Hydraulic Cylinder Work Area Monitoring and Obstacle Avoidance Solution
- Share
- publisher
- Zoe
- Issue Time
- Feb 14,2025
Summary
The DADISICK LD-05D Series 2D LiDAR provides an efficient and reliable solution for hydraulic cylinder work area monitoring and obstacle avoidance.
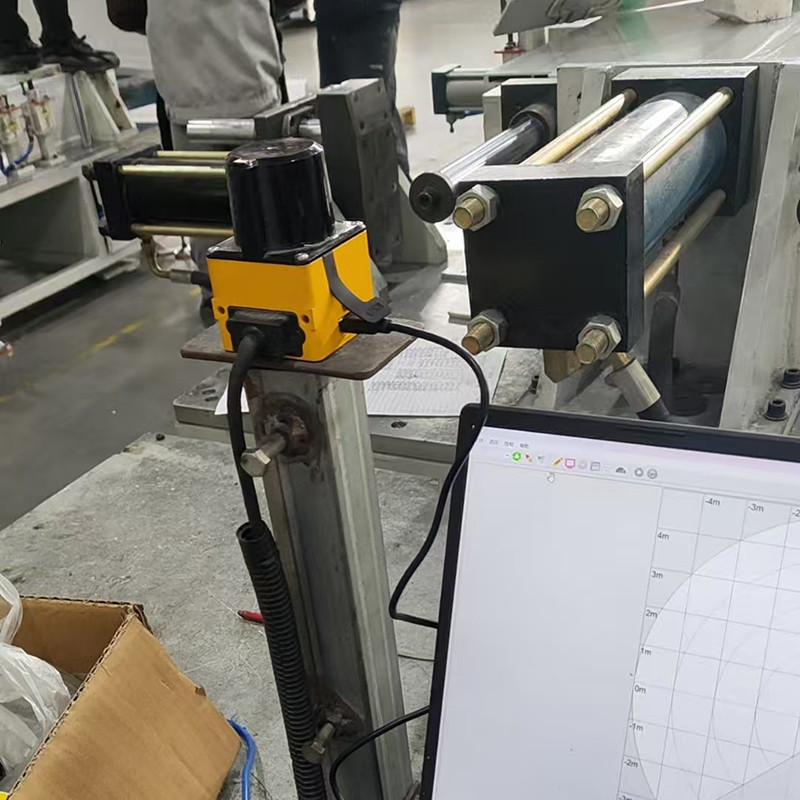
Hydraulic Cylinder Work Area Monitoring and Obstacle Avoidance Solution
A hydraulic cylinder is a device that converts hydraulic energy into mechanical energy, primarily used for generating linear motion or force. However, during operation, the extension and retraction of the piston rod can lead to collision accidents, especially when personnel or obstacles are present in the vicinity.
To address this issue, DADISICK’s LD-05D Series 2D LiDAR provides an efficient and reliable solution for area monitoring and obstacle avoidance, ensuring safe equipment operation and minimizing accident risks.
Working Principle of 2D LiDAR
The LD-05D Series 2D LiDAR utilizes the Time of Flight (TOF) principle, emitting laser pulses and measuring the time for the reflected light to return, accurately calculating the distance to the target object. With its high precision, high resolution, and high scanning frequency, it enables real-time monitoring of the surrounding environment and precise obstacle detection.
Area Monitoring & Alarm Function
The LD-05D Series 2D LiDAR supports precise monitoring area configuration with multiple zone groups and monitoring points to ensure real-time detection around hydraulic cylinders.
▪️Flexible Zone Configuration: Supports up to 16 zone groups, each containing 3 sub-zones, allowing customized monitoring and alarm areas.
▪️Real-time Alarms: When an object enters the predefined danger zone, the LiDAR instantly detects it and triggers an alarm signal, notifying the control system to take necessary action.
Obstacle Avoidance Mechanism
Upon detecting an obstacle, the LD-05D Series 2D LiDAR converts the detection data into switching signals, which are then transmitted to the controller. Based on these signals, along with the motion status and preset path of the hydraulic cylinder, the system can:
✅ Immediately stop the hydraulic cylinder’s movement
✅ Adjust movement direction to avoid collisions
This intelligent obstacle avoidance mechanism effectively prevents accidents, reduces equipment damage, and enhances workplace safety.
