Ultrasonic Sensors in Fully Automated Terminal AGV Applications
- Share
- publisher
- Zoe
- Issue Time
- Dec 6,2024
Summary
Ultrasonic sensors play a pivotal role in ensuring the safety and efficiency of AGV operations at fully automated terminals like Qingdao Port. Their precise measurement and real-time monitoring capabilities make them a reliable and cost-effective solution for container handling systems. As automation continues to evolve, ultrasonic sensors are poised to remain a critical component in the future of smart port operations.
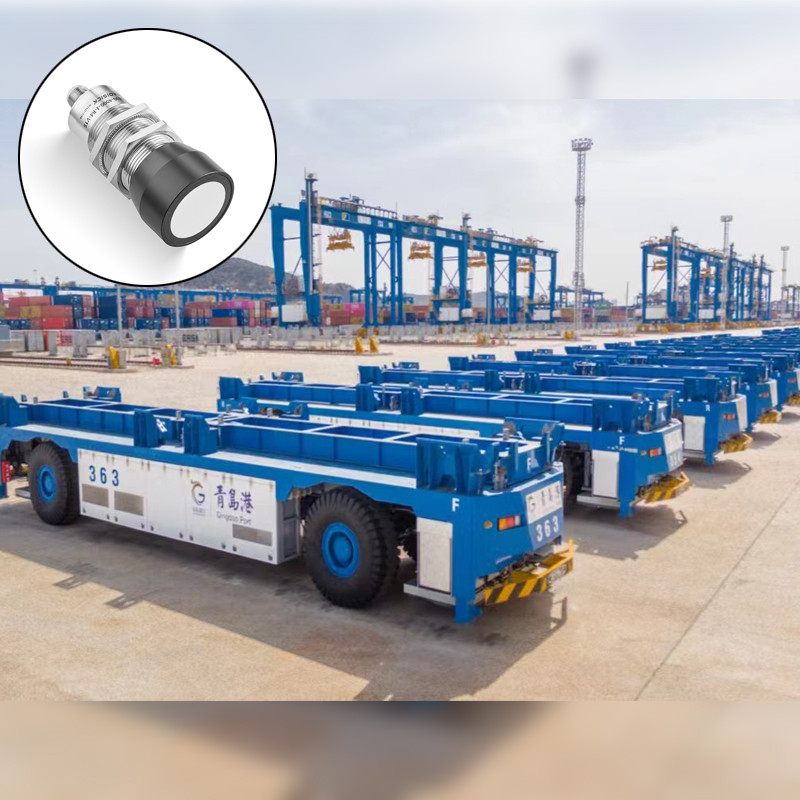
Project Background
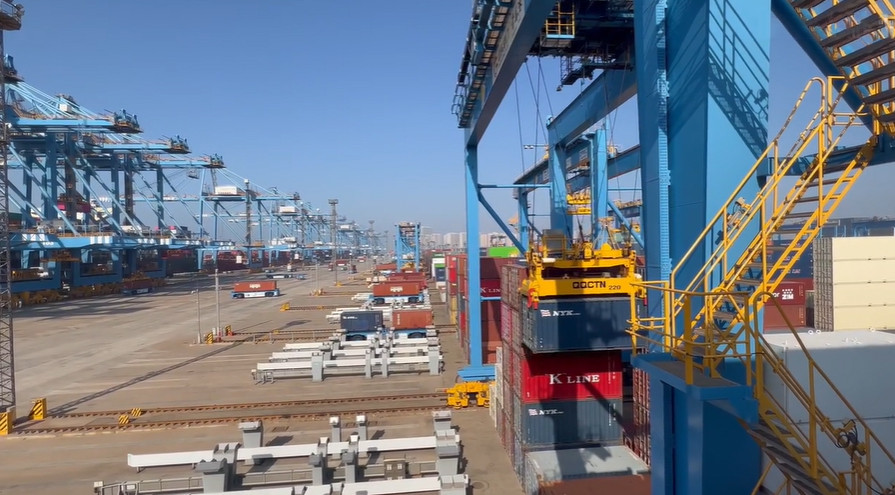
Shandong Qingdao Port, one of the world's leading fully automated terminals, boasts a top-tier cargo throughput capacity. By integrating advanced automation technology, the port has achieved high-efficiency operations without on-site manual intervention. Traditional port operations required at least three operators for bridge cranes and AGVs. However, automation has reduced on-site labor needs by 80% while increasing economic efficiency by 30%.
In this automated container terminal, ultrasonic sensors are utilized to ensure precise positioning between AGVs and containers. This prevents potential hazards caused by container misalignment or accidental drops during transport.
AGV Operating Environment

1️⃣ Operational Zones:
AGVs handle horizontal transport tasks between the quay and yard, operating in zones such as:
◾Horizontal Transport Zone: Transfers containers from quay cranes to storage yards.
