Smart Liquid Level Monitoring with Ultrasonic Level Sensor in Laboratory and Medical Applications
- Share
- publisher
- Zoe
- Issue Time
- Apr 12,2025
Summary
In advanced laboratory automation and medical microdispensing systems, ensuring precise and reliable liquid level detection is critical. This is where ultrasonic level sensors play an increasingly important role.
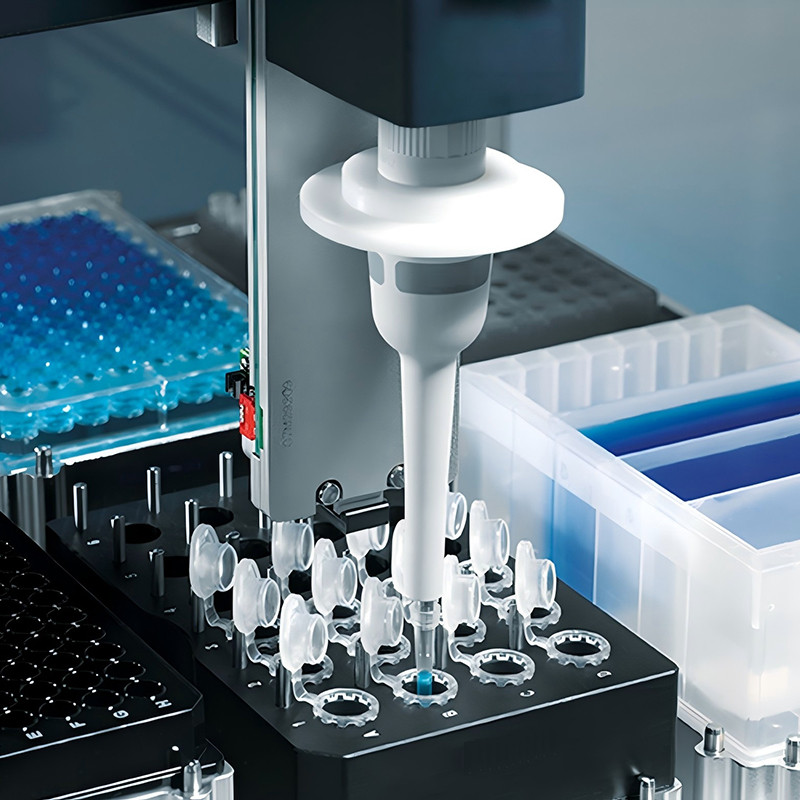
Smart Liquid Level Monitoring with Ultrasonic Level Sensor in Laboratory and Medical Applications
In advanced laboratory automation and medical microdispensing systems, ensuring precise and reliable liquid level detection is critical. This is where ultrasonic level sensors play an increasingly important role.
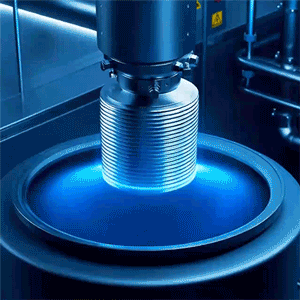
Why Use Ultrasonic Level Sensor for Liquid Level Detection?
Ultrasonic level sensors utilize the properties of sound waves to provide a non-contact and highly accurate solution for detecting object status and distance. The sensor emits high-frequency mechanical sound waves, and when these waves encounter an object, they are reflected back. By calculating the time interval or energy difference between the emitted and received waves, the sensor determines the exact distance or state of the target object.
Unlike conventional proximity switches or photoelectric sensors, ultrasonic level sensors offer several advantages. Compared to inductive or capacitive proximity switches, they support longer detection distances. Compared to photoelectric sensors, ultrasonic level sensors are less affected by harsh environmental conditions, such as the color of the target object, dust, or mist in the air. These fundamental differences offer a range of benefits, especially in sensitive environments like laboratories and medical devices.
✅ Non-Contact and Contamination-Free
Ultrasonic level sensors operate without physically touching the liquid or container. This non-contact fluid detection capability is vital for laboratory environments, where avoiding cross-contamination and ensuring sterile conditions are critical.
✅ Resistant to Environmental Conditions
These sensors are unaffected by humidity, dust, or the color and transparency of the medium, ensuring stable and accurate detection even in challenging environments.
✅ Versatile Across Different Media
Whether you're measuring water-like liquids, viscous reagents, or even foam-topped fluids, ultrasonic liquid level sensors maintain consistent performance regardless of the liquid's viscosity or optical properties.
Ultrasonic Level Sensors Key Applications in Lab Automation and Medical Systems
1. Microdispensing Systems
In the preparation of microneedle patches or drug delivery carriers, tiny droplets must be precisely dispensed into micro-wells. Ultrasonic level sensors can provide real-time monitoring of:
Liquid levels in storage bottles or tubes within the dispensing system.
Presence of residual liquid before and after dispensing.
Automated refilling or alert control functions.
