Detailed Explanation of Common Faults and Troubleshooting Methods for Safety Light Curtain Sensors
- Share
- publisher
- Zoe
- Issue Time
- Mar 24,2025
Summary
This article thoroughly explains the working principle of safety light curtain sensors in industrial automation, the common faults they may encounter, and the troubleshooting methods. It also provides daily maintenance tips to help users quickly identify issues and extend equipment life.
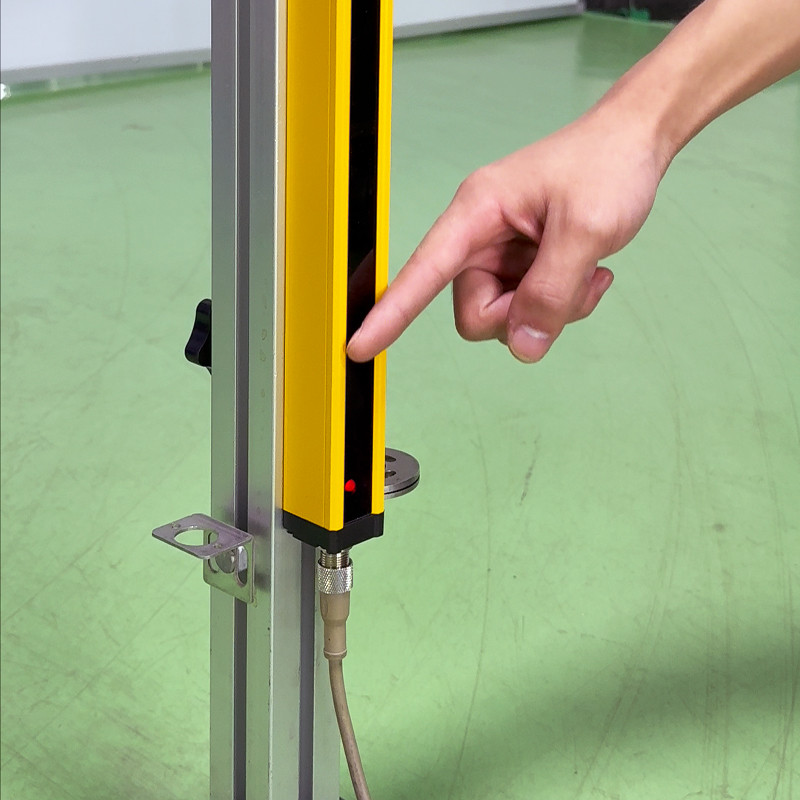
In the field of industrial automation, safety light curtain sensors serve as highly efficient and reliable safety protection devices. They are widely used in machinery, production lines, and various automation systems to provide effective protection for operators. This article explains the basic principles of safety light curtain sensors, details common faults and their troubleshooting methods, and combines daily maintenance and practical case studies to help readers fully grasp the operational characteristics of the equipment and strategies for addressing faults.