◾Landside Exchange Zone: Interfaces with trucks to load and unload containers.
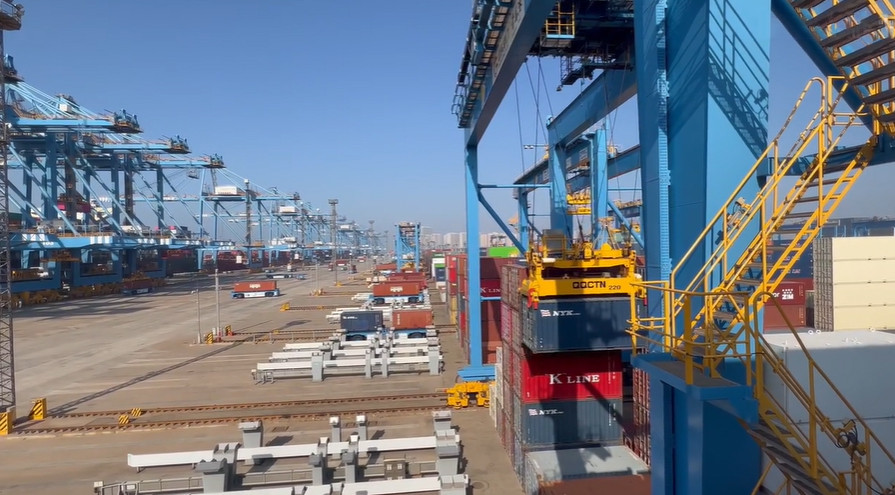
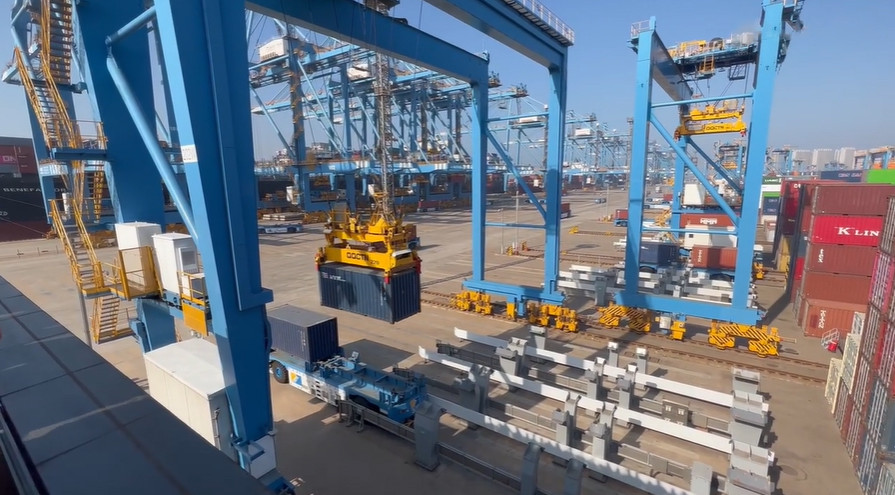
2️⃣ Operational Characteristics:
◾High Precision: AGVs follow predefined paths and task requirements from the control center, ensuring precise navigation and docking.
◾Real-Time Communication: Continuous data exchange with the control center ensures efficient task execution.
◾Challenging Workflows: The container handling process includes lifting, sliding, loading, and turning, requiring highly accurate monitoring systems.
System Architecture
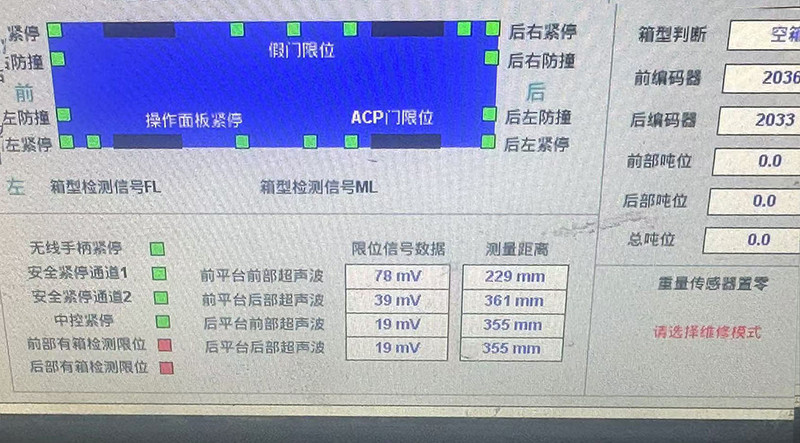
Ultrasonic sensors are connected to the AGV’s control system via data cables for real-time transmission of measurement data. The control system processes sensor data to calculate the relative position between the AGV and the container, adjusting the AGV’s trajectory to ensure accurate docking and transport.
