What is an Ultrasonic Sensor?
- Share
- publisher
- Zoe
- Issue Time
- Aug 22,2024
Summary
This article explains the working principles, types, and applications of ultrasonic sensors, particularly in the medical, industrial, and automotive fields. It details the operation of piezoelectric ultrasonic sensors, discusses key factors in sensor selection, and compares ultrasonic sensors with sonar sensors. The article also provides advice on maintaining sensor performance in unstable environments.
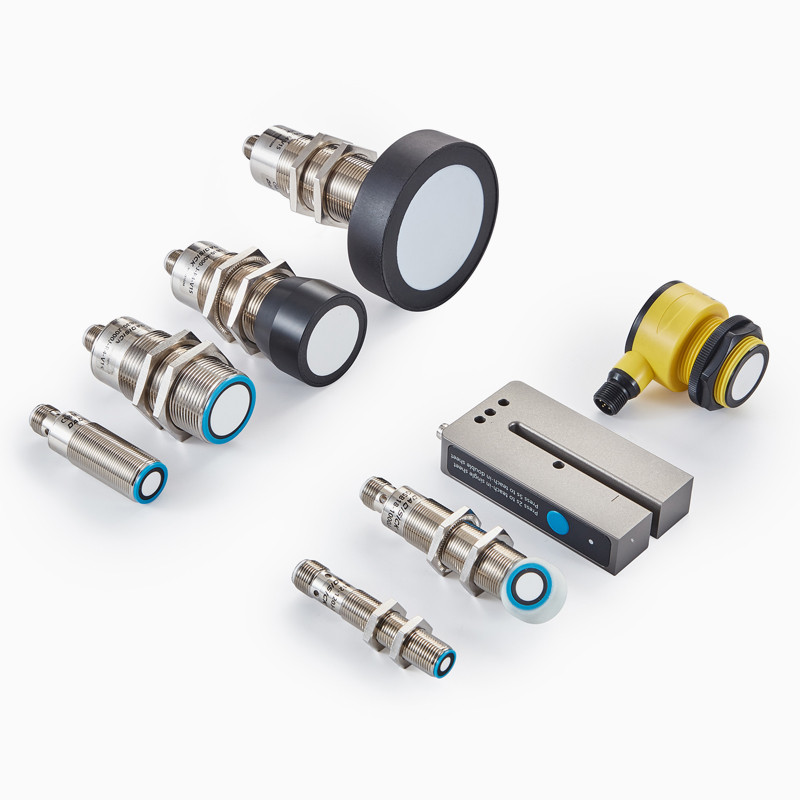
What is an Ultrasonic Sensor?
An ultrasonic sensor is a device that converts ultrasonic signals into other forms of energy, typically electrical signals. Before we introduce ultrasonic sensors, let's first understand the basics of ultrasonic waves.
Sound waves are mechanical waves that can propagate through gases, liquids, and solids. Based on frequency, sound waves can be categorized into infrasound, sound waves, and ultrasound. Ultrasound usually refers to sound waves with frequencies that exceed the lower frequency and audible range (20 Hz to 20 kHz), which are inaudible to humans.
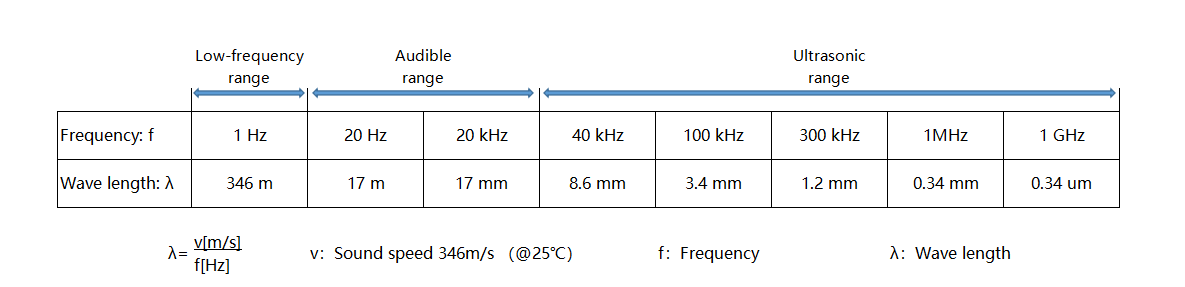
Ultrasonic Wave Propagation Speed:
Ultrasonic waves typically include longitudinal waves, transverse waves, and surface waves, and their propagation speed depends on the elastic constants and density of the medium. Only longitudinal waves can propagate in gases and liquids, with a sound speed of 346 m/s in gases and 900-1900 m/s in liquids. In solids, the speed of longitudinal waves, transverse waves, and surface waves are interrelated. Generally, the speed of transverse waves is half that of longitudinal waves, and the speed of surface waves is about 90% of the speed of transverse waves.