Safety Light Curtain Sensor Working Principle
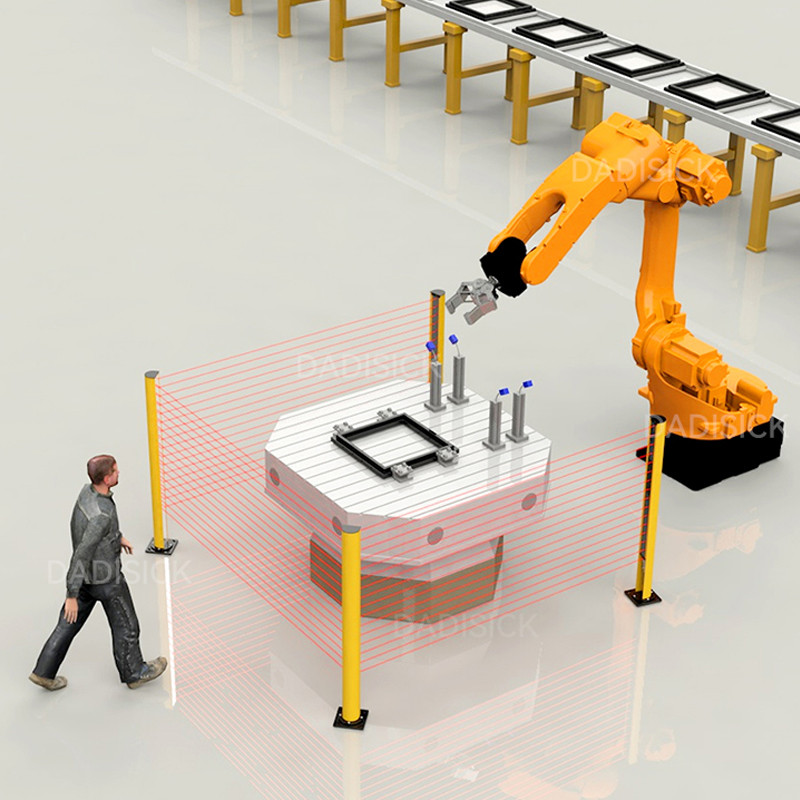
A safety light curtain sensor is a detection device that uses infrared light beams to form a virtual safety barrier, primarily used to monitor whether personnel or objects enter dangerous zones. Once an abnormality is detected, the device immediately triggers an emergency shutdown to prevent accidents. Due to its rapid response and easy installation, the safety light curtain sensor has been widely applied in automated production lines, assembly workshops, packaging machines, and other scenarios, providing reliable safety protection in industrial production.
The core working principle of a safety light curtain sensor is based on infrared sensing technology. Its main components include a transmitter and a receiver. The transmitter continuously emits infrared light beams, and when these beams are transmitted without interruption, the receiver picks up a stable signal. However, when someone or something enters the detection area, the light beams are blocked, reflected, or scattered, causing a change in the received signal. The controller continuously monitors these signal changes, and if it detects interference or intrusion within the safe zone, it immediately issues a shutdown or alarm signal, ensuring operational safety.
Safety Light Curtain Common Faults and Troubleshooting Methods
In practical applications, safety light curtain sensors may encounter various faults due to installation issues, environmental factors, or inherent device problems. Below, we detail several typical fault phenomena and their corresponding troubleshooting methods:
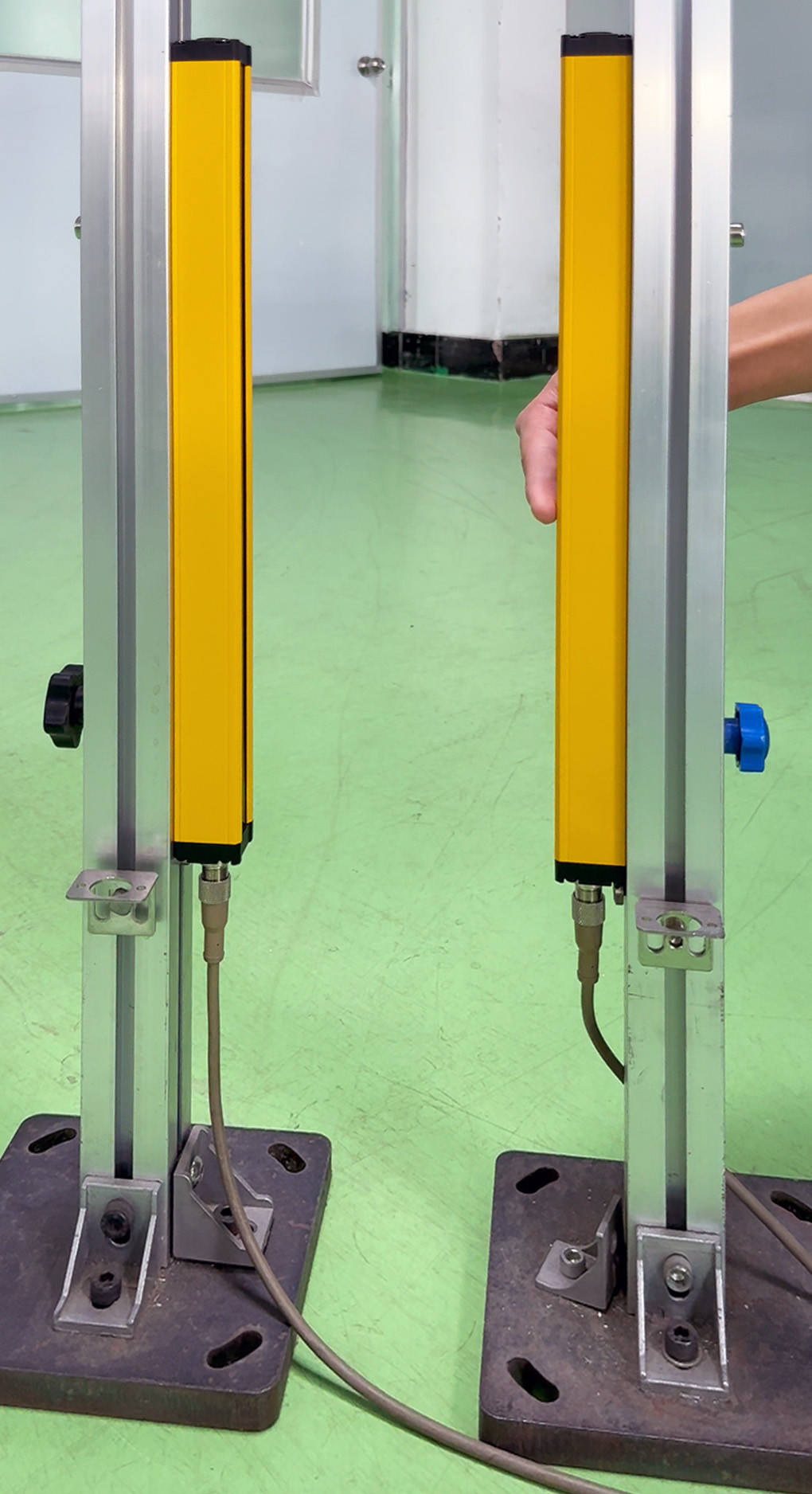
1. Light Curtain Fails to Align the Light Beams
Fault Phenomenon: The light beams from both ends of the curtain fail to align properly during operation, resulting in an incomplete safety barrier.