Working Principle
1️⃣ Signal Emission and Reception:
When the AGV approaches a container, the ultrasonic sensors emit ultrasonic signals. These signals are reflected back upon hitting the container and received by the sensors.
2️⃣ Distance Calculation:
By measuring the round-trip time of the ultrasonic signals, the system calculates the distance between the AGV and the container. Using data from all four sensors, the control system determines the AGV’s precise position for accurate container alignment.
3️⃣ Dynamic Adjustment:
Based on real-time measurements, the control system dynamically adjusts the AGV’s trajectory to ensure proper docking and smooth container handling operations.
Real-Time Monitoring and Alarms
1️⃣ Monitoring Functionality:
The system provides real-time monitoring of the relative position between the AGV and the container, displaying sensor output and measurement data on the interface.
2️⃣ Alarm Mechanism:
If the AGV deviates from the designated position or detects improper container alignment, the system triggers an alarm, alerting operators to take corrective action and avoid safety risks.
Key Functions of Ultrasonic Sensors
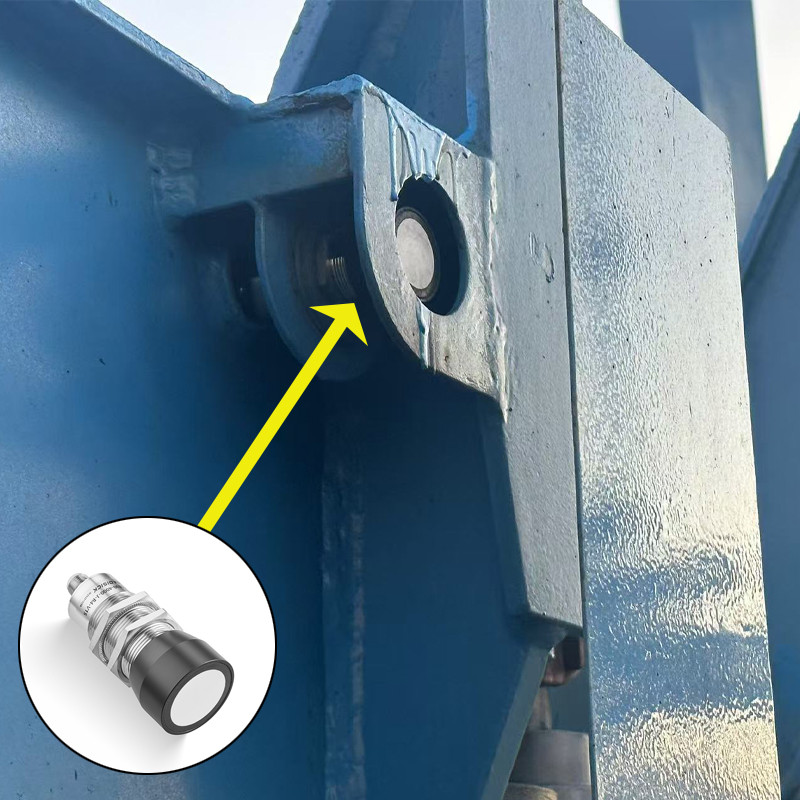
Each AGV is equipped with four ultrasonic sensors, installed at the vehicle’s corners and aligned with the container's four corner castings. Their primary functions include:
1️⃣ Container Position Detection:
Continuously detects whether the container is properly placed on the AGV. If misalignment is detected, the system sends an alert to the control system to prevent potential risks like tipping or falling during transportation.
2️⃣ High Reliability:
Designed to withstand harsh port environments, including high humidity, vibration, and dust, ensuring long-term stable operation.
3️⃣ Efficient Communication:
Integrated with the AGV’s control system via Ethernet interfaces, enabling real-time data transmission and enhancing overall system efficiency.
System Advantages
1️⃣ Enhanced Safety:
Ultrasonic sensors monitor container alignment in real time, preventing accidents caused by misaligned or dropped containers.
1️⃣ Improved Operational Efficiency:
Ensures precise docking, reducing the time spent adjusting container placement and boosting terminal productivity.
1️⃣ Reduced Labor Costs:
Automation significantly reduces on-site manpower requirements, offering a cost-effective and efficient operational model.
