The Core Role of Safety Laser Scanners in AGV, AMR, and RGV: Unlocking the Potential of Obstacle Avoidance, Navigation, and Environmental Perception
- Share
- publisher
- Zoe
- Issue Time
- Sep 26,2024
Summary
Safety laser scanner technology plays an increasingly vital role in the field of automated logistics. By providing high-precision environmental perception and real-time data processing, safety laser scanner supports AGV (Automated Guided Vehicle), AMR (Autonomous Mobile Robot), and RGV (Rail Guided Vehicle), enhancing the efficiency and safety of material handling.
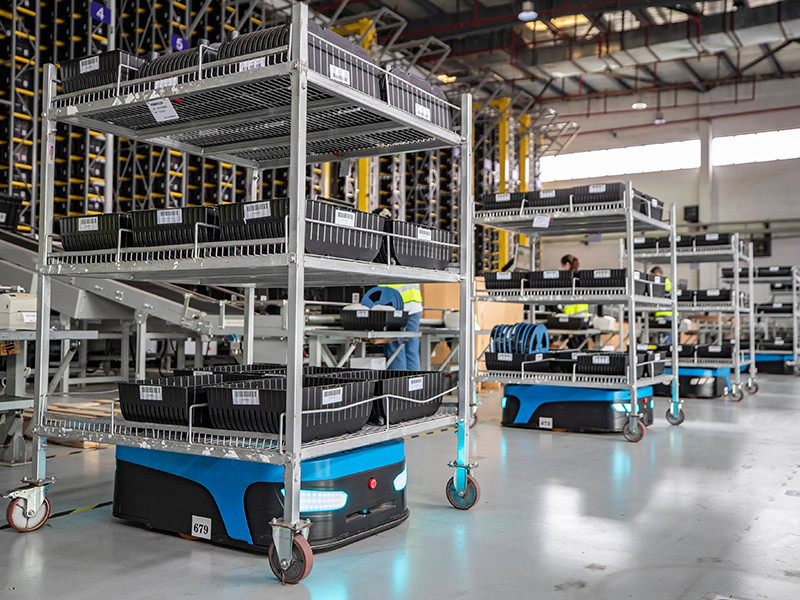
Safety laser scanner technology plays an increasingly vital role in the field of automated logistics. By providing high-precision environmental perception and real-time data processing, safety laser scanner supports AGV (Automated Guided Vehicle), AMR (Autonomous Mobile Robot), and RGV (Rail Guided Vehicle), enhancing the efficiency and safety of material handling.
Application of Safety Laser Scanner in AGV Forklift
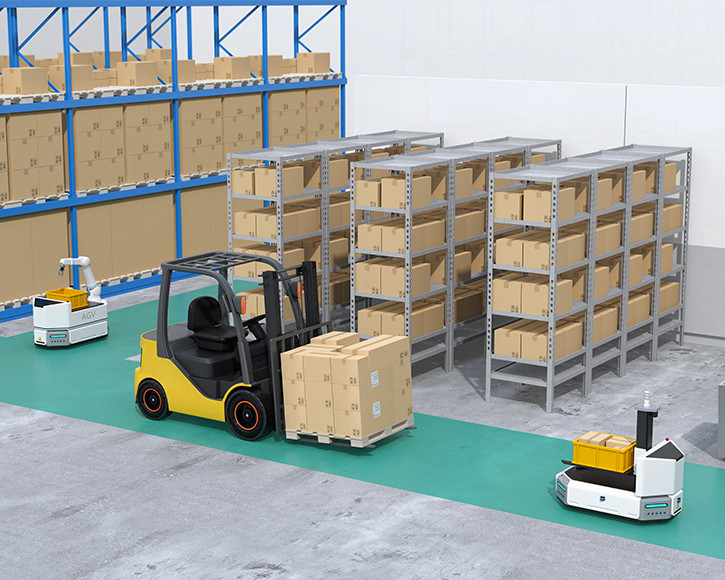
Safety Laser Scanner in AGV Forklift
AGV forklift utilizes safety laser scanner for environmental scanning and path navigation. The laser scanner measures distances to obstacles in real-time, helping the AGV accurately position itself along predetermined paths and effectively avoid obstacles. In stable environments, such as the internal transport of goods within warehouses, the use of safety laser scanner significantly increases the operational efficiency and safety of the AGV, enabling it to perform material handling tasks at high frequency.