As ultrasonic waves propagate through a medium, their energy gradually attenuates with increasing propagation distance. The attenuation of energy is determined by the diffusion, scattering, and absorption of ultrasonic waves.
Ultrasonic Sensors:
Devices that use ultrasonic waves as a detection method and can generate and receive ultrasonic waves are called ultrasonic sensors. There are various types of ultrasonic sensors with different structures, including straight probes (longitudinal waves), angled probes (transverse waves), surface wave probes (surface waves), Lamb wave probes (Lamb waves), and dual probes (one probe for transmitting and one for receiving).
Working Principle of Ultrasonic Sensors
Based on their working principle, ultrasonic sensors can be categorized into piezoelectric, magnetostrictive, and electromagnetic types, with piezoelectric sensors being the most commonly used.
Piezoelectric Ultrasonic Sensors:
A piezoelectric ultrasonic sensor is a sensor that uses the piezoelectric effect to generate ultrasonic waves. Its basic working principle can be divided into two parts: ultrasonic wave emission and reception.
Ultrasonic Wave Emission:
When the piezoelectric material in the sensor is subjected to external mechanical vibration, the positive piezoelectric effect causes an uneven distribution of electric charges, resulting in a voltage signal. This voltage signal is used by circuits and controllers to excite the piezoelectric material, causing it to vibrate mechanically at the same frequency as the external force. In this way, the piezoelectric material generates ultrasonic waves through vibration, converting mechanical energy into acoustic energy.
Ultrasonic Wave Reception:
When external ultrasonic waves pass through the sensor, these waves cause mechanical vibrations in the piezoelectric material. Due to the positive piezoelectric effect, these mechanical vibrations lead to an uneven distribution of charges within the piezoelectric material, generating a voltage signal. This voltage signal represents the ultrasonic information received by the sensor.
Applications of Ultrasonic Sensors
Medical Field: Used in ultrasonic detectors, ultrasonic imaging equipment, etc.
Industrial Field: Used in material inspection, liquid level detection, displacement measurement, etc.
Automotive Field: Used in parking assistance systems, obstacle detection systems, etc.
Three Major Measurement Categories:
1. Liquid Level Measurement
• Measures the liquid level and solid level in closed or open tanks.
• Manages and monitors water levels in rivers, streams, ponds, and canals.
• Measures water levels in rivers and bodies of water to warn relevant parties of floods and tsunamis.
• Manages water usage to protect resources, enhance safety, and improve efficiency.
• Monitors fuel inventory, tracks its usage, and prevents potential theft.
• Measures the height of liquid in weirs, channels, and flumes to calculate the volumetric flow of eluents and water.
2. Distance, Range, and Size Measurement
• Measures the height and size of objects like containers and boxes.
• Calculates the diameter of paper, film, or foil rolls to detect variables such as roll tension or remaining material.
• Measures the free movement of materials as they move from one machine to another to prevent damage.
• Measures the position of objects in a closed-loop system to maintain or control their position.
3. Object Detection or Proximity Sensing
• Detects objects for counting, safety protection, inventory checks, or helps automated moving agents (such as robots) avoid obstacles.
• Detects people in a scene and determines whether they are approaching or leaving.
