Solution for 2D LiDAR Sensors in Overflow Control and Part Counting for Material Bins
- Share
- publisher
- Zoe
- Issue Time
- Sep 12,2024
Summary
By installing 2D LiDAR sensors at the end of the conveyor, real-time monitoring of material height, distribution, and part count in the material bin can be achieved. These sensors use laser scanning technology to detect overflow and trigger alarms or automatically stop the conveyor when the material exceeds preset thresholds, ensuring safety during production. Additionally, LiDAR sensors can precisely count parts in the bin, preventing issues caused by part shortages or excess during production.
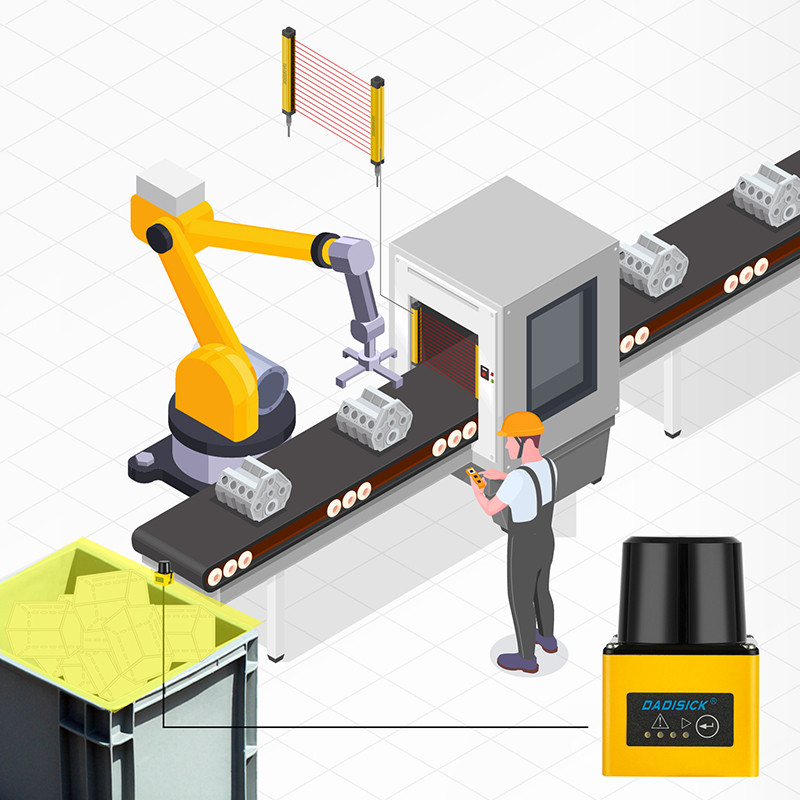
By installing 2D LiDAR sensors at the end of the conveyor, real-time monitoring of material height, distribution, and part count in the material bin can be achieved. These sensors use laser scanning technology to detect overflow and trigger alarms or automatically stop the conveyor when the material exceeds preset thresholds, ensuring safety during production. Additionally, LiDAR sensors can precisely count parts in the bin, preventing issues caused by part shortages or excess during production. This solution improves production efficiency, accuracy, and safety through automated control and high-precision monitoring, while reducing material waste and manual intervention.
The Role of 2D LiDAR in Overflow Control
Monitoring Mechanism:
When materials are conveyed to the end and dropped into the bin, the 2D LiDAR sensor activates immediately, emitting laser beams and receiving the reflected signals to monitor the material’s height and distribution. The LiDAR’s scanning range covers the entire top layer of the material bin, providing comprehensive monitoring of material height.
Overflow Detection:
If the material height in the bin exceeds the preset safety threshold, the LiDAR sensor quickly identifies the overflow condition. The system then triggers a warning signal, prompting operator intervention or automatically stopping the conveyor to prevent further overflow. This real-time response mechanism significantly reduces material waste and enhances workplace safety.
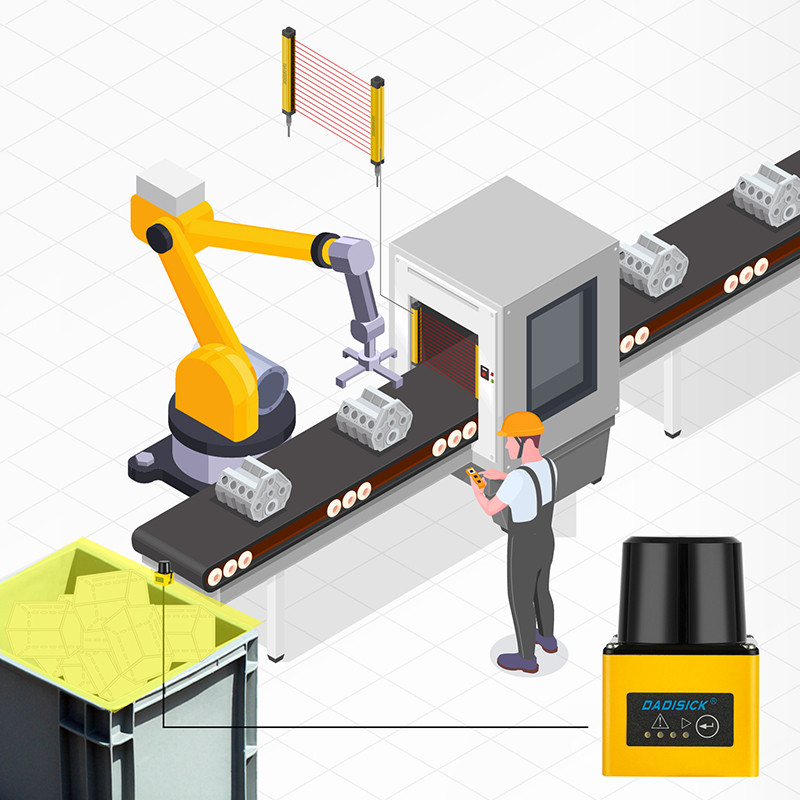
How 2D LiDAR Achieves Part Counting and Monitoring
Counting Function:
In addition to monitoring material height, the 2D LiDAR sensor can accurately scan the shapes of objects in the bin and, using image processing technology, count the parts. This is crucial for ensuring the correct number of parts in each material bin, avoiding problems caused by shortages or excess during production.
