Utilizing Laser Displacement Sensors for Precise PCB Component Height Detection
- Share
- publisher
- Zoe
- Issue Time
- Jan 13,2025
Summary
This article explores how GFL-G Series laser displacement sensors optimize PCB manufacturing by enabling precise, non-contact component height detection. It details common inspection methods, highlights the sensors' working principles and advantages, and provides a step-by-step implementation guide to improve welding quality and production efficiency.
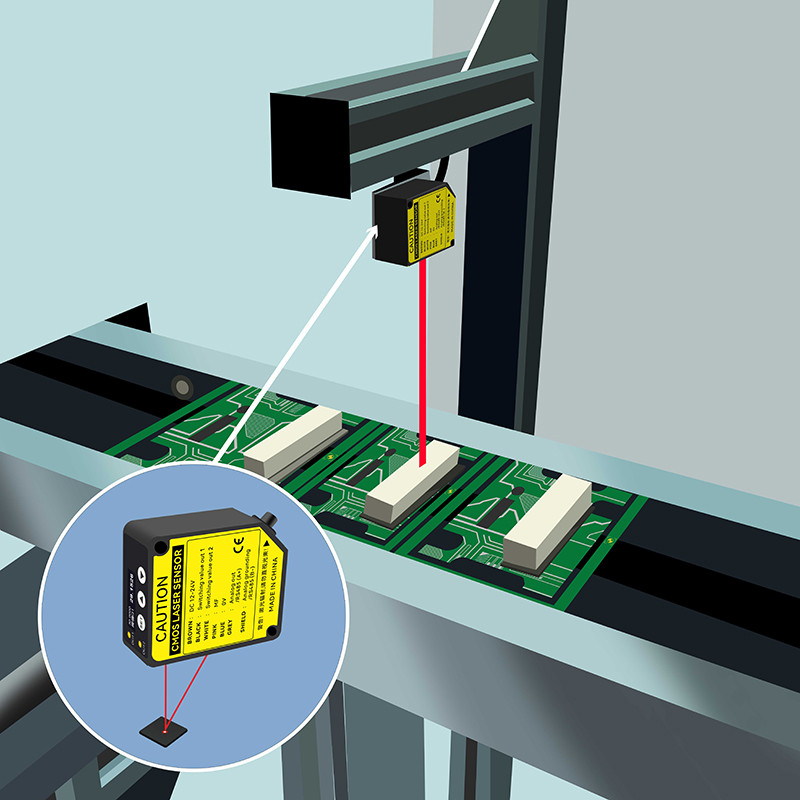
Utilizing Laser Displacement Sensors for Precise PCB Component Height Detection
In the production of printed circuit boards (PCBs), welding errors are a major bottleneck affecting product quality and production efficiency. By accurately measuring component heights, welding defects can be significantly reduced, and production processes can be optimized. This solution proposes the use of GFL-G series laser displacement sensors to achieve fast, flexible, and cost-effective height detection, helping companies improve product quality and reduce production costs.
Working Principle and Advantages of Laser Displacement Sensors
1. Working Principle
Laser displacement sensors use the laser triangulation principle for non-contact height measurement. When the laser beam hits the target surface, the sensor’s internal receiver measures the displacement of the reflected light path to calculate height information, achieving high-precision measurement with advanced signal processing technology.
2. Advantages
▪️The GFL-G series achieves a resolution of 0.002 mm, making it capable of detecting extremely small height variations in components.
▪️High-speed sampling and high-precision performance meet the stringent requirements of PCB manufacturing.
▪️Non-contact measurement avoids damage caused by mechanical contact, making it ideal for sensitive component inspections.
Implementation of the Solution Using GFL-G Series Laser Displacement Sensors
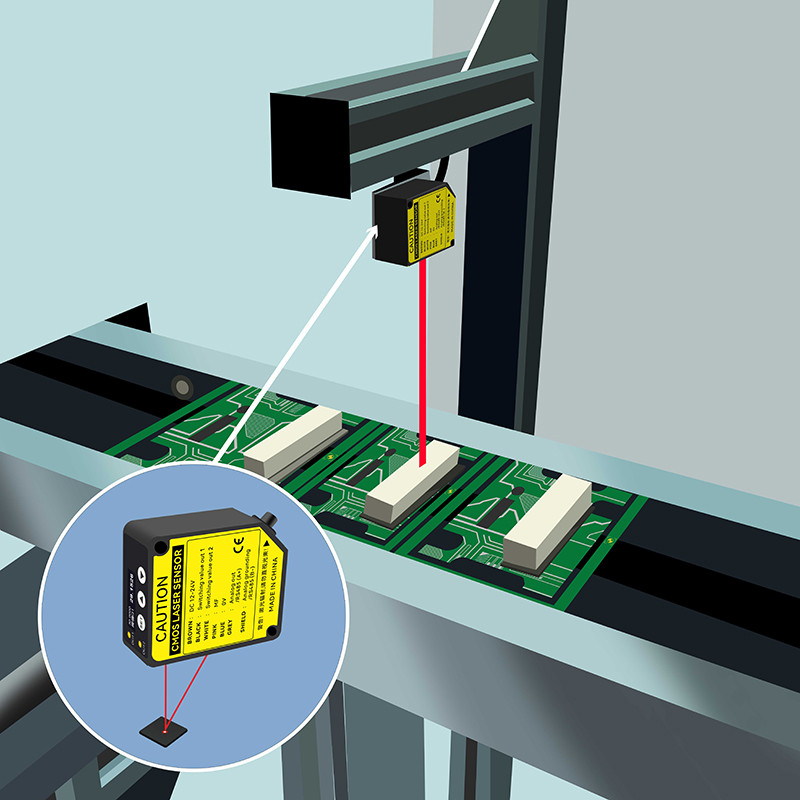
1. Equipment Selection and Installation
▪️Select the appropriate GFL-G series model (e.g., GFL-G30N(P)-485 or GFL-G250N(P)-485) based on PCB size, component height distribution, and precision requirements.
▪️Install sensors on precision rails or adjustable brackets to ensure stable measurement and detection angles.
▪️Minimize external vibrations and strong light interference during installation to ensure a stable working environment for the sensors.
2. Measurement Process Setup
▪️Calibrate the sensor before measurement to ensure data accuracy.
▪️Perform height data collection for key components before and after welding, focusing on height changes at welding positions.
3. Data Processing and Analysis
▪️Integrate sensor output signals into the enterprise’s MES system for real-time monitoring and data storage.
▪️Use intelligent algorithms to analyze height deviations and provide early warnings for potential issues.
Benefits for Your Business
By implementing the GFL-G series laser displacement sensors, companies can significantly enhance PCB production quality and welding accuracy, reduce rework rates and material waste, and ultimately achieve cost reduction and efficiency improvements. This high-precision detection solution also helps companies meet higher customer standards, boosting market competitiveness.
Possible Solutions
Response time: up to 1.0ms
Repetitive accuracy: up to 2µm
Response time: up to 1.5ms
Repetitive accuracy: up to 10µm
Detection range: 20-120 mm
Detection range: 20-200 mm
Material: copper nickel plating
Connection type: 4-pin M12 connector
Maximum detection distance: 2 - 150 mm
Stable detection distance: 3 - 120 mm
Power supply voltage: 12 - 24 V DC
Switch output: NPN/PNP
Connection type: Cable, 4 cores, 2 m