Customer Case: Successful Application of Safety Laser Scanner in AGV Forklift
In a large warehousing enterprise, the customer integrated our safety laser scanner into their AGV forklift to enhance material handling efficiency. The real-time environmental perception capabilities of the safety laser scanner enabled the AGV to quickly identify surrounding obstacles and autonomously adjust its path, facilitating efficient and safe transportation of goods in a busy warehouse environment. This technology upgrade resulted in a 25% increase in handling efficiency and significantly reduced downtime caused by collisions, demonstrating the critical value of safety laser scanners in automated logistics.
✅ Laser Source: 905 nm (Class I)
✅ Scanning Angle Range: 300°
✅ Scanning Frequency: 25 Hz
✅ Angular Resolution: 0.5°
✅ Operating Range: 0.05 m ~ 20 m
✅ Detection Range at 10% Object Reflectivity: 15 m
✅ Self-Learning Function: Automatic environmental scanning and region generation
✅ Recognizable Object Shapes: Almost any shape
✅ Number of Zone Groups: 16 customizable preset area groups support background contour self-learning
✅ Measurement Error: System error ± 2 cm; Statistical error ± 1 cm
✅ Enclosure Protection Rating: IP67
✅ Weight: 0.6 kg
✅ Operating Temperature: -25°C ~ 50°C
✅ Dimensions (L x W x H): 80 mm x 85 mm x 102 mm
Application of Safety Laser Scanner in AMR (Autonomous Mobile Robot)
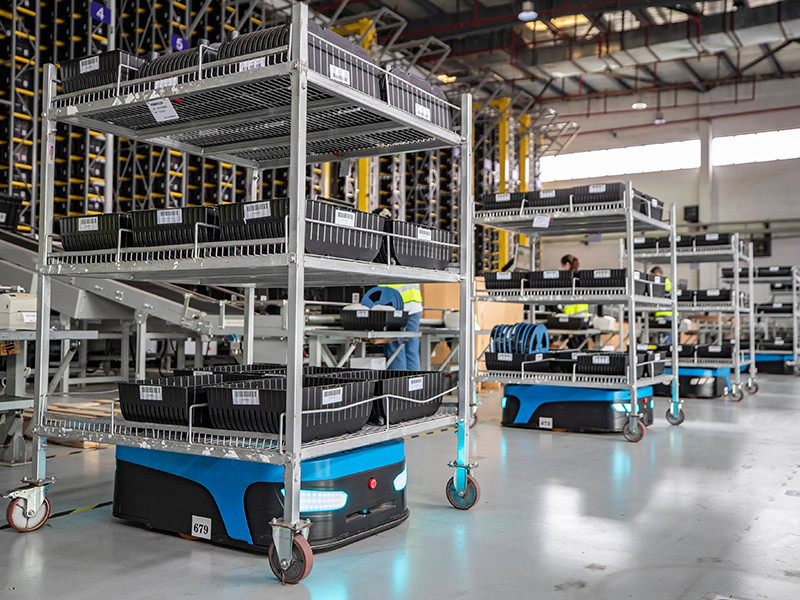
Safety Laser Scanner in AMR
In contrast to AGVs, AMR employs safety laser scanner for autonomous navigation and dynamic path planning. The safety laser scanner provides real-time environmental perception, enabling the AMR to recognize and adapt to complex and dynamic work scenarios. This flexibility and autonomy allow the AMR to excel in variable environments like production workshops and distribution centers, effectively responding to obstacles and adjusting its travel path.
