Application of 2D LiDAR Sensors with Electric Forklifts: A High-Rack Warehouse Slot Detection Solution
- Share
- publisher
- Zoe
- Issue Time
- Sep 13,2024
Summary
In modern warehousing and logistics, improving operational efficiency and safety is key to enhancing overall performance. This solution leverages high-precision 2D LiDAR sensor technology to address the challenges faced by electric forklifts when handling goods in high-rack warehouses. By enabling fast and accurate detection of available storage slots, this technology prevents misplacement of goods, increases retrieval efficiency, and reduces risks during forklift operations.
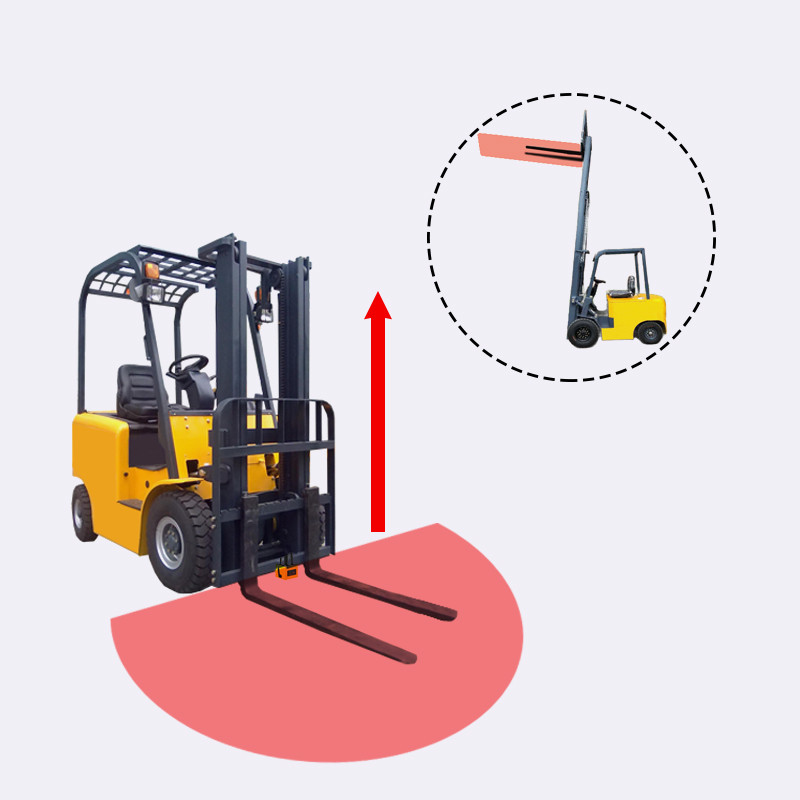
In modern warehousing and logistics, improving operational efficiency and safety is key to enhancing overall performance. This solution leverages 2D LiDAR sensor technology to address the challenges faced by electric forklifts when handling goods in high-rack warehouses. By enabling fast and accurate detection of available storage slots, this technology prevents misplacement of goods, increases retrieval efficiency, and reduces risks during forklift operations.
