What is the Principle of Safety Relay? Fundamentals, Design, and Workflow of Safety Relays
- Share
- Issue Time
- Sep 6,2024
Summary
Safety relays are essential for reliability and safety in industrial automation, machinery and power systems. They detect abnormal conditions, prevent damage/injury. Dual-channel signaling & forcibly guided contacts increase reliability. Equipped with logic controllers, they monitor signals, make decisions, control equipment & protect against failures. Workflow includes signal reception, logic decision, output control, action execution & fault protection.
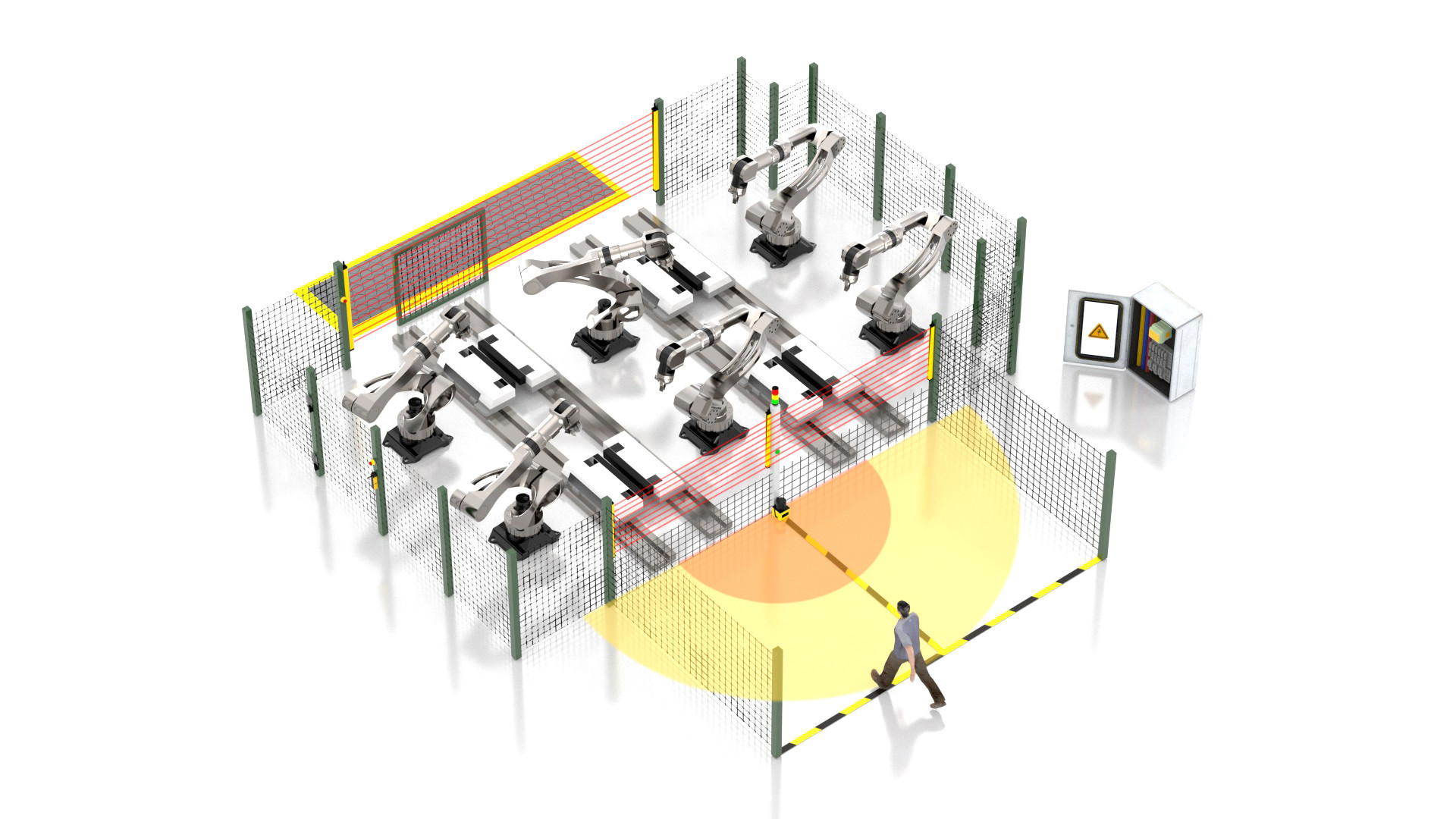
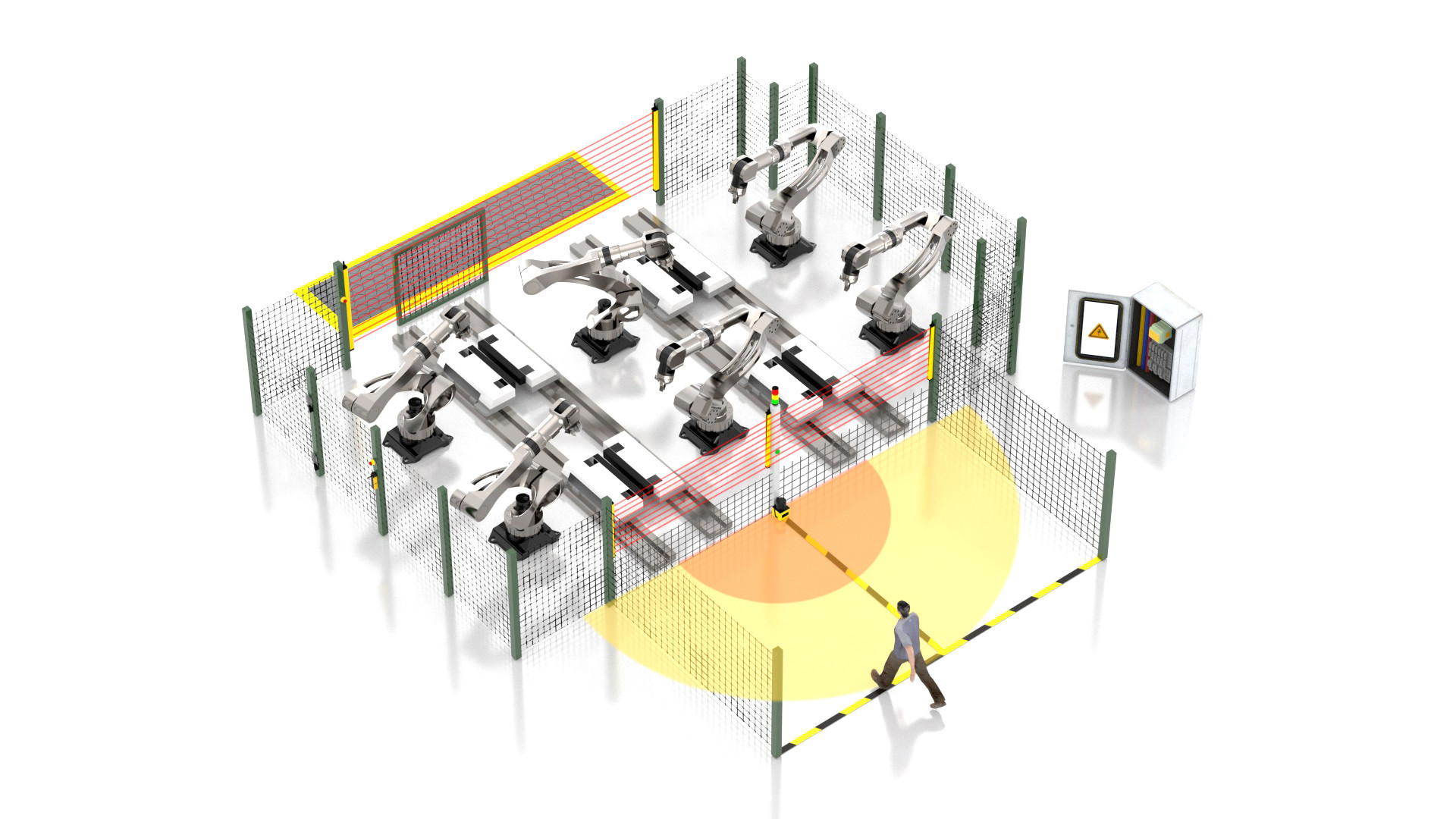
Safety relays are widely used in industrial automation systems, machinery and equipment, and power systems. In mechanical equipment, safety control relays can detect unexpected conditions (e.g., overload, overtemperature, etc.) and stop the equipment in time to prevent further damage or personal injury. In industrial automation systems, safety relays can monitor abnormal conditions that occur on production lines and trigger appropriate protective measures to protect workers and equipment. In power systems, safety relays can quickly switch and isolate equipment based on received fault signals to prevent the spread of accidents and further damage.
Safety relays are the best choice for reliability and efficiency. Dual channel safety relay signaling design and forced guided contact structure make them highly reliable and reduce the possibility of malfunction and failure. Emergency safety relay also improve overall safety performance. Safety relays are indispensable components in industrial electrical control systems.
Fundamentals of Electromagnetic Effects
Safety relays consist of electromagnetic relay components, which usually consist of a core, coil, armature, and contact reeds. When a certain voltage is applied to the ends of the coil, current flows through the coil, creating an electromagnetic effect. This electromagnetic effect will cause the armature to overcome the tension of the return spring under the attraction of the electromagnetic force and suction to the iron core. The armature's movement drives the moving contacts (normally open contacts) and static contacts (normally closed contacts) to either suction or release, completing the on or off in the circuit.
