How Can Cranes Communicate to Prevent Collisions?
- Share
- publisher
- Zoe
- Issue Time
- Apr 22,2025
Summary
Discover how ST100 Optical Data Transmission Modules enable real-time, interference-free communication between cranes, enhancing safety and efficiency.
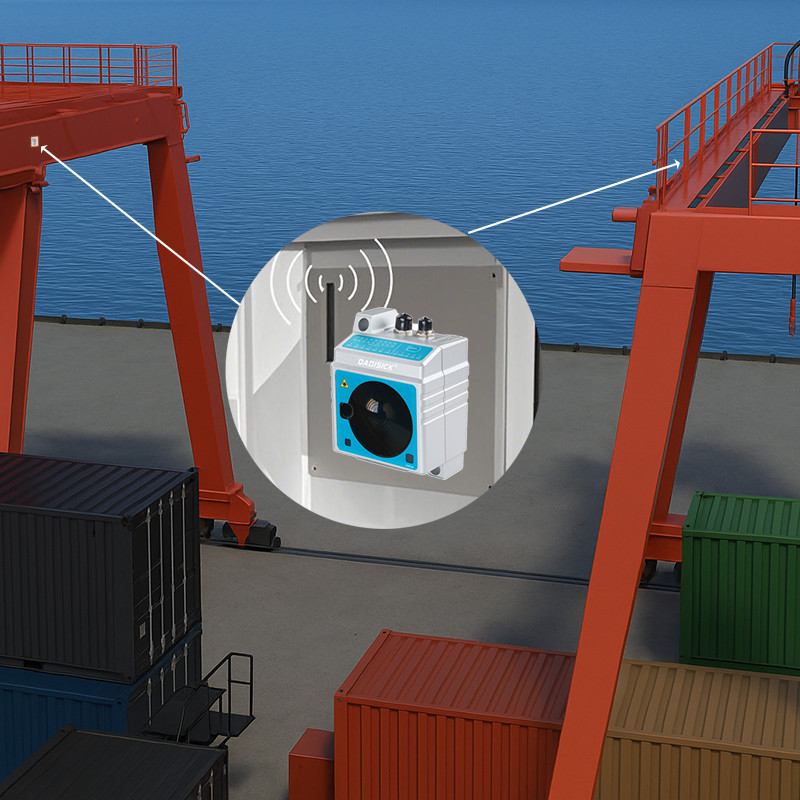
How Can Cranes Communicate to Prevent Collisions?
Optical Data Transmission (ODT)—uses light pulses instead of cables or radio waves to link multiple cranes in crowded port or yard environments. By eliminating messy wiring and resisting electromagnetic interference, Optical data transmission modules like the ST100 series deliver ultra‑low latency, high‑precision positioning, and rock‑solid reliability, enabling cranes to share real‑time position and status data, avoid collisions, and boost throughput.
Why Crane‑to‑Crane Communication Matters?
In modern automated terminals, two or more gantry cranes often operate side by side on the same rails or within tight aisles. Efficient, accurate, and fail‑safe data exchange is vital to:
Prevent collisions when containers or trolleys overlap work zones.
Coordinate lifting sequences to reduce idle time and maximize throughput.
Synchronize diagnostics & maintenance alerts without disrupting operations.
Traditional wiring is expensive, cumbersome, and prone to mechanical wear. Conventional wireless (Wi‑Fi, Bluetooth) can suffer from EM noise, multipath fading, and security gaps.
How Does Optical Data Transmission Module Work?