Troubleshooting Methods: Check if the installation distance exceeds the recommended maximum transmission range; if so, adjust the equipment positions accordingly. Ensure that the installation positions are properly aligned and level to avoid misalignment of the light beams. If the issue persists, the internal components of the light curtain might be damaged. In this case, contact the manufacturer for professional repair and calibration.
2. Indicator Lights Are Normal, but the Device Malfunctions
Fault Phenomenon: Although the indicator lights appear normal, the device fails to trigger the emergency stop or alarm functions.
Troubleshooting Methods: Check if strong ambient light is interfering with the infrared signal; if so, improve the lighting conditions or adjust the installation location. Confirm that the shielded cables are securely connected to prevent external electromagnetic interference from affecting the device signal. If the problem remains, inspect the signal reception module of the controller for potential faults.
3. Continuous Flashing of Red/Green Indicator Lights
Fault Phenomenon: The red and green indicator lights flash abnormally, indicating that the system is unstable.
Troubleshooting Methods: Verify that the shielded cables are properly grounded and that all electrical connections meet technical requirements. Check all connectors and interfaces for looseness or signs of aging. If any cable is found to be aged or damaged, replace it promptly to restore normal operation.
4. Occasional Abnormal Signal Output
Fault Phenomenon: Occasionally, the device outputs abnormal signals during operation, causing unintended actions or shutdowns.
Troubleshooting Methods: Inspect all connection points for loose plugs or insecure fittings; tighten screws if necessary. Verify that the supply voltage is within the normal range to prevent fluctuations from affecting the device’s performance. If abnormal signals occur frequently, use a multimeter to check the voltage and signal output at various interfaces for further diagnosis.
