Solutions for Controlling Production Costs of Lithium-ion Batteries: Laser Displacement Sensors for Measuring Electrode Thickness
- Share
- publisher
- Zoe
- Issue Time
- Sep 29,2024
Summary
This article provides an overview of the impact of electrode layer count on lithium-ion battery performance and proposes a solution for measuring the thickness of lithium-ion battery electrodes using laser displacement sensors.
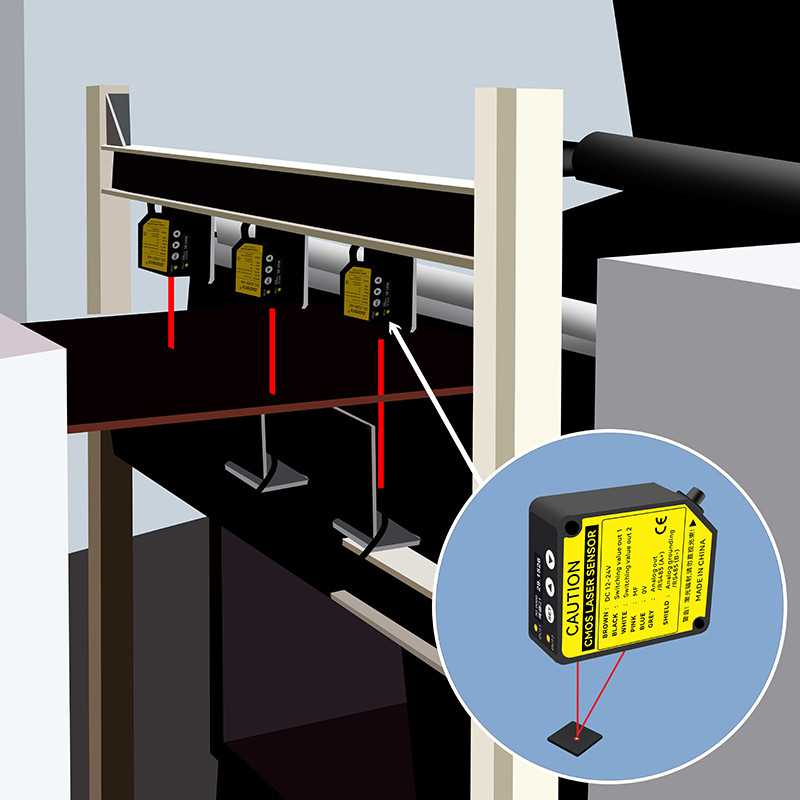
As the emphasis on and demand for renewable energy continue to rise, lithium-ion batteries have become a primary technology for applications such as electric vehicles, mobile devices, and energy storage systems. However, the performance and efficiency of lithium-ion batteries are influenced by various factors, among which the number of electrode layers is significant.

Impact of Electrode Layer Count on Lithium-Ion Battery Performance
Electrodes are key components of lithium-ion batteries, responsible for storing and releasing charge. In lithium-ion batteries, the number of electrode layers indicates the layers between the positive and negative electrodes. Generally, a higher number of electrode layers leads to increased battery capacity and longer maintenance time, as well as higher voltage and power. However, in practical applications, increasing the number of layers does not always represent the best strategy for improving battery performance.
While a greater number of layers can enhance battery capacity and energy density, it also increases the internal resistance, affecting the charging and discharging rates, leading to higher temperatures and reduced battery lifespan, while simultaneously raising costs. Therefore, selecting an appropriate number of electrode layers and implementing a reasonable battery design are crucial.
Through the design and optimization of electrode layers, it is possible to maximize the performance of lithium-ion batteries, achieving goals of low cost, long cycle life, and high efficiency. This is particularly important for applications requiring high energy density, such as mobile devices and electric vehicles, where precise control of electrode design and layering is paramount.
In summary, the number of electrode layers is one of the critical factors affecting lithium-ion battery performance. Battery designers need to consider a variety of trade-offs to select the most suitable layer count and further optimize battery performance. This presents a challenge that must be addressed in the development and application promotion of battery technology.