System Integration & Key Advantages
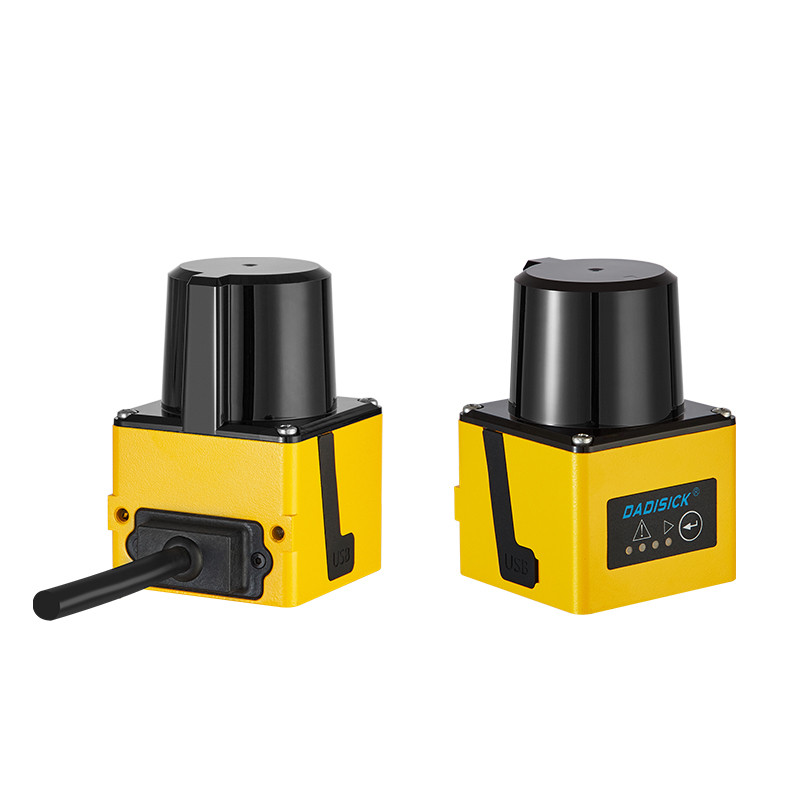
LD-05D Series 5 m Obstacle Avoidance 2D LiDAR
✔ High Accuracy & Reliability
▪️Measurement accuracy: ±3 cm (typical)
▪️Angular resolution: 0.1° / 0.3°
▪️Scanning frequency: 15 Hz / 30 Hz
▪️Ensures precise monitoring and reliable obstacle avoidance
✔ Fast Response Time
▪️Typical response time: 134 ms (adjustable range: 67 ms ~ 30,000 ms)
▪️High-speed communication: Micro USB interface for real-time data transmission
✔ Easy Integration
▪️Compact design: Dimensions 50 mm × 50 mm × 76 mm
▪️Lightweight: 150 g (excluding cable)
▪️Plug-and-play installation: Easily mounted around hydraulic cylinders with no need for large-scale modifications
Real-World Application Case
In an automated production line of a mechanical manufacturing company, hydraulic cylinders drive robotic arms for precision assembly. Since operators work in close proximity to these machines, safety risks are high.
To mitigate this risk, the company installed the LD-05D Series 2D LiDAR at the exit area of the hydraulic-driven equipment to continuously monitor the working zone. When personnel or obstacles enter the danger area, the LiDAR immediately triggers an alarm and stops equipment operation.
Application Results:
✅ Reduced safety incidents by over 70%
✅ Prevented production losses caused by equipment collisions
✅ Enhanced automation safety in the production line
Tips:
If you have purchased the LD-05D radar, you should receive the following accessories
LD-05D Radar × 1
USB Data Cable × 1
Radar Connection and Debugging Steps:
1️⃣ Connect the Power Supply: Follow the instructions in the "Electrical Connection" section of the user manual to properly connect the power supply.
2️⃣ Connect to a Computer: Use the USB data cable to connect the radar to a computer.
3️⃣ Launch the Software: Run LD View software and establish a connection with the radar.
4️⃣ Check Point Cloud Data: Monitor the radar’s point cloud output and debug the alarm function.
5️⃣ Set Up the Monitoring Area: Configure the monitoring area groups and download the settings to the radar.
6️⃣ Prepare for Installation: Once the setup is complete, install the radar in the designated location.