Recommended Ultrasonic Sensors
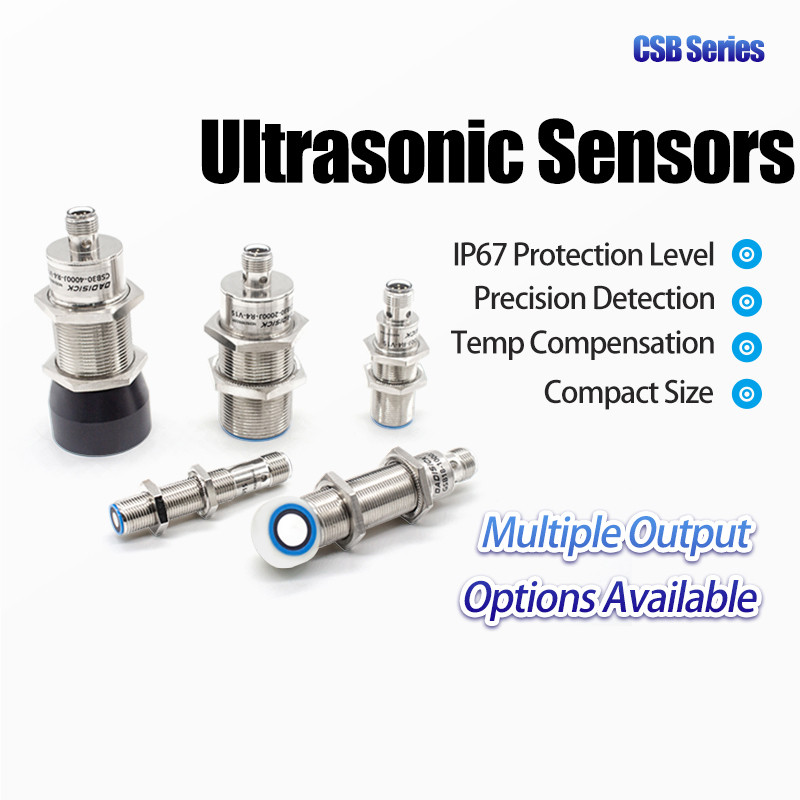
Ultrasonic Sensors Features:
Ultrasonic sensors are renowned for their high reliability and outstanding versatility, capable of handling complex detection tasks such as millimeter-level object detection and liquid level measurement. Their measurement methods ensure stable operation under almost all environmental conditions, demonstrating unparalleled adaptability.
Additionally, these sensors are designed to be rugged and durable, making them suitable for harsh working environments. The sensor surface features a vibration-based self-cleaning function, effectively preventing the accumulation of dust and debris. Leveraging the physical principle of sound wave propagation, ultrasonic sensors operate reliably in nearly all environments, with only a few exceptional cases.
Ultrasonic sensors are widely used in the following industrial sectors:
◾Mechanical Engineering / Machine Tools
Ultrasonic sensors are widely used in the following industrial sectors:
◾Mechanical Engineering / Machine Tools
◾Woodworking and Furniture Manufacturing
◾Building Materials Production
◾Agriculture and Livestock
◾Pulp and Paper Industry
◾Material Handling and Logistics
◾Liquid Level Measurement and Monitoring
◾Food and Beverage Industry
◾Building Materials Production
◾Agriculture and Livestock
◾Pulp and Paper Industry
◾Material Handling and Logistics
◾Liquid Level Measurement and Monitoring
◾Food and Beverage Industry
◾Construction and Infrastructure
Ultrasonic Sensors Output Type | Stands for |
||
Switching Quantity
|
Single Switching Quantity
|
1 PNP
|
E3/E5
|
1 NPN
|
E2/E4
|
||
Dual Switching Quantity | 2 PNP | E6/E8 | |
2 NPN | E7/E9 | ||
PNP + NPN | E | ||
Analog Quantity
|
Single Analog Voltage
|
Analog Voltage 0-10 V
|
U
|
Single Analog Current | Analog Current 4-20 mA | I | |
Analog Voltage + Current Dual Output | 0-10 V + 4-20 mA | IU | |
Analog Voltage + PNP Switch Dual Output | Analog Voltage 0-10 V + PNP | UE5 | |
Analog Current + PNP Switch Dual Output | Analog Current 4-20 mA + PNP | IE5 | |
Analog Voltage + NPN Switch Dual Output | Analog Voltage 0-10 V + NPN | UE4 | |
Analog Current + NPN Switch Dual Output | Analog Current 4-20 mA + NPN | IE4 | |
Digital Quantity | RS485 Output with Modbus Protocol | R4 | |
IO-Link | IO-Link | IO |
Related Non Contact Distance Measurement
Detection range: 20-120 mm
Detection range: 20-200 mm
Material: copper nickel plating
Connection type: 4-pin M12 connector
Detection range: 60-1000mm, 150-2500 mm
Material: copper sleeve nickel plated
Connection type: 5-pin M12 connector
Detection range: 30-300 mm, 50-500 mm, 60-1000 mm
Material: copper nickel plating, plastic fittings
Connection type: 5-pin M12 connector
Detection range: 100-2000 mm, 200-4000 mm, 350-6000 mm
Material: copper nickel plating, plastic fittings
Connection type: 5-pin M12 connector