2D LiDAR-Based Anti-Collision Solution for Gantry Cranes
- Share
- publisher
- Zoe
- Issue Time
- Jul 16,2025
Summary
In industrial environments where heavy-duty machinery such as gantry cranes, overhead cranes, or automated guided vehicles (AGVs) operate, ensuring safety within close-range working zones is critical. To prevent collisions with personnel, objects, or structural elements, safety laser scanners have become a preferred choice for real-time 2D zone monitoring.
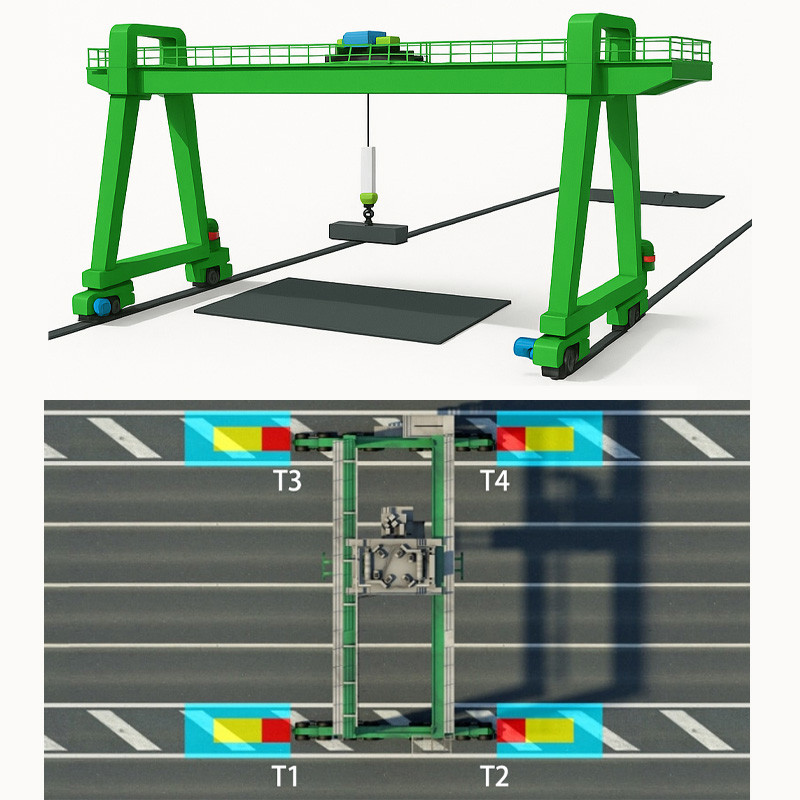
In heavy-duty industrial environments such as steel mills, ports, and automated warehouses, gantry cranes play a critical role in transporting oversized and heavy materials. However, due to their large span and long travel distances, they face high risks of collisions—whether with surrounding equipment, structures, or personnel. To address these challenges, a reliable and intelligent gantry crane anti-collision system is essential.
Intelligent Collision Avoidance Using 2D Safety Laser Scanners
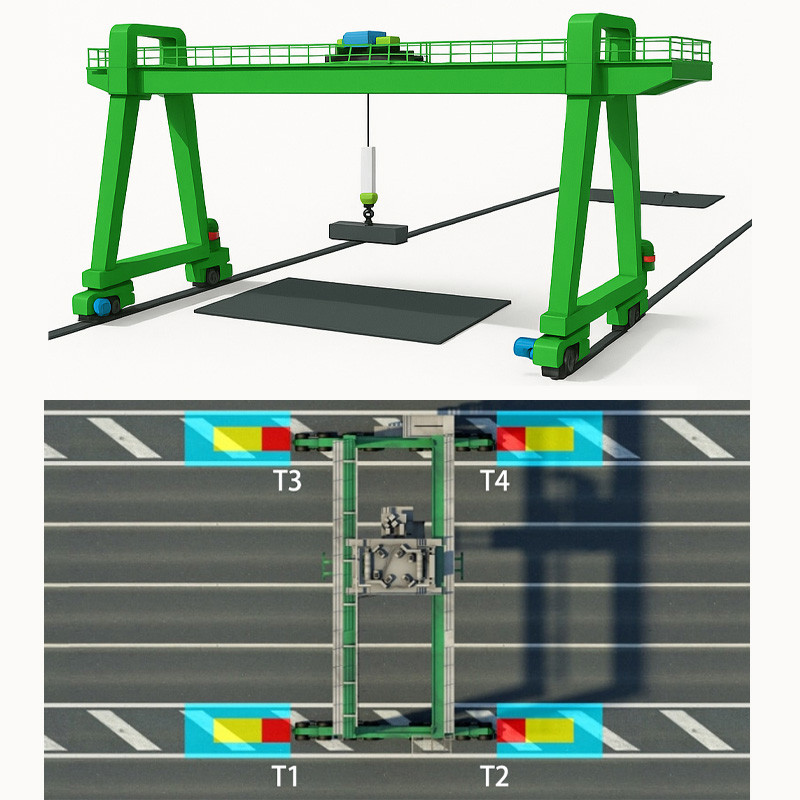
To ensure operational safety and efficiency, we offer a 2D LiDAR-based gantry collision avoidance solution designed specifically for large-scale gantry cranes. As illustrated above, four safety laser scanners (T1, T2, T3, and T4) are mounted on the lower sections of the crane legs, near each of the drive wheels. These scanners generate horizontal scanning planes aligned with the crane's motion direction, enabling comprehensive, real-time monitoring of the travel path.