The ST100 series leverages infrared or visible‑light pulses to transmit data through free space:
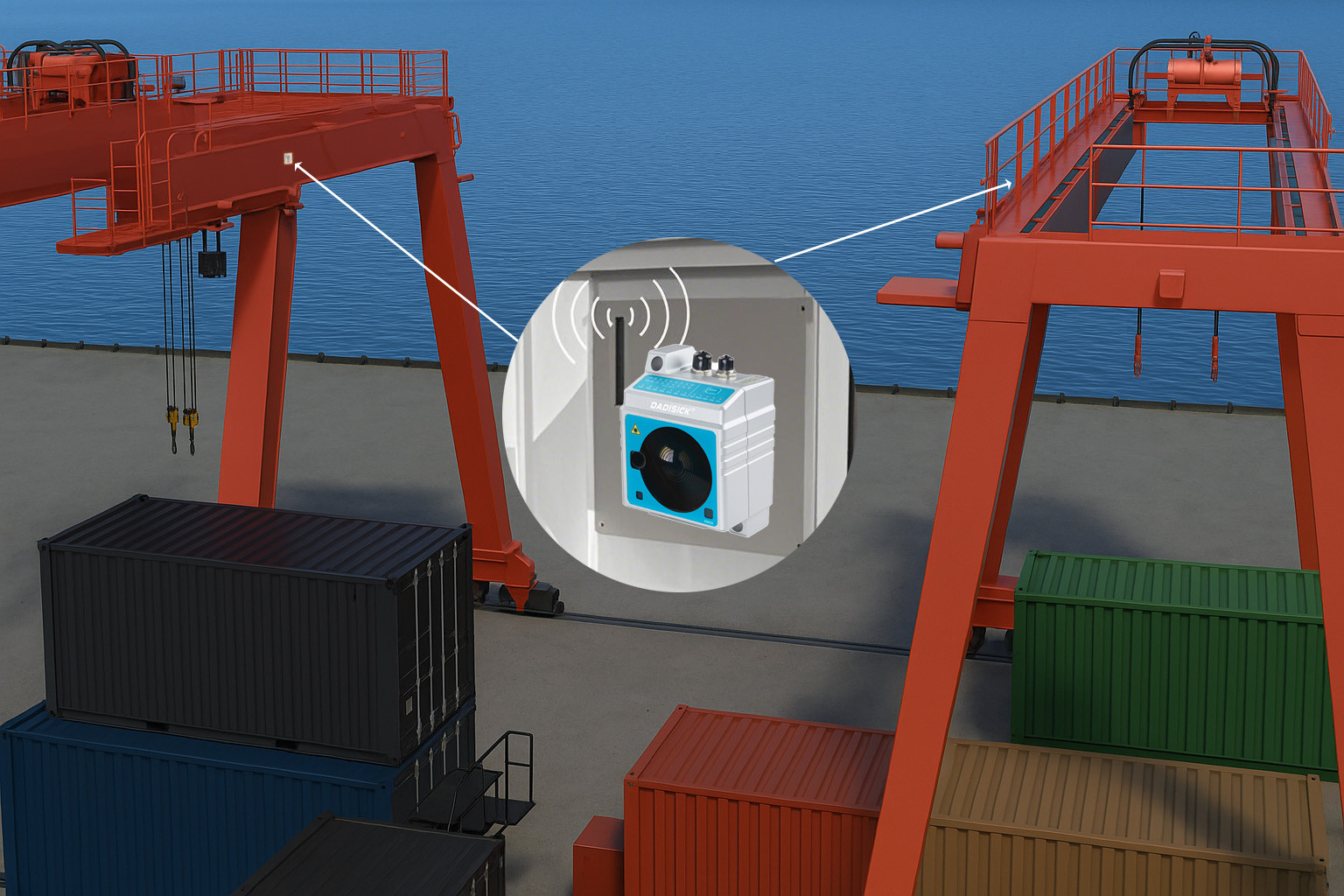
1. Data Encoding & Emission
• A controller (PLC or industrial PC) sends digital position, speed, or command data to the ST100.
• The ST100 converts these bits into a train of high‑frequency light pulses (laser or LED).
2. Free‑Space Optical Link
• Light pulses travel in straight lines between crane‑mounted transceivers—no cables, no connectors.
• Point‑to‑point beams ensure a focused, interference‑free path.
3. Reception & Decoding
• The remote unit’s photodetector captures the pulses, converts them back into an electrical data stream, and forwards it to the destination controller.
Key Benefits:
Cable‑free: Zero wiring between moving cranes.
Low latency: Sub‑millisecond round‑trip times.
Secure & interference‑immune: No RF leakage or EMI concerns.
Advantages of ST100 Optical Data Transmission in Crane Operations
1. Ultra‑Precise Collision Avoidance
By continuously sharing real‑time X/Y position and velocity vectors, cranes can dynamically adjust travel speeds and stop‑zones, eliminating blind‑spot risks and container‑clash incidents.
2. Real‑Time Control & Diagnostics
Millisecond‑level updates allow centralized or distributed control systems to orchestrate lift/drop cycles, optimize container sequencing, and issue predictive maintenance alerts before failures occur.
3. Robust Performance in Harsh Environments
Optical links are unaffected by heavy machinery’s electromagnetic fields, extreme humidity, or dusty atmospheres—delivering reliable uptime even in the world’s busiest ports.