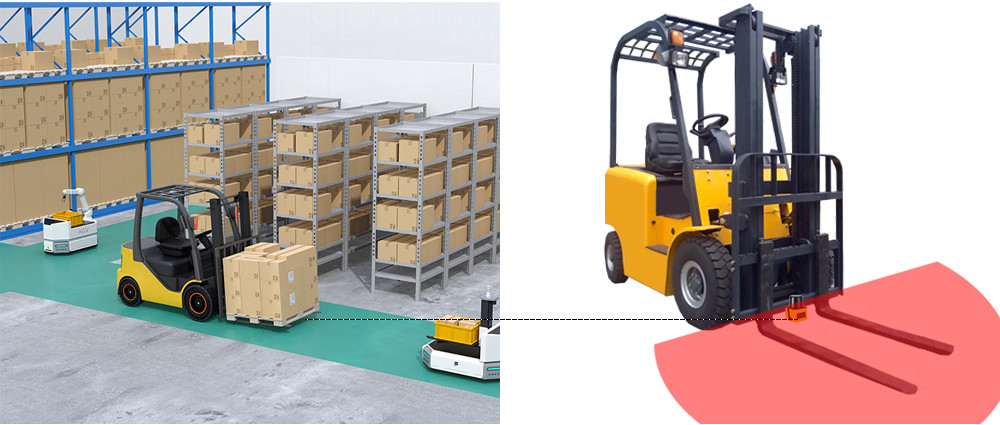
Forklift Monitoring System Components
Electric Forklift:
A standard electric forklift that handles tasks such as transporting, stacking, and loading/unloading goods.2D LiDAR Sensor:
Installed between the forklift’s two forks, responsible for real-time scanning of the state of the racks ahead.Control System:
Receives and analyzes data from the LiDAR sensor, providing feedback to the operator through an interface or alert system.Working Principle of the 2D LiDAR Sensor
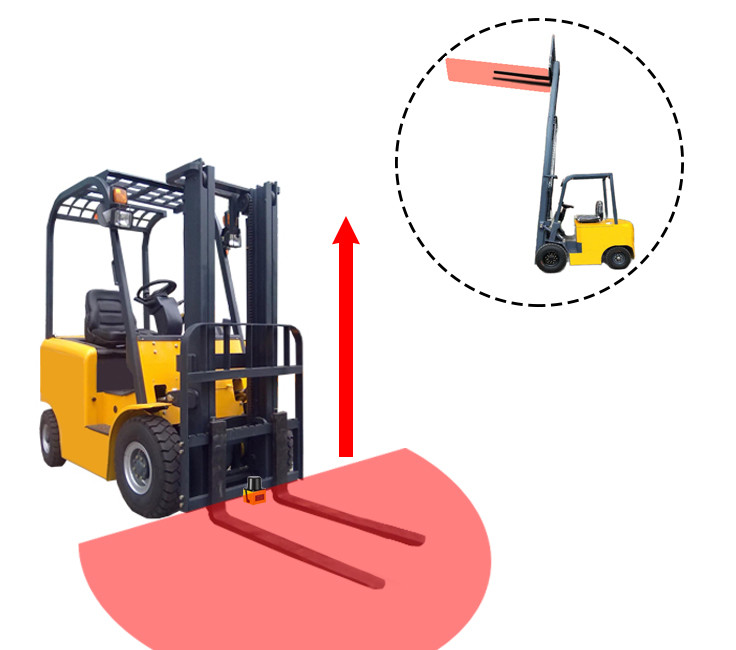
Working Principle
In high-rack warehouse operations, as the forklift's pallet is raised, the operator's line of sight becomes obstructed, particularly when the pallet reaches the upper shelves, creating a "blind spot." As shown in the image, the 2D LiDAR sensor installed between the two forks of the forklift continuously scans the area in front of the forklift, detecting the shelves and the surrounding environment.
As the pallet is lifted, the 2D LiDAR sensor continuously monitors the pre-defined alert zone to ensure there are no obstacles or incorrect storage locations. As illustrated by the red warning area in the image, if the sensor detects an object entering this zone, it immediately triggers an alarm signal. The forklift's control system then processes the signal and can take appropriate actions, such as reducing the pallet's speed or, if necessary, stopping the operation to prevent collisions.
Additionally, if the sensor detects an available storage space, the system will prompt the operator with precise placement instructions via a display screen or an audible signal, ensuring accuracy and safety. If the shelf is full, the system will issue an alert to prevent incorrect placement, thus improving operational efficiency and safety.
Implementation Steps
1️⃣ Needs Analysis: Evaluate the warehouse layout and forklift operation process to determine the best installation and configuration plan for the sensor.
2️⃣ System Configuration: Choose the appropriate 2D LiDAR sensor model and install it according to the type of electric forklift.
3️⃣ Staff Training: Train forklift operators on how to use the LiDAR system, ensuring all employees can operate it proficiently.
4️⃣ Trial Run and Optimization: Conduct a trial run in the initial phase, monitoring system performance and adjusting parameters based on real-world conditions.
5️⃣ Full Deployment and Maintenance: After ensuring the system’s stability, fully deploy it across all relevant forklifts and establish regular maintenance and calibration procedures to ensure long-term reliability.