Application Scenarios:
This function is especially useful for production lines and warehouse management systems where part quantities are strictly regulated. LiDAR technology can quickly capture and count large quantities of parts, reducing manual intervention and improving efficiency and accuracy.
System Integration and Intelligent Control
Automated Integration:
LiDAR sensors can be easily integrated into existing industrial control systems, enabling coordinated operations with conveyors, alarm systems, and other devices. When the sensor detects overflow or abnormal part quantities, the system can automatically take actions such as stopping the conveyor, issuing alerts, or sending adjustment commands to upstream equipment.
Remote Monitoring and Data Analysis:
By connecting LiDAR scan data to a central management system, operators can remotely monitor the status of the material bins while receiving real-time data for overflow trend forecasting or part inventory management. This provides strong support for production line optimization and decision-making.
Benefits of Using 2D LiDAR Sensors as a Solution
✅ High Precision Monitoring: 2D LiDAR sensors provide millimeter-level accuracy, ensuring precise monitoring of material height and part count.
✅ Real-time and Automated: The automated response mechanism quickly addresses overflow and counting errors, reducing manual intervention and operational delays.
✅ Cost Efficiency: Minimizes material waste and prevents production line stoppages due to part shortages or overflows, lowering operational costs.
✅ Enhanced Safety: Timely control and detection of overflows ensure safe production processes and reduce potential accident risks.
LD-05D Series 2D LiDAR Sensor – An Efficient Monitoring Solution
Laser Source: 905 nm (Class I)
Scanning Angle Range: 270°
Scanning Frequency: 15 Hz / 30 Hz
Angular Resolution: 0.1° / 0.3°
Operating Range: 0.05 m ~ 5 m
Detection Range at 10% Object Reflectivity: 2.5 m
Self-Learning Function: Automatic environmental scanning and region generation
Recognizable Object Shapes: Almost any shape
Number of Zone Groups: 16 zone groups, each containing 3 zones
Measurement Error: ±30 mm
Housing Color: Yellow
Enclosure Protection Rating: IP65
Weight: 150 g (excluding cable)
Operating Temperature: -10°C ~ 55°C
Dimensions (L x W x H): 50 mm x 50 mm x 76 mm
Related Safety Sensors
20m distance, A technique that uses a laser beam to measure distance and create detailed maps of objects and environments.
Sensing range 20m, A technique that uses a laser beam to measure distance and create detailed maps of objects and environments.
The LD-50G model belongs to the 2D single-line lidar. Based on the DTOF ranging principle.
Beam spacing: 10mm
Number of optical axes: 200
Protection height: 1990mm
FAQs About 2D LiDAR
What Is The Difference Between 2D LiDAR And 3D LiDAR?
2D LiDAR: Scans in a single plane to generate a two-dimensional image, primarily used for monitoring the height, distance, and position of objects. 2D LiDAR is ideal for simpler detection tasks like measuring object height on a flat surface or detecting obstacles in surrounding environments.
3D LiDAR: Generates a three-dimensional image by using multiple layers or combining vertical and horizontal scans, capturing the shape and depth information of objects. It is used for more complex applications such as autonomous driving, 3D modeling, and full environment sensing.
What Are The Advantages Of 2D LiDAR Compared To 3D LiDAR?
Lower cost: 2D LiDAR has lower manufacturing and deployment costs, making it suitable for budget-constrained applications that do not require 3D information.
Easier integration: Due to simpler data processing, 2D LiDAR is easier to integrate into existing automation systems and is ideal for basic monitoring tasks.
Lower power consumption: 2D LiDAR consumes less power compared to 3D LiDAR, making it suitable for systems with energy efficiency requirements.
Compliant with Eye Safety Standards: Most 2D LiDAR sensors use Class 1 lasers, which comply with the International Electrotechnical Commission (IEC) eye safety standards. This means they will not cause harm to human eyes during operation.
How Does 2D LiDAR Work?
2D LiDAR works by emitting laser beams and receiving the reflected signals. The sensor emits a laser beam that scans across the target area. When the beam hits an object, it reflects back to the sensor, and the system calculates the distance between the object and the sensor based on the return time (time-of-flight). This scanning is performed along a horizontal plane, creating a two-dimensional point cloud that shows the distance and distribution of objects in that plane.
What Are The Application Scenarios Of 2D LiDAR?
Industrial automation: Widely used for monitoring overflow in material bins and counting parts, ensuring safety and efficiency on production lines.
Warehousing and logistics: Used for obstacle detection, path planning, and inventory monitoring, optimizing warehouse operations.
Safety systems: In automatic doors, access control, and perimeter security, 2D LiDAR detects the movement of people and objects.
Service robots: Used for navigation, obstacle avoidance, and localization, helping robots operate safely in complex environments.