2. Automated Pipetting Workstations
In fully automated reagent handling systems, monitoring the remaining volume of liquids is crucial for ensuring continuous workflows. Ultrasonic level sensors can be integrated beneath pipetting heads or reagent storage modules to:
Detect if reagent bottles are nearing depletion.
Support simultaneous multi-channel level detection.
Prevent air bubble aspiration caused by incorrect operation.
3. Medical Production Automation
On production lines for injectables, inhalation drug filling, or tablet packaging, ultrasonic level sensors play a vital role by:
Detecting whether drugs (such as tablets or capsules) are correctly positioned.
Verifying whether blow-molded packages are properly filled.
Supporting compact, integrated deployment on complex robotic arms.
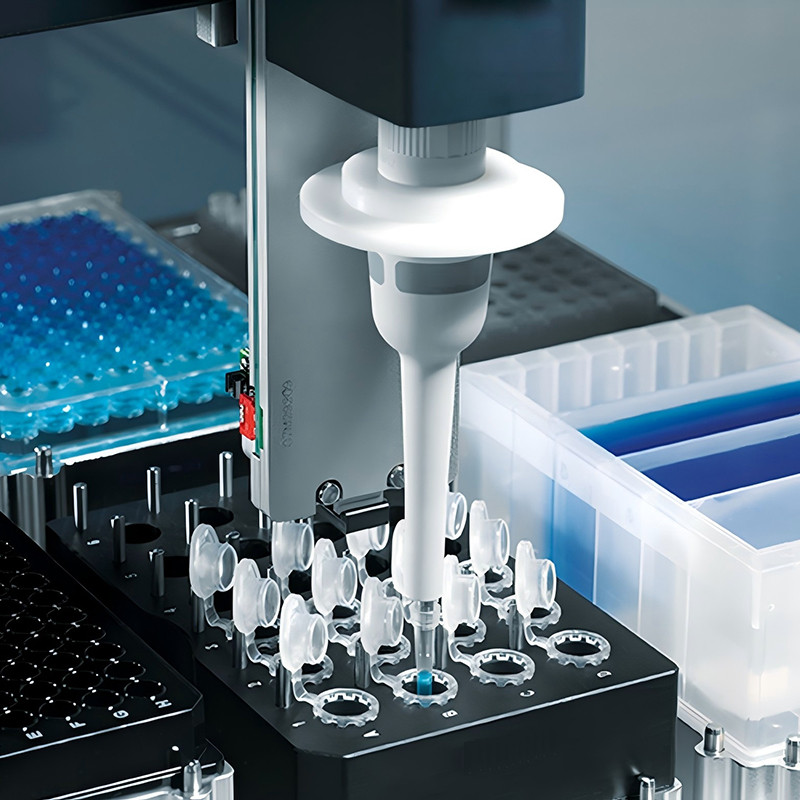
Your Possible Solution: CSB12 Series Ultrasonic Level Sensor for Level Monitoring
Models
|
CSB12-120 |
CSB12-200 |
Detection range | 20-120 mm | 20-200 mm |
Blind zone
|
0-20 mm |
|
Resolution
|
0.1 mm |
|
Response time | 18 ms | 22 ms |
Switching hysteresis | 1 mm | |
Switching frequency | 55 Hz | 45 Hz |
Repeatability: ±0.15% of full-scale value | ||
Absolute accuracy: ±1 % (built-in temperature drift compensation) | ||
Input type: With synchronization and learning function | ||
Output type: Switch output; IO-Link output; Analog output; Digital output RS485 | ||
Material: Copper nickel plating , plastic fittings , glass filled epoxy resin | ||
Connection type: 4-pin M12 connector | ||
Protection Class: IP67 | ||
Ambient temperature: -25°C~+70°C (248~343K) |
Ultrasonic Level Sensors Benefits Over Optical or Mechanical Sensors
Feature | Ultrasonic Level Sensor | Optical Sensor | Mechanical Sensor |
Contactless | ✅ Yes | ✅ Yes | ❌ No |
Transparent liquid detection | ✅ Reliable | ❌ Unstable | ✅ Good |
Foam/liquid interface detection | ✅ Effective | ❌ Poor | ❌ Poor |
aintenance-free | ✅ Yes | ❌ May require cleaning | ❌ Moving parts |
Related Ultrasonic Sensors
Emitter - receiver spacing: 20-40 mm, 20-60 mm, 20-100 mm
Material: nickel plated copper, plastic fittings
Connection type: 2 m, PVP cable, 0.14 mm²
Detection range: 100-2000 mm
Material: plastic accessories, filled with epoxy resin
Connection type: 5-pin M12 connector
Output method: 1 NPN, NO/NC
Groove depth: 68 mm
Slot width: 5 mm
Material: metal, aluminum
Connection type: 4-pin M8 connector
Detection range: 30-300 mm, 50-500 mm, 60-1000 mm
Material: copper nickel plating, plastic fittings
Connection type: 5-pin M12 connector