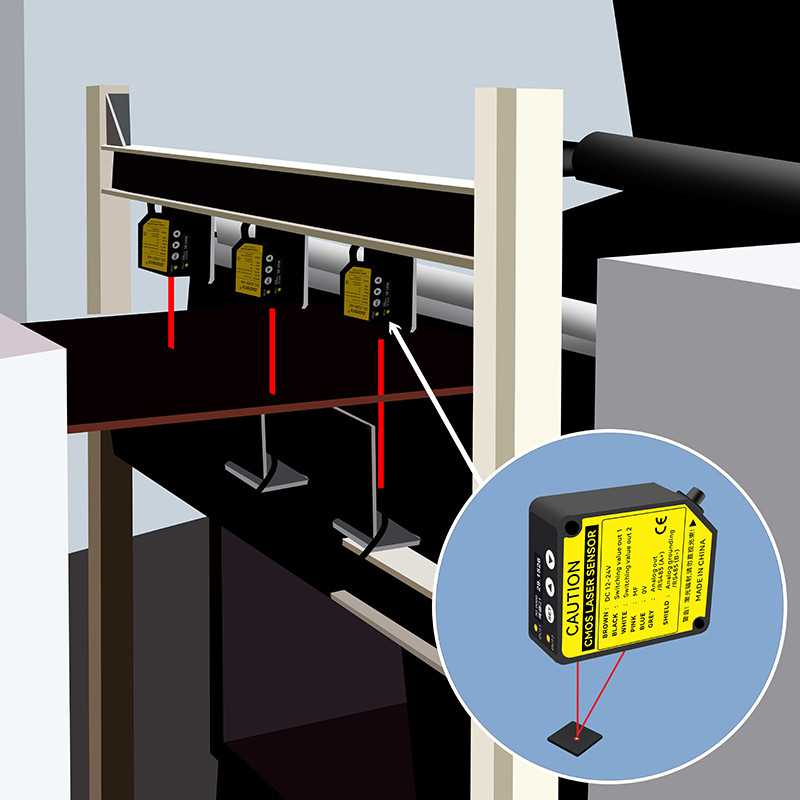
Overview of Lithium Battery Production Process
Once the raw materials for lithium batteries have passed inspection, they enter the coating process. The uniformity and edge distance of the slurry application undergo rigorous testing. After drying, the aluminum foil substrate for the positive electrode is coated on both sides and then enters the "cell assembly" stage, where the lithium polymer-coated substrate is cut into small pieces according to the size of the battery. These small pieces, consisting of positive and negative electrodes, are wrapped together with insulating materials, and after welding the tabs and completing the aluminum-plastic packaging, they undergo X-ray inspection for quality assurance. If any abnormal layering occurs, the battery may experience swelling or short-circuiting during later use. Finally, after a high-temperature bake to remove moisture, the electrolyte is injected, and the internal dryness of the battery determines its quality, resulting in the completion of the finished battery cell.
A more detailed summary of the lithium battery production process includes: material preparation, coating, rolling, cutting, stacking, welding tabs, packaging, drying, liquid injection, formation, and sorting.
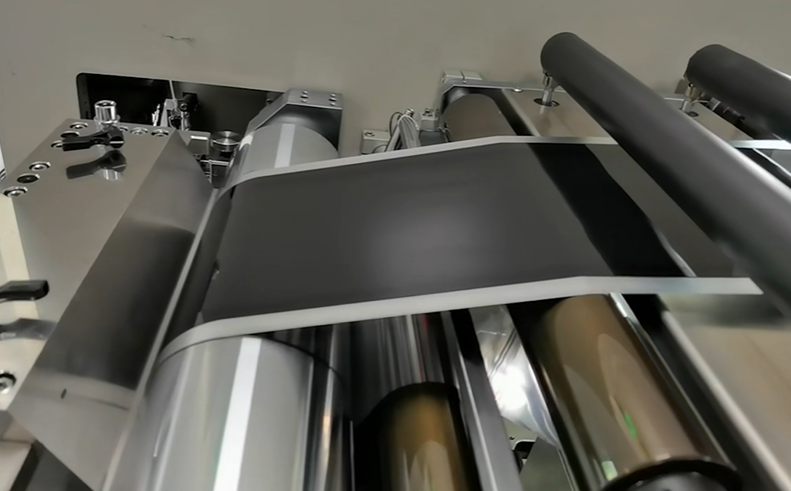
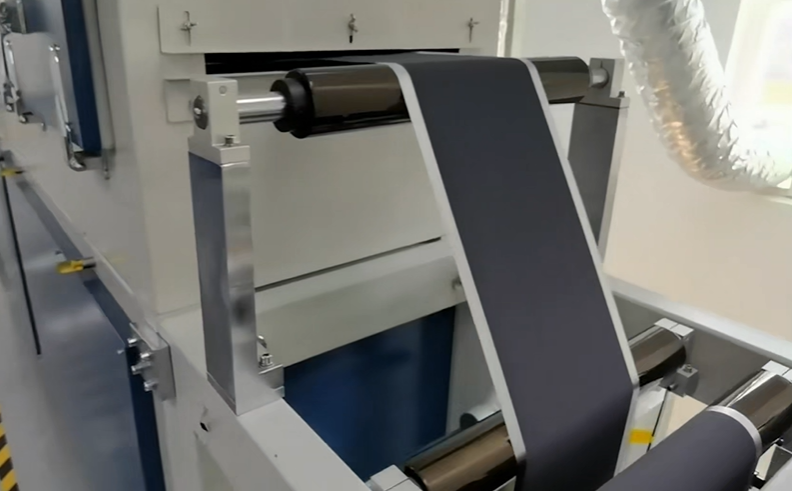
Laser Displacement Sensors for Measuring Electrode Thickness in Lithium Batteries
The coating thickness of electrodes directly relates to the battery's power generation efficiency and effective cost control. Below, we explain how DADISICK laser displacement sensors can measure the thickness of battery electrodes.