Safety relays have a dual-channel signaling design, which is a key feature of the operating principle. Dual-channel means that the relay must receive signals from two independent channels simultaneously, and the relay can operate properly only when the signals from both channels are normal. This design effectively eliminates false operation caused by a single point of failure and improves the safety and reliability of the system.
The safety relay is equipped with an internal logic controller responsible for making decisions based on preset logic conditions and input signals. The logic controller constantly monitors the signal status of both channels, and in the event of a signal interruption or abnormality in either channel, the logic controller immediately issues a command to stop the output of the relay and disconnect it from the controlled equipment. This prevents danger in the event of equipment failure or abnormality.
Safety relays also feature a forced guided contact construction that is specially designed to ensure safety in the event of an abnormal condition such as a melted contact. The forced guided contact construction ensures that even if a contact is melted, the relay will operate according to a predetermined rule and will not cause a dangerous situation such as short-circuiting or continuous energization of the circuit due to a melted contact.
Power supply: 24 V DC
Relay safety output: 3NO + 1NC (PNP or NPN)
Maximum switching capacity: 12 A (Distributed on all safety output contacts)
Transistor signal output: <500 mA 24 V DC
Contact resistance: <100 mΩ
Size: 117 × 100 × 22.5 mm
Shell material: flame retardant PA66
Storage temperature: -40℃ ~ 105℃
The workflow of a safety relay can be summarized in the following steps:
Receive signals: The safety relay receives signals from external sensors or manual control devices via the input module.
Logic decision: The logic controller makes a decision based on the preset logic conditions and the received signals.
Output control: If the signals from both channels are normal and the logic conditions are met, the logic controller sends a control signal to the output module.
Action execution: After receiving the control signal, the output module controls the controlled equipment to perform the corresponding action.
Failure protection: If either channel signal is interrupted or abnormal, the logic controller will immediately stop the output and disconnect from the controlled equipment to protect equipment and personnel safety.