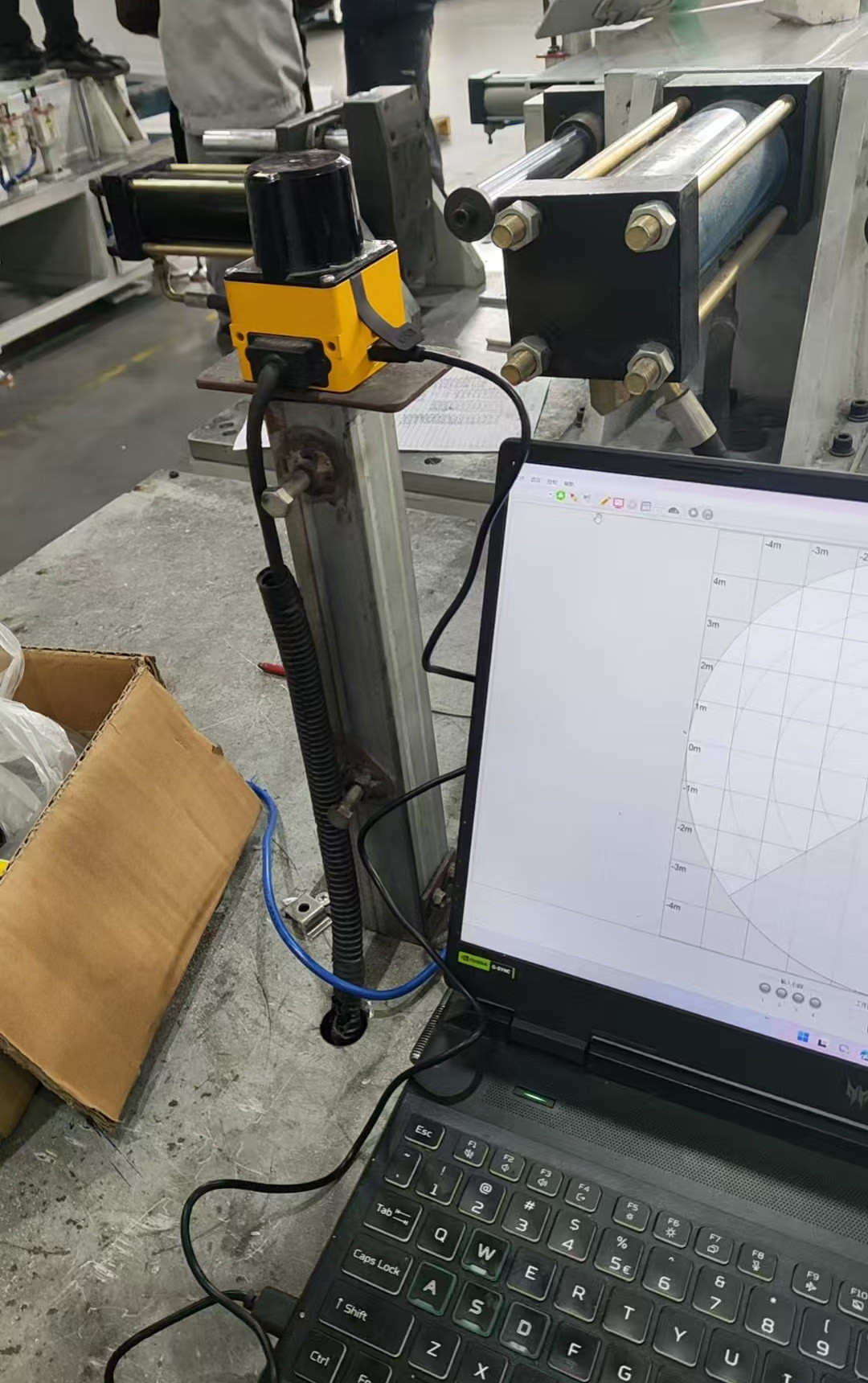
Related Safety Products
5m distance, A technique that uses a laser beam to measure distance and create detailed maps of objects and environments.
20m distance, A technique that uses a laser beam to measure distance and create detailed maps of objects and environments.
Sensing range 20m, A technique that uses a laser beam to measure distance and create detailed maps of objects and environments.
Economic Laser Scanning Radar sensing range 5m-10m