Key Features:
✅ Bidirectional Safety Protection
Each 2D LiDAR provides real-time monitoring for both forward and reverse movements. No blind zones—ensuring complete perimeter awareness during gantry travel.
✅ High-Precision Obstacle Detection
With millimeter-level resolution, the safety laser scanners accurately identify track edges, potential obstacles, or intrusions in the travel path, triggering early warnings before a potential collision occurs.
✅ Customizable Detection Zones
The warning zones—represented in red, yellow, and blue—are programmable to suit specific safety logic. For example:
▪️🔴 Red: Emergency Stop Zone (immediate halt if obstacle detected)
▪️🟡 Yellow: Warning Zone (slow down or sound alarm)
▪️🔵 Blue: Safe Buffer Zone (entry allowed, monitoring only)
✅ System Integration & Intelligent Response
The scanners are fully integrated with the crane’s PLC or control system. When an obstacle or person enters a danger zone, the system can automatically trigger predefined responses such as speed reduction, audible alerts, or immediate shutdown.
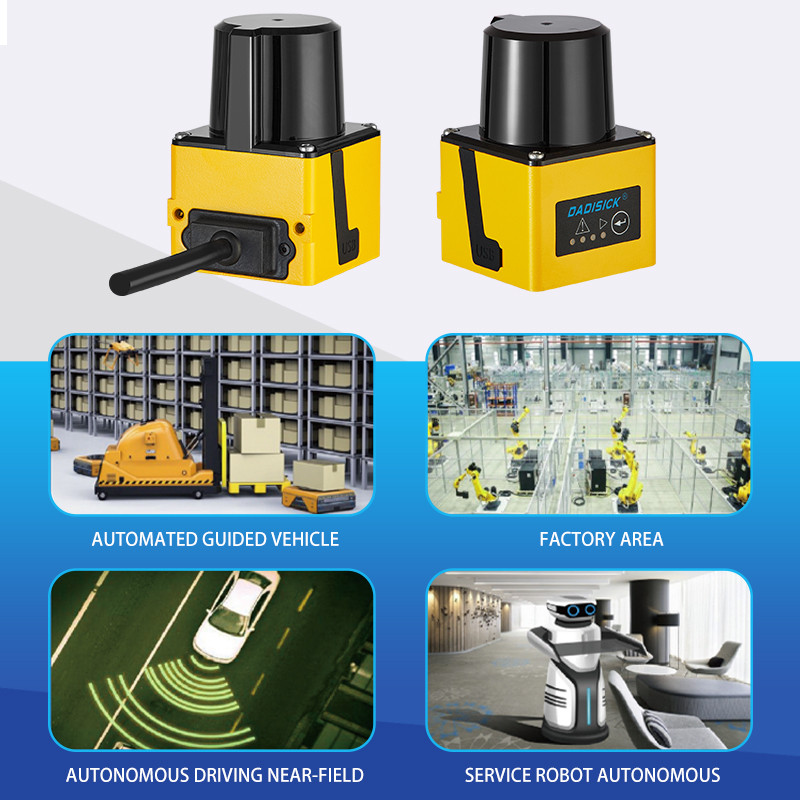
Recommended: Crane Collision Avoidance Sensors
1. 2D Laser Scanning (2D LiDAR)
▪️Performs horizontal 2D scanning to create a fan-shaped detection area on the ground.
▪️Non-contact detection with high accuracy for identifying humans, obstacles, and equipment within the scan range.
2. Maximum Detection Range: 5 Meters
▪️Ideal for short- to mid-range obstacle avoidance in applications such as gantry cranes, AGVs, robotic arms, and forklifts.
3. 270° Wide-Angle Scanning
▪️Covers a wide fan-shaped area, monitoring both sides of the rail and front/rear directions.
▪️Effectively eliminates blind spots in movement paths.
4. Programmable Multi-Zone Protection
▪️Supports three configurable zones (typically color-coded red, yellow, blue), representing warning, deceleration, and stop zones respectively.
▪️Each zone can be programmed with custom response logic (e.g., slow down, stop, trigger alarm).
Benefits for Gantry Crane Operations
▪️Improved Safety: Proactively prevents collisions with people, vehicles, or structures on or near the rails.
▪️Reduced Downtime: Avoids costly accidents or crane derailments caused by unexpected obstructions.
▪️Scalable Deployment: The modular design allows customization for different crane sizes, rail lengths, and operating environments.
▪️Enhanced Automation: Supports integration with industrial IoT systems for data logging and remote diagnostics.
Similar Posts You May Be Interested in