Laser displacement sensors are commonly used non-contact measurement tools that accurately measure the distance between an object and the sensor by emitting a laser beam and analyzing the time or phase difference of the reflected light. When measuring the thickness of a workpiece, triangulation methods are typically employed. (Click to learn more about laser measurement methods.)
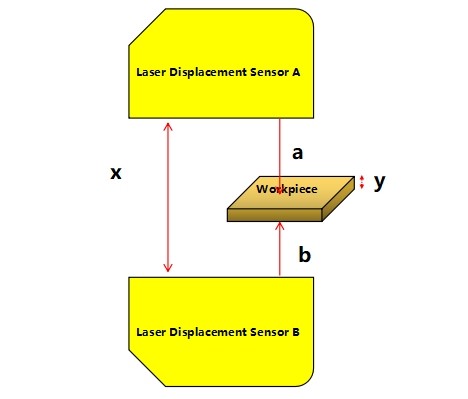
The Formula For Calculating Workpiece Thickness Is: y = x − a − b
Where:
x is the fixed distance between the two laser displacement sensors;
a is the distance from sensor A to the electrode surface;
b is the distance from sensor B to the electrode surface;
y is the thickness of the battery electrode.
After installing the two laser displacement sensors, the fixed distance x is set, and the workpiece is placed within the measurement range of the two sensors. Sensors A and B measure their distances a and b to the workpiece surface, respectively. By using the formula y = x − a − b, the thickness of the workpiece y can be calculated. It is worth noting that minor horizontal displacement of the workpiece does not affect the thickness y.
Additionally, since laser displacement sensors typically do not output direct distance values but rather analog signals proportional to the distance, a PLC (Programmable Logic Controller) is needed to read the output signals from the sensors. Through corresponding calibration and calculations, the signals are converted into actual distance values, enabling thickness measurement.
Advantages of Using Laser Displacement Sensors for Measuring Electrode Thickness in Lithium Batteries
✅ Non-Contact Measurement: Does not cause any physical damage to the measurement object.
✅ High Precision: Measurement accuracy can reach the micron level. For example, the repeatability of DADISICK's GFL-Z series laser displacement sensors can reach 10 microns, while the resolution of the GFL-G series can be as high as 2 microns.
✅ Fast Measurement: Measurement speed is quick, meeting the demands of efficient production.
Recommended Laser Displacement Sensors
Sensing Distance
|
Resolution
|
Linearity |
Output
|
30 mm (±4)
|
2 µm
|
±0.1%f.s. (f.s.=8mm) |
NPN / PNP
Analog RS485 |
50 mm (±10)
|
5 µm
|
±0.1%f.5. (f.s.=20mm) |
|
85 mm (±20)
|
10 µm
|
±0.1%f.8.(f.s.=40mm) | |
120 mm (±60) | 30 µm | ±0.1%f.s.(f.s.=120mm) | |
250 mm (±150) | 75 µm | ±0.3%f.s.(f.s.=300nm) |
Sensing Distance
|
Repeatability
|
Linearity |
Output
|
30 mm (±5)
|
10 µm
|
±0.1%F.S. |
Analog / RS485
|
50 mm (±15)
|
30 µm
|
NPN / Analog / RS485
|
|
100 mm (±35)
|
70 µm
|
||
200 mm (±80) | 200 µm | ±0.2%F.S. | |
400 mm (±200) | 400 µm / 800 µm |
Related Photoelectric Sensors
Measuring frequency: 1Hz-40Hz
Communication interface: RS232/RS485 (switchable)
Measuring distance: 0.2-100m
Measurement resolution: 1mm
Output method: NPN/PNP+analog+RS485
Resolution: 1mm
Laser type: red semiconductor laser Class II laser 655+10nm<1m
Reaction time: 50-200ms
5m distance, A technique that uses a laser beam to measure distance and create detailed maps of objects and environments.
Beam spacing: 40mm<br>
Number of optical axes: 72<br>
Protection height: 2840mm<br>
Laser curtain sensor outputs (OSSD)2 PNP