How to Troubleshooting Safety Relay Failures? A Practical Guide
- Share
- Issue Time
- Sep 7,2024
Summary
A guide to troubleshooting common failures in safety relays, focusing on overhauling sensing mechanisms and actuators. Includes steps to repair coil and iron core faults, address contact overheating, wear, and welding. Tips include rewinding coils, smoothing contact surfaces, and adjusting springs for better performance.
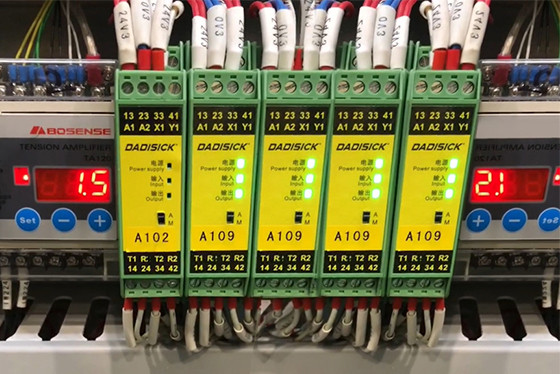
From a practical standpoint, relays function as electrical switches. Both near and far, they use low-power signals to control high-power circuits. Relays are designed to effectively isolate low-power signals from high-power circuits, often referred to as galvanic isolation. This isolation ensures safe and robust operation of the user's electrical system. Relays are versatile because they can be used to control a single circuit or multiple circuits, and they can also be used as amplifiers or circuit breakers.
Electromechanical relays have a long history and consist of contacts, an armature, a spring and an electromagnet. In its basic operation, the spring holds the armature in position. When energized, an electromagnet exerts an attraction on the armature, causing it to move and close a set of contacts, allowing current to flow through the circuit.
Today we will explain how to troubleshoot common failures when using safety relays:
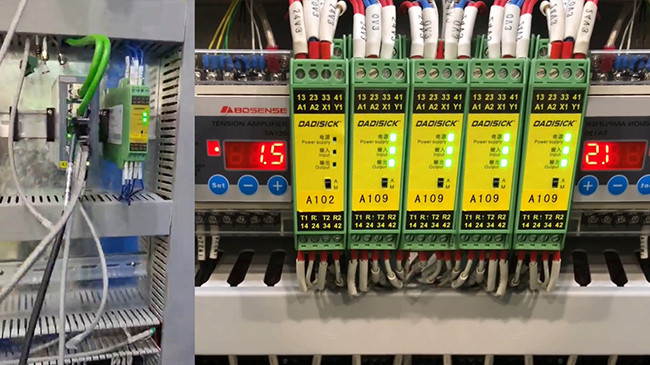
For electromagnetic (voltage, current, intermediate) relays, the sensing mechanism is known as the electromagnetic system. The faults of the electromagnetic system are mainly concentrated in the coil and the moving and static iron core parts. Commonly encountered faults and overhaul methods are as follows:
1. Coil fault repair
Coil failure usually coil insulation damage caused by mechanical injury to the formation of turn-to-turn short circuit or ground; due to the supply voltage is too low, dynamic and static iron core contact is not tight, so the current through the coil is too large, the coil is hot and burnt. The coil should be rewound. When the coil is energized, the armature does not attract, it may be disconnected from the coil lead wire connection so that the circuit is interrupted. This problem can be solved by welding the disconnected point.
2. Iron core fault repair
Iron core failure is mainly energized armature can not be sucked. This may be due to the coil wire breakage, a foreign body between the static iron core, low power supply voltage and so on. Repair should be differentiated. When the noise of the armature is loud after energization. It is caused by the dynamic and static iron core contact surface is uneven, or oil contamination. When repairing, the coil should be removed, the contact surface should be filed or smoothed; and it should be cleaned if there is oil contamination.
Most relay actuators are contact systems. Through its "on" and "off" to complete certain control functions. Contact system failures generally include contact overheating, wear, welding and so on.
1. Contact overheat is mainly caused by insufficient power, insufficient contact pressure, oxidation, dirt, etc.
2. Insufficient contact capacity, high arc temperature oxidizing the contact metal, etc. are the main causes of contact wear.
4. The main reason for contact welding is the high arc temperature or severe contact jump.
The sequence of contact maintenance is as follows:
1. Open the cover and check the contact surface.
2. If the contact surface is oxidized, the silver contacts can be repaired and the copper contacts can be smoothed with a smooth file or the oxide layer can be scraped off gently with a knife.
3. If the contact surface is dirty, it can be cleaned with gasoline or carbon tetrachloride.
4. If there are burn marks on the contact surface, the silver contacts can be repaired and the copper contacts can be repaired with an oil file or knife. Do not use sandpaper for repair to avoid residual sand particles causing poor contact.
5. Contacts should be replaced if they are welded. If the contact capacity is too small, replace the relay with one with a larger capacity.
6. Adjust or replace the spring to increase the pressure if the contact pressure is insufficient. If the pressure is still insufficient, replace the contacts.