• Can monitor targets across the entire sensor range or restrict it to a user-defined distance range.
• Long-distance applications may involve detecting the presence or absence of objects and/or materials, as well as avoiding obstacles.
• Industrial ultrasonic sensors can detect large and small targets, including solids, liquids, and particulate materials.
• Ultrasonic sensors are not affected by optical characteristics such as color, transparency, reflectivity, or opacity. However, certain variables (including the shape, size, and orientation of the target) will affect the maximum detection range of the ultrasonic sensor.
Reference Factors for Selecting Ultrasonic Sensors
When selecting and installing ultrasonic sensors, it is important to clarify some basic conditions; otherwise, the measurement results may be directly affected.
1. Characteristics of the Measured Object: Flat Objects: Such as liquid surfaces, glass, etc; Cylindrical Objects: Such as cans, bottles, etc; Granular or Blocky Objects: Such as coal, cement, plastic granules, etc.
2. Application Environment: Consider factors such as temperature, humidity, and noise.
3. Detection Methods: Limited Distance Type (reflective type); Limited Area Type (reflective type); Through-beam Type.
4. Detection Distance: The maximum detection distance for reflective sensors is 6 meters (e.g., CSB30 series); The maximum detection distance for through-beam sensors is 100mm (e.g., CSDA series).
5. Sensor Output: Analog Output: The voltage or current output signal changes with the measured distance; Serial Data: The output data is sequentially transmitted to the designated connected device; Switch/Relay Output: The switch output is activated or deactivated at a set distance, thereby starting or stopping specific external actions or indicators based on the preset distance.
6. Sensor Shape: Cylindrical, square, cylindrical with an Elbow.
Unstable Scenarios for Ultrasonic Sensors
To ensure the stable and effective operation of ultrasonic sensors, it is recommended to consider the following situations before testing:
• The surface temperature of the target object exceeds 100°C.
• The wind speed in the detection environment exceeds 60 km/h.
• The operating environment is at an altitude above 3,000 meters.
• The pressure in a sealed environment exceeds 1.2 standard atmospheres.
• The operating environment has temperatures below -20°C or above 70°C.
• In non-reflector mode, detecting highly sound-absorbing materials such as felt, wool, cotton, or sponge foam.
• Sound waves cannot propagate in a vacuum. Therefore, ultrasonic sensors will fail in vacuum environments.
• Detecting other unknown substances or in uncertain usage scenarios.
Side Note: The Difference Between Ultrasonic Sensors and Sonar Sensors
When discussing ultrasonic sensors, sonar sensors are often brought up as well. Many people think these two types of sensors are the same, but there are actually some key differences between them.
Sonar sensors are primarily used to directly detect and identify objects in water and the contours of the seabed. A sonar sensor emits a sound wave signal that, when it encounters an object, reflects back to the sensor. The sensor then calculates the distance and position of the object based on the reflection time and waveform. Sonar sensors are typically used for biological detection, such as identifying what types of creatures are present on the seabed and their sizes. The devices you may have heard of for detecting sea monsters are sonar sensors.
Ultrasonic waves have strong penetration capabilities, especially in opaque solids, where they can penetrate to depths of several tens of meters. When ultrasonic waves encounter impurities or interfaces, they produce significant reflections that form echoes; when they encounter moving objects, they generate a Doppler effect. Ultrasonic sensors are developed based on these characteristics of ultrasonic waves.
DADISICK Popular Sensor Products
Detection range: 100-2000 mm, 200-4000 mm, 350-6000 mm
Material: copper nickel plating, plastic fittings
Connection type: 5-pin M12 connector
Detection range: 30-300 mm, 50-500 mm, 60-1000 mm
Material: copper nickel plating, plastic fittings
Connection type: 5-pin M12 connector
Response time: up to 1.5ms
Repetitive accuracy: up to 10µm
Beam spacing:10mm
Number of optical axes:70
Protection height:690mm
light curtain sensor output (OSSD):2 PNP
Safety Edges is a technology that monitors the pressure distribution on the carpet through pressure sensing.