In Simple Terms:
▪️ AGV (Automated Guided Vehicle): Operates efficiently in unmanned areas and is suitable for item sorting.
▪️ AMR (Autonomous Mobile Robot): Efficiently navigates between machinery and human operations, suitable for handling pallets, cases, and trolleys in internal logistics.
Application of Safety Laser Scanner in RGV (Rail Guided Vehicle)
Safety Laser Scanner in RGV
Although the RGV typically follows a fixed track or rail system, the safety laser scanner still plays a vital role in its operation. This scanner can be mounted on the RGV itself or strategically positioned along the track to monitor the environment and detect potential hazards. By continuously scanning the area around the RGV, the scanner can alert the system to any obstacles or people that may have inadvertently entered the RGV's path. This information is crucial for emergency stopping and collision avoidance, even in a guided system. Furthermore, the scanner's environmental perception capabilities enhance the overall safety of the RGV's operation, ensuring that it operates within safe parameters and does not cause harm to personnel or equipment.
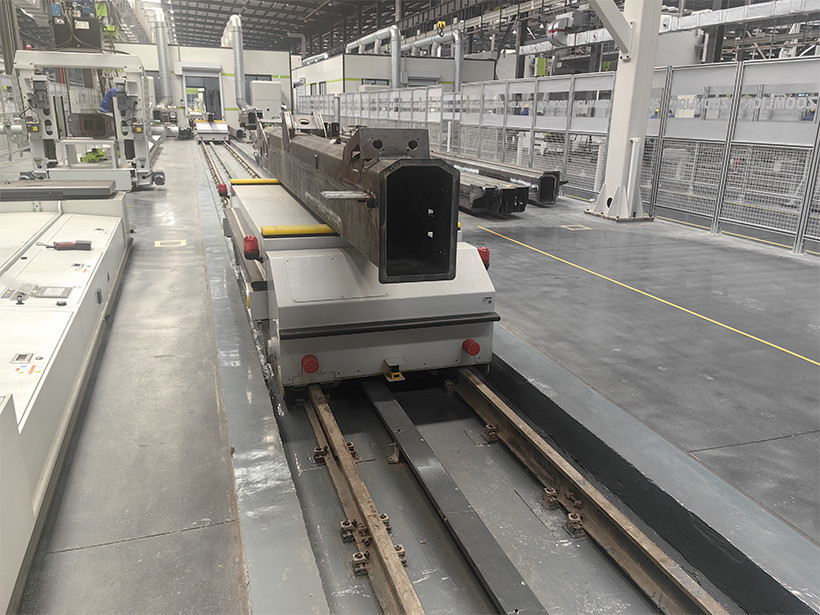
Customer Case: Successful Application of Safety Laser Scanner in Container Handling RGV
In a port logistics company, the customer applied our 2D safety laser scanner to their container handling RGV system. The high-precision positioning and real-time obstacle avoidance capabilities of the safety laser scanner enabled the RGV to quickly and safely transport heavy containers in the complex port environment. This technology integration resulted in a 30% increase in handling efficiency and effectively reduced the risk of accidents caused by obstacles, further optimizing the container operation process and enhancing overall logistics efficiency.
✅ Laser Source: 905 nm (Class I)
✅ Scanning Angle Range: 270°
✅ Scanning Frequency: 15 Hz / 30 Hz
✅ Angular Resolution: 0.1° / 0.3°
✅ Operating Range: 0.05 m ~ 5 m
✅ Detection Range at 10% Object Reflectivity: 2.5 m
✅ Self-Learning Function: Automatic environmental scanning and region generation
✅ Recognizable Object Shapes: Almost any shape
✅ Number of Zone Groups: 16 zone groups, each containing 3 zones
✅ Measurement Error: ±30 mm
✅ Housing Color: Yellow
✅ Enclosure Protection Rating: IP65
✅ Weight: 150 g (excluding cable)
✅ Operating Temperature: -10°C ~ 55°C
✅ Dimensions (L x W x H): 50 mm x 50 mm x 76 mm