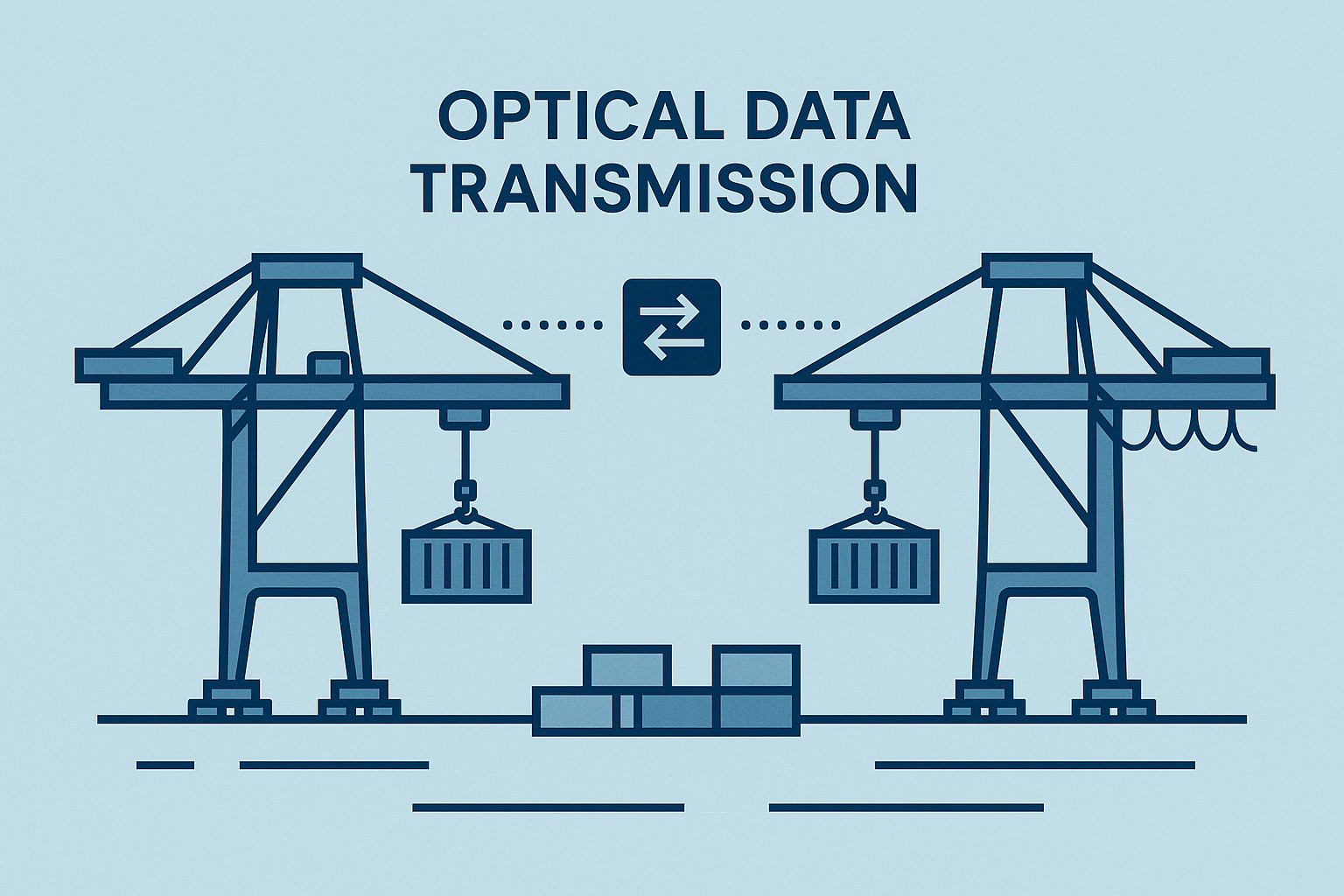
Recommended Optical Data Transmission Module
Optical Data Transmission Module ST100 Series | ||||
Models | ||||
Effective transmission distance | 80m | 120m | 200m | |
Communication rate | 100Mbit/s | |||
Communication light divergence angle | 1° | |||
Communication light receiving angle | 1.5° | |||
Power supply voltage | DC 10V-30V | |||
Power consumption | 3W (max) | |||
Data transmission interface | Ethernet | |||
Protection level | IP65 | |||
Dimensions | 102 * 84 * 140.5 mm |
Related Products
Measuring frequency: 1000Hz
Data transmission interface: SSl, Ethernet 100 BASE-TX
Measuring distance: 200m
Measurement accuracy: ±2 mm
Measuring frequency: 1000Hz
Data transmission interface: SSl, Ethernet 100 BASE-TX
Measuring distance: 120m
Measurement accuracy: ±2 mm
Eective transmission distance: 200 m
Communication rate: 100 Mbit/s
Communication light divergence angle: 1°
Communication light receiving angle: 1.5°
Eective transmission distance: 120 m
Communication rate: 100 Mbit/s
Communication light divergence angle: 1°
Communication light receiving angle: 1.5°