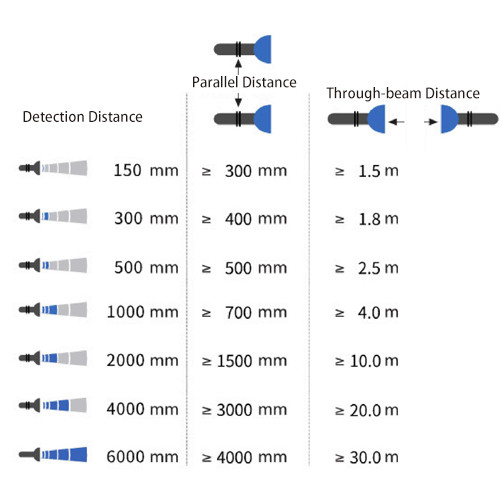
Ultrasonic Sensor Synchronization Function
When installing multiple sensors, if the installation spacing is less than the distance that may cause mutual interference, the synchronization or asynchronous function should be used. These functions control multiple sensors to measure simultaneously.
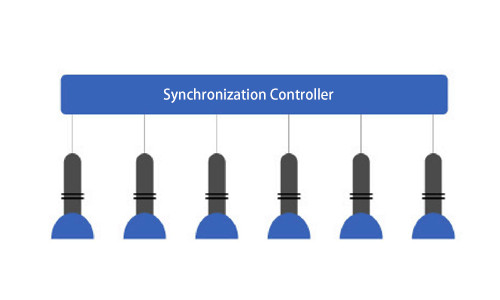
Ultrasonic Sensors With Synchronization and Learning Function
DADISICK's ultrasonic sensors are equipped with a synchronization function. Whether using sensors of the same model or different models, synchronization or asynchronous functionality can be achieved through a synchronization controller.
Application of Sound Wave Reflection Characteristics
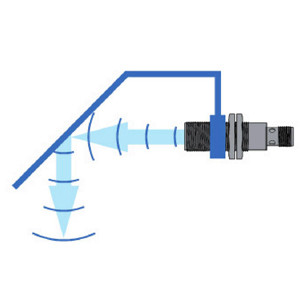
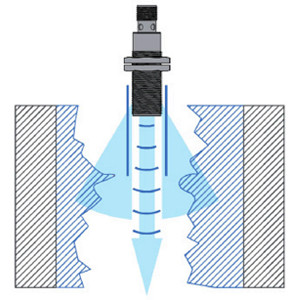
The sound wave beam experiences minimal attenuation after being reflected and redirected by a smooth reflective surface.
By using appropriate accessories or adjusting the installation angle, the propagation direction of the sound wave can be deflected, allowing the sensor to be installed and used in confined environments.
Effect of Temperature on Ultrasonic Sensors
Temperature is the most significant factor affecting the accuracy of ultrasonic sensors. The speed of sound waves in air varies with temperature. Generally, for every 1℃ change in temperature, the measurement accuracy is affected by approximately 0.17%. All DADISICK ultrasonic sensors are equipped with a temperature compensation circuit, keeping the repeatability error controlled to around 0.15%.
Detection range: 20-120 mm
Detection range: 20-200 mm
Material: copper nickel plating
Connection type: 4-pin M12 connector
Detection range: 30-300 mm, 50-500 mm, 60-1000 mm
Material: copper nickel plating, plastic fittings
Connection type: 5-pin M12 connector
Detection range: 30-300 mm, 50-500 mm, 60-1000 mm
Material: copper nickel plating, plastic fittings
Connection type: 5-pin M12 connector
Detection range: 100-2000 mm, 200-4000 mm, 350-6000 mm
Material: copper nickel plating, plastic fittings
Connection type: 5-pin M12 connector
Detection range: 60-1000mm, 150-2500 mm
Material: copper sleeve nickel plated
Connection type: 5-pin M12 connector
Emitter - receiver spacing: 20-40 mm, 20-60 mm, 20-100 mm
Material: nickel plated copper, plastic fittings
Connection type: 2 m, PVP cable, 0.14 mm²
Groove depth: 68 mm
Slot width: 5 mm
Material: metal, aluminum
Connection type: 4-pin M8 connector
Detection range: 100-2000 mm
Material: plastic accessories, filled with epoxy resin
Connection type: 5-pin M12 connector
Output method: 1 NPN, NO/NC
Effects of Air Pressure, Airflow, and Humidity on Ultrasonic Sensors
Air pressure below 3,000 meters of altitude has minimal impact on ultrasonic sensors. Above 3,000 meters, the testing distance may shorten, so testing is recommended to determine suitability. Wind speeds below 60 km/h have almost no effect on ultrasonic sensors, so it is recommended to use them under wind speeds of less than 60 km/h. The impact of air humidity on ultrasonic sensors is negligible.