Benefits and Technical Features of Using 2D LiDAR Sensors
✅ Efficiency Boost: Rapid and precise detection of available storage slots reduces time spent on transporting and searching, improving overall operational efficiency.
✅ Enhanced Safety: Prevents accidents or damages caused by misplacement or overloading, increasing safety during warehouse operations.
✅ Easy Integration: The 2D LiDAR sensor can be easily installed on existing electric forklifts without requiring major equipment modifications.
✅ Cost-Effectiveness: By minimizing goods damage and improving operational speed, this solution can significantly reduce long-term warehouse operating costs.
Related Sensors
Laser Source: 905 nm (Class I)
Scanning Angle Range: 270°
Scanning Frequency: 15 Hz / 30 Hz
Angular Resolution: 0.1° / 0.3°
Operating Range: 0.05 m ~ 5 m
Detection Range at 10% Object Reflectivity: 2.5 m
Self-Learning Function: Automatic environmental scanning and region generation
Recognizable Object Shapes: Almost any shape
Number of Zone Groups: 16 zone groups, each containing 3 zones
Measurement Error: ±30 mm
Housing Color: Yellow
Enclosure Protection Rating: IP65
Weight: 150 g (excluding cable)
Operating Temperature: -10°C ~ 55°C
Dimensions (L x W x H): 50 mm x 50 mm x 76 mm
20m distance, A technique that uses a laser beam to measure distance and create detailed maps of objects and environments.
Sensing range 20m, A technique that uses a laser beam to measure distance and create detailed maps of objects and environments.
Beam spacing: 80mm
Number of optical axes: 10
Protection height: 720mm
Safety Curtain outputs (OSSD):2 PNP
Detection range: 350-6000 mm
Material: copper nickel plating, plastic fittings
Connection type: 5-pin M12 connector
Output method: RS485
Response time: up to 1.5ms
Repetitive accuracy: up to 10µm
FAQs About 2D LiDAR Sensors
What Are The Functions Of 2D LiDAR Sensors?
The 2D LiDAR sensor has three main functions:
Area protection: Monitors a designated area to prevent unauthorized objects or personnel from entering, ensuring operational safety.
Path protection: Ensures that moving equipment, such as forklifts, can pass safely through pathways, preventing collisions.
Collision avoidance: Detects potential obstacles or hazardous objects, issuing timely alerts to help avoid accidents during operations.
What Are The Operating Modes Of The LD-05D Series 2D LiDAR?
Monitoring mode: This is the default operating mode of the LD-05D. When an object enters the pre-set monitoring area, the sensor will trigger an alarm through LED lights and output signals. The LD-05D will automatically enter this mode when powered on.
Editing mode: This mode allows the user to edit the monitoring areas of the LD-05D. Through the LD Designer software, users can adjust the monitoring areas and area groups, putting the sensor into editing mode.
LD-05D Software installation package.rar: https://drive.google.com/file/d/1BlVdjQALeIgMce2S8cdH6RVRJuR76bqs/view?usp=drive_link
Self-learning mode: Users can use the 2D LiDAR to scan the surrounding environment and generate work areas. In this mode, pressing and holding the “self-learning button” on the LD-05D housing will activate the self-learning mode, enabling the sensor to automatically set the monitoring areas.
Standby mode: In this mode, the LD-05D is on standby, pausing all monitoring tasks. Key characteristics of this mode include:
(1) The motor stops rotating.
(2) Point cloud data transmission is paused.
(3) Area group data can still be uploaded and downloaded.
(4) Users can switch the sensor to standby mode through input signals.
What Are “Areas” And “Area Groups”?
Area: The LD-05D monitors a user-defined specific range. When an object enters this range, the sensor triggers an alert signal. For example, a specific location on a warehouse shelf can be set as a monitoring area, allowing the system to track when goods enter or leave the area.
Area group: An area group consists of three areas: Area 1, Area 2, and Area 3. These areas can be independent or interrelated, depending on the user’s needs. For example, in a high-rack warehouse, different monitoring areas can be set for different shelf levels to simultaneously track the movement of goods at multiple levels.