5. Communication Faults
Fault Phenomenon: Despite normal indicator lights, the safety light curtain sensor fails to output control signals or communicate properly with the host system.
Troubleshooting Methods: First, inspect all communication cables and output connectors for any looseness or physical damage.
Use a multimeter to test the voltage and signal at each interface to determine if there is a hardware fault. If the internal communication module is found to be faulty, it is recommended to send the device back to the manufacturer for professional repair to ensure stable operation.
Daily Maintenance and Upkeep of Safety Light Curtain Sensors
To ensure the long-term stable operation of safety light curtain sensors, daily maintenance and upkeep are as important as troubleshooting faults.
Regularly inspect the installation angles, transmission distances, and positions of the light curtains to ensure optimal working conditions.Keep the transmitters and receivers clean to prevent dust or oil stains from affecting the transmission of infrared light.Periodically check all fasteners to prevent loosening due to vibrations or long-term use.
When installing, try to avoid strong direct light sources. If necessary, use light shields or adjust indoor lighting conditions. In industrial environments, arrange the equipment to avoid close proximity to high-power electrical devices to prevent electromagnetic interference.
Establish a reasonable maintenance schedule (monthly, quarterly, or annually) based on the manufacturer’s guidelines and the operating environment. When facing complex faults or uncertain issues, promptly contact professional technicians or the manufacturer’s service center to ensure the maintenance work is handled safely and professionally. Keep detailed records of each inspection, cleaning, and component replacement to assist in future troubleshooting and system upgrades.
Regularly inspect the installation angles, transmission distances, and positions of the light curtains to ensure optimal working conditions.Keep the transmitters and receivers clean to prevent dust or oil stains from affecting the transmission of infrared light.Periodically check all fasteners to prevent loosening due to vibrations or long-term use.
When installing, try to avoid strong direct light sources. If necessary, use light shields or adjust indoor lighting conditions. In industrial environments, arrange the equipment to avoid close proximity to high-power electrical devices to prevent electromagnetic interference.
Establish a reasonable maintenance schedule (monthly, quarterly, or annually) based on the manufacturer’s guidelines and the operating environment. When facing complex faults or uncertain issues, promptly contact professional technicians or the manufacturer’s service center to ensure the maintenance work is handled safely and professionally. Keep detailed records of each inspection, cleaning, and component replacement to assist in future troubleshooting and system upgrades.
Safety Light Curtain Frequently Asked Questions
Q: Why does the device sometimes fail to trigger an emergency stop even when the indicator lights appear normal?
A: This may be caused by strong ambient light interfering with the infrared signal or by poor connections in the shielded cables. It is advisable to check the installation environment and electrical connections, and, if necessary, adjust the light sources or implement interference prevention measures.
Q: How can I tell if flashing indicator lights indicate a fault?
A: Continuous flashing of the red/green lights usually indicates abnormal signals or grounding issues. First, check the shielded cables and connection interfaces for any physical damage. Then, use testing equipment to verify the stability of the signal and ensure the circuitry is functioning properly.
Q: How should I determine the maintenance schedule for the safety light curtain?
A: It is recommended to follow the manufacturer’s guidelines and tailor the maintenance schedule (monthly, quarterly, or annually) to the operating environment. Adjust the schedule as necessary based on the device’s operational performance to ensure it remains in optimal condition.
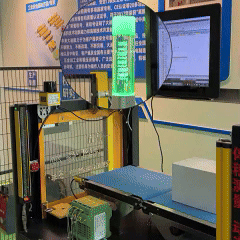
Related Safety Sensors
Beam spacing:40mm
Number of optical axes: 32
Protection height: 1240mm
Safety-light-curtain outputs (OSSD):1 PNP
Beam spacing: 40mm
Number of optical axes: 32
Protection height: 1240mm
Safety Curtain outputs (OSSD):2 PNP
Beam spacing: 200mm
Number of optical axes: 22
Protection height: 4200mm
Safety Curtain outputs (OSSD): 2 PNP